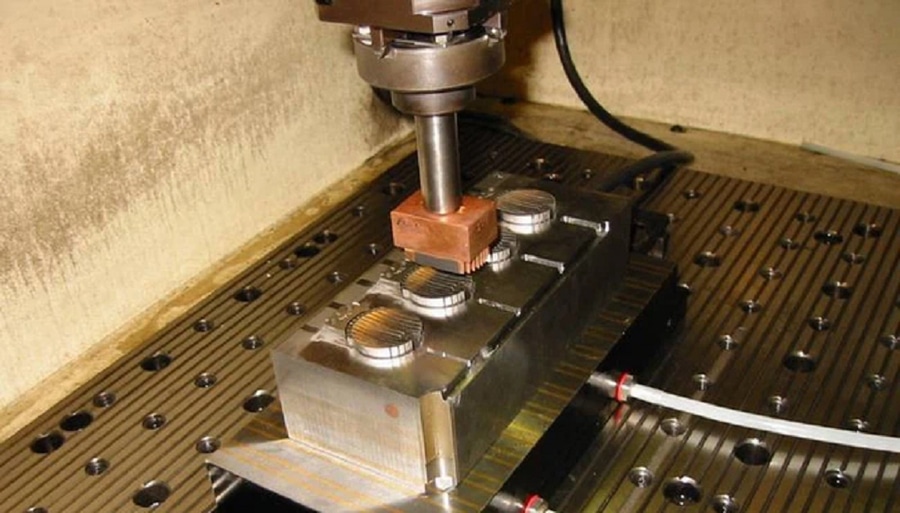
#Industry News
Electrical discharge machining (EDM)
precision machining and multi-field applications
Electrical discharge machining (EDM) is an advanced machining technology that demonstrates strong machining capabilities under project requirements that challenge traditional machining methods. This article will introduce the processing capabilities of EDM and its applications in areas such as mold manufacturing, rapid prototyping, small batch production, and direct part processing.
1.Precision Machining:
The EDM process can achieve tight tolerances of +/- 0.004 mm (±0.0001 inches) and surface roughness up to 0.18 micron Ra smoothness. This high-precision machining capability makes EDM one of the important processes in the manufacturing field.
2.Complex geometric shapes:
EDM can create 3D complex cavities, internal gears, deep holes and grooves with high precision, making it easier and feasible to manufacture complex parts.
3.Blind and through holes:
Through EDM technology, blind holes that do not completely penetrate the material and through holes that penetrate the entire workpiece can be realized to meet the processing needs of different parts.
4.Non-contact processing:
Since the electrode does not have physical contact with the workpiece during processing, the mechanical stress is minimal and there is no tool wear, effectively reducing part processing losses.
For manufacturers, EDM is an essential tool to meet high production demands, providing significant advantages:
1. Mold manufacturing:
EDM is widely used to manufacture molds and dies for plastic injection, metal casting and forging. It can produce high-precision complex cavities and cores, providing key technical support for long-term production mold manufacturing.
2. Rapid prototyping and small batch production:
EDM facilitates rapid prototyping, accelerating the design process and enabling iterative improvements before entering mass production. Its flexibility makes it possible to quickly adjust designs or settings, making it ideal for low-volume, high-variety production.
3. Direct processing of parts:
EDM dies can process final parts directly from solid blocks of conductive material, and are especially suitable for manufacturing parts with complex shapes or features. This direct processing method has important applications in aerospace, automotive, medical and electronic products and other fields, ensuring the accuracy and durability of parts.
To sum up, EDM, as an advanced processing technology, has significant advantages in precision processing, complex shape manufacturing and multi-field applications, and brings new opportunities and challenges to the development of the manufacturing industry.If you would like more information, please click on the link below.