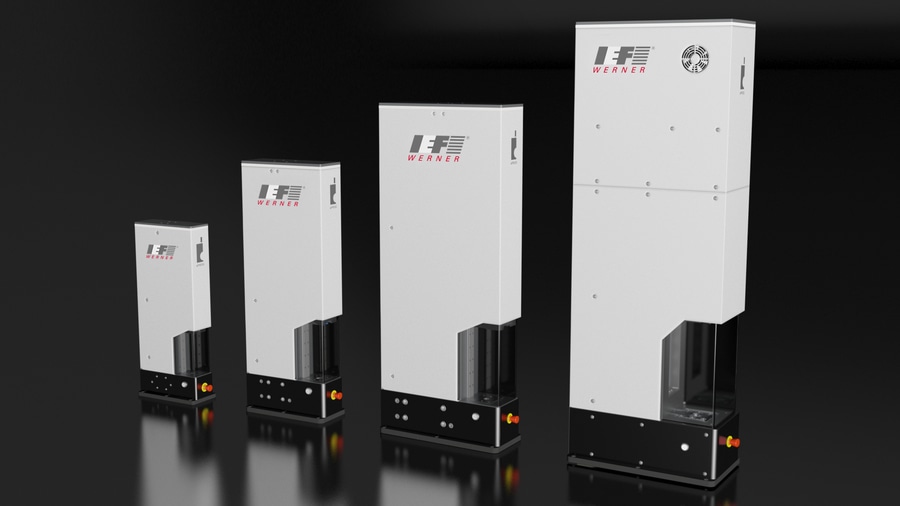
#Product Trends
A clear added value
IEF-Werner optimises aiPRESS servo press series
The aiPRESS servo press series from IEF-Werner is used by users to automatically press components with an accuracy of a few micrometres. The automation specialist has now further optimised the series, equipped it with special functions and subjected it to a type examination.
Furtwangen, 02.08.2023
"If components have to be joined with a high degree of precision, servo presses are used," Peter Pfaff explains, Head of Product Management Servo Presses at IEF-Werner GmbH. "These can also check the accuracy and divide the joined assemblies into good and bad parts or even into different quality levels." The automation specialist has developed the proven aiPRESS series for these tasks. The flexibly designed systems can be integrated into automated production lines as well as manual workstations. For this purpose, the presses have several standardised software interfaces and also simple I/O interfaces. The servo press is available in four sizes - the smallest has a force of three kilonewtons with an opening of 180 millimetres, the largest can achieve up to 100 kilonewtons with an opening of 350 millimetres. If required, IEF-Werner offers even more flexibility in the size of the working area with the aiPRESS JM series.
"In the summer of 2022, we had our servo press subjected to a type examination by TÜV Süd," Peter Pfaff says. In this way, IEF-Werner guarantees that the series meets all safety requirements from the standards applicable to the product and is suitable for the intended area of application. Operators receive production equipment that is tailored to their requirements and safe to operate. The type certificates issued are valid for all sizes.
More convenient to use
More convenient to use
In order to meet the increased customer requirements and to simplify the work for the user, the IEF developers have, among other things, optimised the multi-touch support of the control panel of the aiPRESS. "The user was already able to handle this intuitively before. Now it comes very close to the operation of a smartphone," Pfaff explains. In addition, the user management has been made clearer and the auto-scaling of the window has been adapted to the monitor size. Alternatively, the user can now also operate the press with standard monitors and input devices.
"We have also introduced a superuser for service - that is, a special user account with more authorisations than a normal account," Pfaff reports. If the user, for example the service technician, is logged in at this highest level, a window opens for him with special functions that are less interesting for the machine operator.
Zero point adjustable
Zero point adjustable
"The biggest innovation, however, concerns the adjustment of the zero point on the aiPRESS," IEF expert Pfaff explains. It's like this: The servo press consists of various components that are manufactured within certain tolerances. Depending on the size of the machine, these deviations can add up to seven to eight tenths. This then also affects the opening. "A few tenths often decide whether a joined assembly meets the requirements or is scrap," Peter Pfaff knows. If a user has several machines of the same size in operation, he cannot simply change the tool between the machines without having to make adjustments beforehand. "We now manufacture the opening for all sizes with an accuracy of five hundredths," Pfaff describes. This means that all presses are identical in construction and can be exchanged one-to-one. If the customer requires even tighter tolerances, IEF-Werner implements this according to customer specifications.
The product data is on the server. The operator can use the tool on the press that is currently free and simply start it - without having to make any adjustments. The parameters are identical on every machine. "We set the zero point in the factory, but it can also be changed at any time," Pfaff explains.
Pressing with measuring piece
Pressing with measuring piece
"We now also offer various special functions that we have developed customer-specifically," Peter Pfaff says: "Some of these will also be included in the standard." One function is called: 'Pressing with measuring piece'. Let's assume that there must be a gap of 0.3 millimetres between the motor and the fan wheel in an assembly. The motor is to be pressed onto the motor shaft. The assembly also consists of other components such as the fan wheel and ball bearing. All components have tolerances that add up. In order to produce the exact gap reproducibly, the operator first places the motor in the press and then a measuring piece. Now the other components of the assembly to be joined are added.
Peter Pfaff: "The aiPRESS presses the measuring piece with a defined force. The measured value, i.e. the thickness of the measuring piece, is stored as a parameter in the control." After this pre-pressing, the operator opens the press and removes the measuring piece. Now the press corrects the measurement until a gap of 0.3 millimetres is reached. With this pre-pressing on the measuring piece and post-pressing to the target dimension, all component tolerances can be compensated.
Pressing with digital input
Pressing with digital input
"To press an assembly, the user defines a force or a travel position," Peter Pfaff describes. To compensate for the summed tolerances of the individual components, he usually uses a gauge that serves as a reference standard for the previously defined dimension. Now there is another way: the IEF developers have made it possible to connect a sensor to the upper tool via a sensor connection. Now the press can be parameterised in such a way that it moves exactly until this sensor is actuated. To make it easier to set the sensor, there is a parameter that allows the sensor to be "overrun" in the tenth of a millimetre range.
"We have developed another special function," Pfaff reports. With 'spring element endurance test', a spring can be repeatedly loaded for displacement or force with the help of the aiPRESS and all values recorded via a displacement-force curve. Limit values for when the test should be stopped can be set. Peter Pfaff: "With our aiPRESS, the user can test how springs behave after five, 50, 500 or even 5,000 cycles, for example."
Precise operation
Precise operation
The basis of the servo press series consists of a solid and torsion-resistant C-frame. This bends up under very high forces. However, the bending is compensated. The drive train, which consists of a high-precision spindle, a servo motor and a quill guide, also ensures precise operation. This allows lateral forces to be absorbed safely. A precision guide keeps the drive train of the aiPRESS exactly on track over the entire working path. A configuration system ensures that it can be adapted to the required force range. The servo drive thus always works under optimal operating conditions. The operator can set process factors such as feed force, travel speed, positioning time and accuracy individually for the respective application.
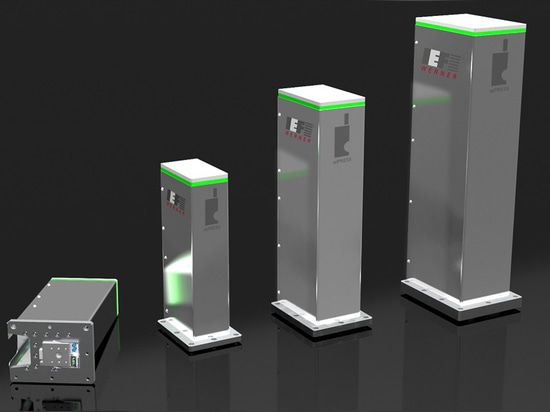
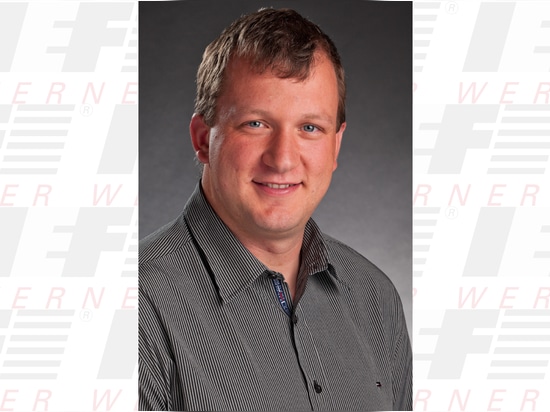