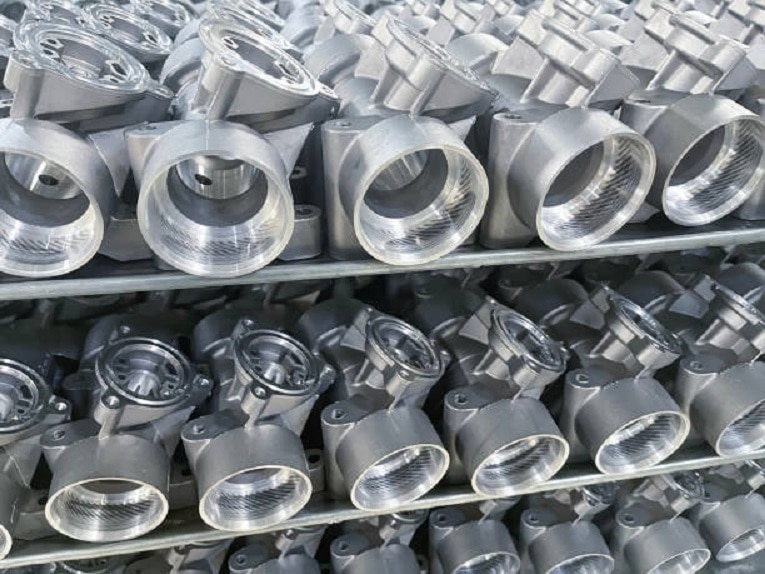
#Industry News
What Is Aluminum Die Casting
Definition and Advantage
The aluminum die casting process is a standardized method for creating aluminum alloy components featuring intricate geometries. Typically composed of aluminum, silicon, copper, and other alloys, the aluminum alloy serves as the primary raw material.
During aluminum die casting, the alloy undergoes heating and melting before being injected into a metal mold of the desired shape. Through high-pressure injection and rapid cooling, the molten aluminum solidifies swiftly, forming the desired component. This method offers numerous advantages, particularly in crafting parts with complex configurations.
Aluminum boasts lightweight properties alongside impressive strength and stiffness, rendering die castings lighter than their traditional cast iron counterparts while maintaining ample durability.
Additionally, aluminum's commendable thermal and electrical conductivity makes it a preferred choice for applications necessitating efficient heat dissipation or electrical conduction, such as radiator construction, automotive engine components, and electronic enclosures.
Moreover, aluminum die casting enables the production of intricately shaped components with precise dimensions. Molds are crafted with exceptional precision, ensuring heightened product accuracy and superior surface quality.
The production process generates waste materials and cutting residues, which can be recycled and reused, thereby curbing resource wastage and mitigating environmental pollution.