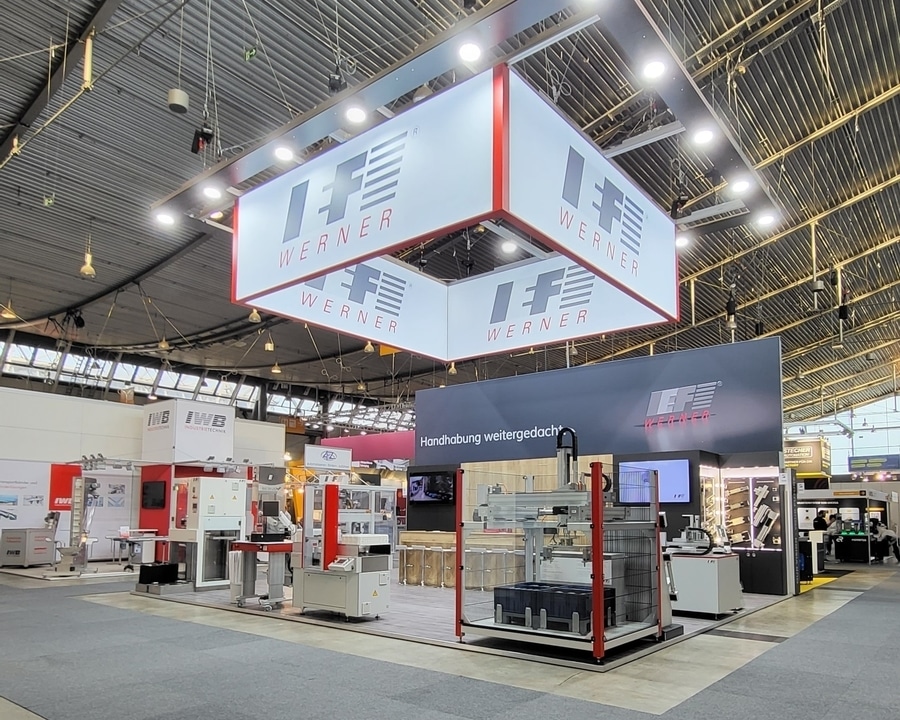
#Trade Shows & Events
Intelligent solutions
IEF-Werner at the Motek 2024
How can automation and handling tasks for production and assembly be solved intelligently? IEF-Werner will show this at the Motek in Stuttgart (8th to 11th October) in hall 5, booth 5220, where the automation specialist presents new developments as well as proven and very successful systems such as the aiPRESS servo press series.
Furtwangen, 22.08.2024
The flexibly designed aiPRESS servo press series is available in four sizes and can be integrated into both automated production lines and manual workstations. Workpieces can be joined or pressed with a high precision of just a few micrometres. Continuous quality control is already integrated into the aiPRESS by means of force-displacement monitoring. Assemblies can therefore not only be categorised into good and bad parts, but also into different quality levels. The presses have several standardised software and I/O interfaces for connection to the customer's system landscape. They can be further customised using various special functions. The basic system was successfully subjected to a type examination.
In Stuttgart, IEF-Werner will also be showing a gantry system with the toothed belt axis module 115/25, which can be used to safely handle workpieces or boxes weighing up to 40 kilograms. Thanks to the bending and torsion-resistant base bodies of the modules, large spans with strokes of up to 6.5 metres can be implemented. Even with high loads and long strokes, no additional support structures are required. Companies can not only reduce their costs with this system - compared to alternative solutions, they also benefit from a significantly faster system assembly.
Another exhibit will be the varioSTACK CF "Clean Factory". The open and modular palletising system is suitable for high-precision and automated production processes in cleanrooms - up to class 8 according to ISO 14644-1. The palletiser is used successfully in the medical technology, pharmaceutical and electrical industries, for example. The system can be operated with integrated IEF product handling, and the extremely compact palletiser can be loaded with trays weighing up to 15 kilograms as standard using pallet trolleys or conveyor belts.
With the energy-efficient and equally compact ecoSTACK palletising system, companies can reduce costs and strengthen their competitiveness. This is because the system works completely without expensive compressed air. The palletiser saves even more energy by automatically switching off components that are not currently required. The power supply is interrupted as often as possible - for example when the machine is at a standstill, at the end of a shift or during breaks. This also has a positive effect on the service life of the entire system. The ecoSTACK is designed as an inline system and enables the continuous loading and unloading of pallets of different sizes - especially quarter and octal pallets.
In order to monitor production processes and the quality of components, IEF-Werner has further developed its previous camera solutions. The new, wireless image transmission to mobile devices is an advantage here - especially for manual operations within the machine, out of sight of the permanently installed control panel. The camera - including lens and lighting - can be mounted on the domiLINE manual adjustment unit. A precise steel spindle, ball-bearing mounted in end plates and with a low-backlash, pre-tensioned plastic nut, moves the guide system. Precise positioning is achieved by using a rotary knob or handwheel - motorisation is also possible. The unit can be flexibly mounted in all positions, allowing the image sensor to be easily readjusted when the product is changed.
Trade visitors will be able to see the roboSTACK in action virtually on screens. The new palletising system is based on the modular and compact varioSTACK palletiser. Instead of standard linear handling as in the varioSTACK, the roboSTACK has been specially developed for the integration of a robot and the palletiser frame has been reinforced accordingly. The robot palletiser is also available in the roboSTACK Flex version. Here, the palletiser is equipped with variable infeed belts and electrically controllable lifting forks, for example. This allows it to flexibly process different tray sizes.
Predictive maintenance
Predictive maintenance makes it possible to identify problems or failures before they become acute - this can significantly reduce cost-intensive downtime or damage. With the development from IEF-Werner, process and machine data for wear detection can be analysed and evaluated. The value-added information obtained in this way can be processed in an application-specific and user-orientated manner and supports all parties involved in the respective decision-making process, from the machine operator to the service technician to the management level. This will be impressively demonstrated at the stand via the live monitoring of two trade fair exhibits.
Another exhibit shows a robot mounted on a linear unit - keyword: "Robot with 7th axes". This seventh axis can significantly increase the efficiency of the robot in assembly and also in material handling. This is because it can move from one production station to another with a much greater range, which can be extended if necessary.
IEF-Werner at the Motek: Hall 5, Stand 5220

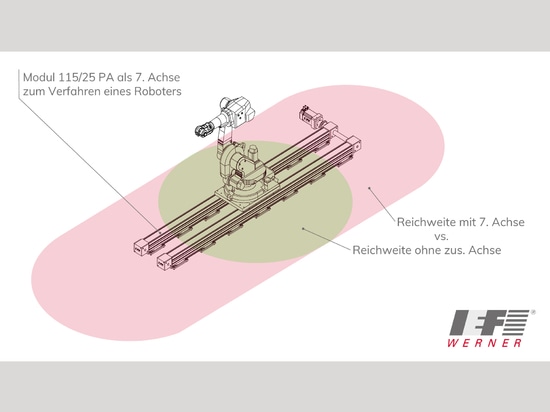
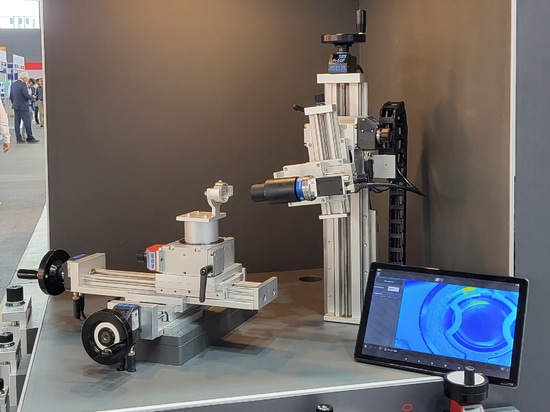
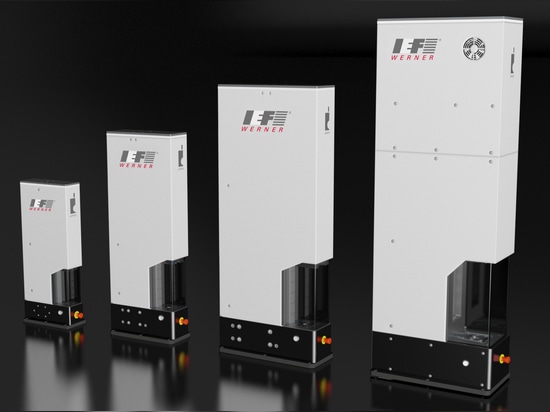