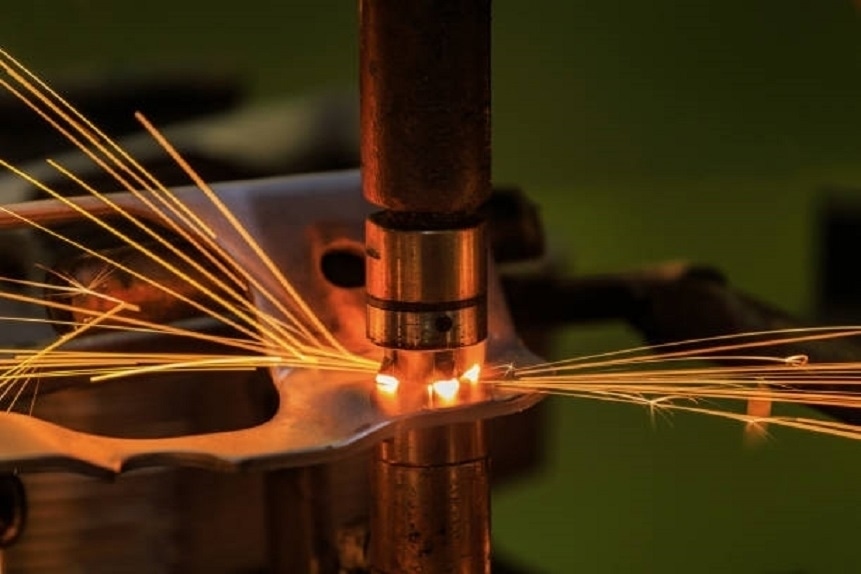
#Industry News
Spot Welding And MIG
The difference between the two
One type of resistance welding is spot welding. The metal melts and forms a local connection at the contact sites of the metal plates when high current and pressure are applied through the electrodes. The contact surface is locally heated by the current flowing through the electrodes, causing it to melt and produce a weld area. The current is cut off after the weld is finished, and the electrodes keep applying pressure until the weld spot cools and hardens.
Gas metal arc welding, or MIG (metal inert gas welding), is a popular welding technique that may be used on a range of metal materials. A continuous filler wire is used as the electrode in MIG welding, and it fuses with the workpiece through an arc to create a weld connection. An inert gas, like argon or helium, or a mixed gas, like argon and carbon dioxide, shields the weld pool from contamination and oxidation during the welding process.
Disparities between the two strengths: MIG welding, which is appropriate for structural applications and thicker materials, often results in stronger welds because the weld bead is continuous and has a deeper penetration depth.
Application suitability: MIG welding is more adaptable and can handle a wider range of material thicknesses and joint configurations than spot welding, which is best suited for high-speed, high-volume manufacturing of thin sheet metal.
Efficiency: MIG welding produces stronger welds when great strength and durability are required, while spot welding is more effective and quicker in applications like the assembly of automobile body panels.