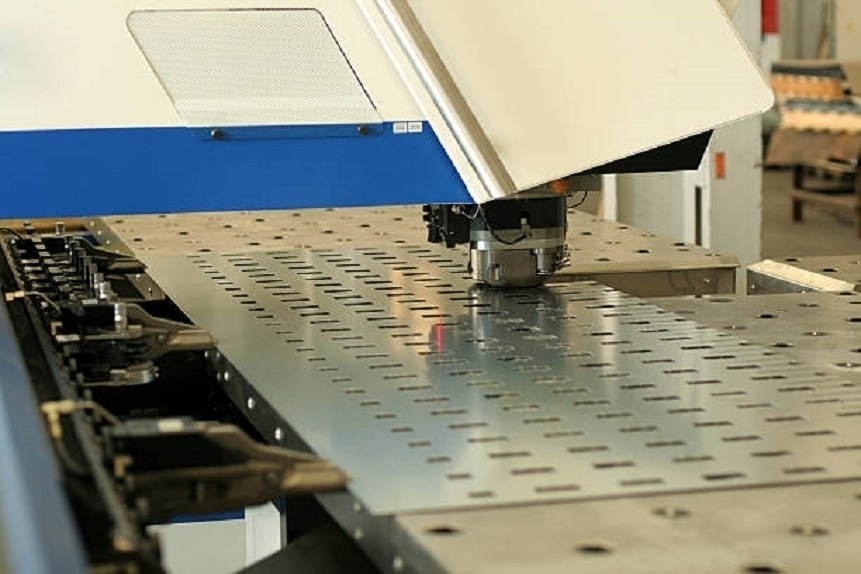
#Industry News
Exploring the Types of Punching Machines
Advantages and Disadvantages
In the world of manufacturing, selecting the right punching machine is crucial for optimizing productivity, precision, and cost-efficiency. There are several types of punching machines available, each with its unique set of advantages and disadvantages. Let's dive into the specifics of each type to understand their unique features and determine which might be the best fit for your needs.
Mechanical Press
Mechanical presses are known for their simple and robust design. These machines offer several benefits, making them a popular choice in various industries. One of the primary advantages of a mechanical press is its lower initial cost compared to hydraulic presses. This makes it an attractive option for businesses looking to manage their budgets effectively. Additionally, mechanical presses are well-suited for high-speed operations, ensuring quick and efficient production cycles.
However, mechanical presses do come with some limitations. Their force capacity is generally lower compared to hydraulic presses, which can be a drawback for tasks requiring significant pressure. Furthermore, mechanical presses offer less precise control over pressing parameters, which may not be ideal for applications needing high precision.
Hydraulic Press
Hydraulic presses stand out for their high force capacity and precise control over pressing parameters. These machines are incredibly versatile, making them suitable for a wide range of operations. Whether you need to perform deep drawing, forming, or any other high-force tasks, a hydraulic press can handle it with ease.
The trade-off, however, is a higher initial investment compared to some other press types. Additionally, hydraulic presses may require more maintenance due to the complexity of their hydraulic components. Despite these drawbacks, the precision and versatility of hydraulic presses often justify the additional costs and maintenance efforts.
Pneumatic Press
For those seeking quick cycle times and simple operation, pneumatic presses are an excellent choice. They offer lower initial costs compared to hydraulic presses, making them accessible for smaller operations or those just starting.
Nonetheless, pneumatic presses share some of the limitations seen in mechanical presses. They have a limited force capacity and provide less precise control over pressing parameters. These factors might restrict their use to applications where high force and precision are not critical.
Servo Press
Servo presses are designed for applications requiring high precision and control over pressing parameters. They are also known for their energy-efficient operation, which can lead to significant cost savings over time. The ability to handle complex and high-precision tasks makes servo presses a valuable asset in advanced manufacturing settings.
The primary downside is their higher initial investment and the need for skilled operators to handle setup and programming. Despite the higher upfront cost, the long-term benefits of precision and efficiency can make servo presses a worthwhile investment.
C-Press
C-presses feature an open-front design, allowing for easy access to the work area. Their space-saving design makes them ideal for workshops with limited floor space. These presses are versatile and can be used for various operations, adding to their appeal.
However, C-presses typically have lower tonnage capacity compared to other press types, which can limit their use in heavy-duty applications. Additionally, potential rigidity issues might affect their performance under high loads.
H-Type Press
H-type presses are known for their sturdy construction, offering stability and rigidity during operations. They have a high force capacity and are versatile, making them suitable for heavy-duty applications. These presses are reliable and can handle demanding tasks with ease.
The main drawbacks are their higher initial investment and the larger space requirement due to their size. Despite these disadvantages, their robust construction and high force capacity make H-type presses a solid choice for heavy-duty operations.
Four-Column Press
Four-column presses boast a robust construction that ensures stability and durability. With a high force capacity, these presses are versatile and suitable for heavy-duty applications. Their design provides the reliability needed for demanding manufacturing processes.
The larger footprint of four-column presses may require more space, and the higher initial investment can be a consideration. Nevertheless, their durability and high performance often outweigh these disadvantages.
Multiple Position Press
Multiple position presses excel in multi-station capability, allowing for simultaneous processing and high productivity. Their versatility makes them suitable for various operations, making them a favorite in high-volume production environments.
The higher initial investment and the need for skilled operators for setup and operation can be seen as drawbacks. However, the efficiency and productivity gains from using multiple position presses can justify the higher costs and training requirements.
Progressive Die Press
Progressive die presses are designed for continuous processing of multiple operations in a single pass, which leads to high productivity. They are particularly suitable for high-volume production, making them indispensable in mass manufacturing settings.
The higher initial investment and the requirement for specialized tooling and setup can be challenging. Yet, the continuous and efficient operation of progressive die presses often makes them a cost-effective solution for large-scale production.
For more information and how to choose the right metal punch, please click the link below for details.