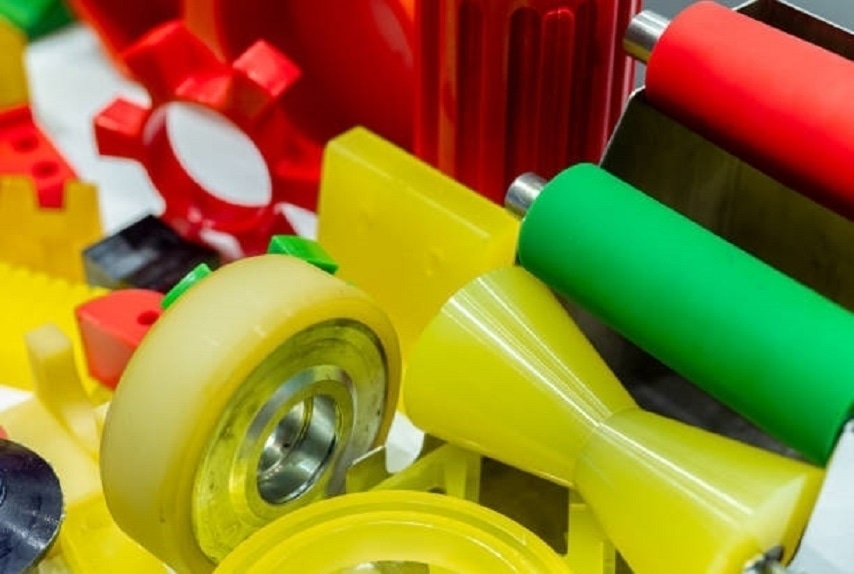
#Industry News
what is vacuum casting
How Does Polyurethane Casting Work?
Urethane casting is also called polyurethane casting or vacuum casting.
Vacuum casting pours polyurethane and additives into a mold and sets it. The vacuum chamber is used to remove air from the mold to ensure that the object has the correct shape.
Step 1: Design the 3D model
Understand product requirements and analyze them to create a perfect 3D model. Things to note when designing polyurethane castings:
Step 2: Create a main widget
The master model is the positive model from which the replica is derived through casting. Main components are usually produced using splicing, CNC machining or 3D printing. Nowadays, SLA resin or nylon powder is commonly used for 3D printing, and then the printed parts are ground, polished or sandblasted.
Step 3: Make the Silicone Mold
Before making the silicone mold, we need to prepare a proper casting box. Place the master model into the casting box and make sure there is enough space around the model while adding locations for the core, inserts and gates.
In the casting box, the core, inserts and gates are added by hanging the main model, and the exhaust pipe is installed. Use a vacuum pump to create a vacuum inside the casting box to remove air bubbles. Slowly pour the silicone around the master model, making sure to fill the entire mold and capture all the details of the master model.
Place the casting box in an oven at 40°C to cure the silicone, the time will depend on the type and thickness of the silicone.
When the silicone has cured, carefully remove the mold from the casting box. Use a knife to carefully cut open the mold to expose the negative cavity of the part.
Step 4: Mix Polyurethane Resin
Prepare the resin: Heat the polyurethane resin to around 40°C to ensure fluidity.
Mix: Mix the two components of polyurethane resin and add color and fillers as needed, making sure to mix evenly.
Step 5: Pouring and Vacuuming
Casting resin: Slowly pour the mixed polyurethane resin into the silicone mold, making sure the filling is complete and there are no voids.
Vacuum treatment: Start the vacuum pump to evacuate the air from the mold to ensure the resin fully fills the mold and expels air bubbles.
Step 6: Curing and Demolding
Curing: Put the resin-filled mold into the oven to cure. The time and temperature depend on the type and thickness of the resin.
Demold: When the resin has cured, carefully remove the product from the silicone mold, making sure not to damage the product or the mold.
Step 7: Post-processing
Conduct quality inspections on products to ensure size and appearance meet requirements.
Through the above steps, we can produce polyurethane casting products with high precision and quality, suitable for small and medium-sized batch production and prototype production.