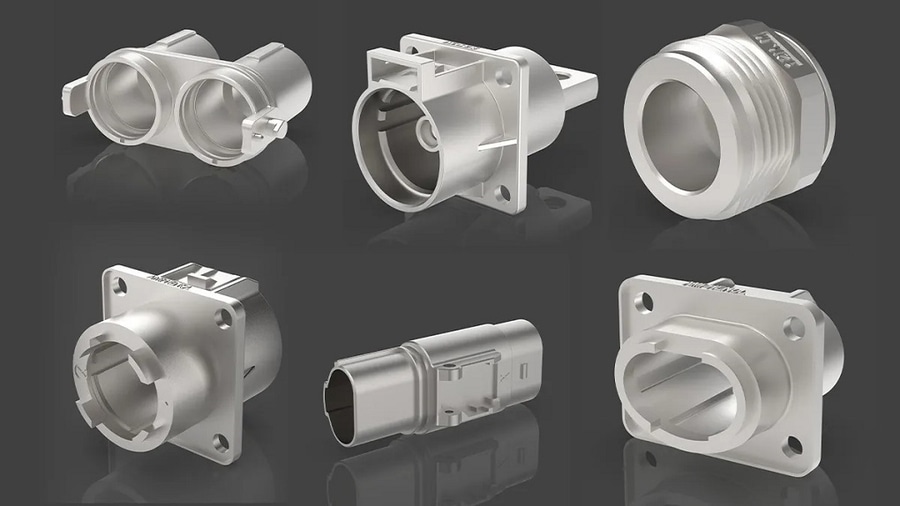
#Industry News
hot chamber die casting VS cold chamber die casting
two common metal die casting
During the hot die casting process, the metal is preheated to a certain temperature before being injected into the mold, usually through electric furnaces, induction heating, to improve its fluidity and filling properties. During the injection process, the metal enters the mold in a liquid or partially solid state.
The selected metal material is pre-processed into a suitable form, usually in block or granular form. The metal material is directly filled into the cavity of the mold using pressure or extrusion, and is cooled and solidified after applying pressure.Pressure is usually provided by a hydraulic system.
▶Features: Hot die casting requires high temperature, usually higher than the melting point of the metal; while cold die casting does not require preheating the metal.
▶Metal state: Hot die casting injects the metal into the mold in a molten state, while cold die casting injects the metal into the mold in a solid or semi-solid state.
▶Production speed: The production speed of hot die casting is relatively slow, while the production speed of cold die casting is relatively fast.
▶Energy consumption: Hot die casting consumes more energy and needs to heat the metal to a high temperature; while cold die casting consumes less energy and does not need to preheat the metal.
▶Forming accuracy: Hot die casting has high forming accuracy, while cold die casting has lower forming accuracy and may be affected by metal fluidity.
▶Surface quality: The surface quality of hot die casting is better, with fewer pores and defects, while the surface quality of cold die casting is relatively poor and may contain pores and defects.
▶Applicable materials: Hot die casting is suitable for high melting point metals such as aluminum and copper, while cold die casting is suitable for low melting point metals such as zinc and lead.
▶Applicable scenarios: Hot die casting is suitable for scenarios that require high precision and surface quality, while cold die casting is suitable for scenarios that require rapid production and low cost.