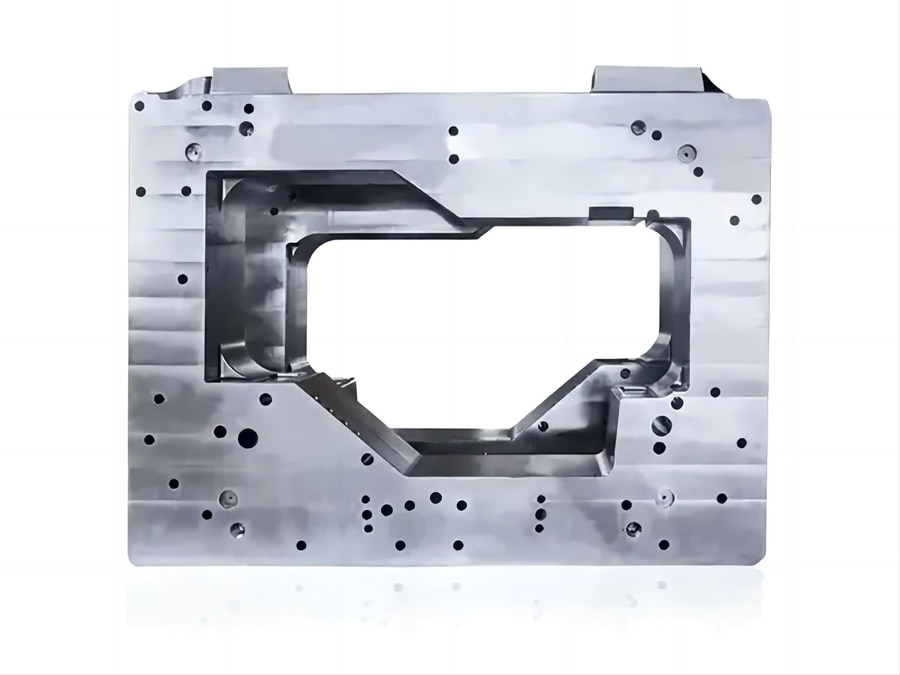
#Industry News
The Mould Base Is An Important Part Of The Design And Manufacturing Of New Energy Vehicles
The Mould Base Is An Important Part Of The Design And Manufacturing Of New Energy Vehicles
Fuel Cars Mould Base
The Fuel Cars mould base is an important part of the design and manufacturing of new energy vehicles. It is used for assembling various parts of the car and is essential for ensuring that each part has the correct shape, is standard compliant and meets the mechanical properties required before production.
Moulds are used to manufacture a wide range of products from small parts to entire vehicle body panels. They are made from metal, usually either steel or aluminum, and precision-machined to form the features of the desired part.
Injection Moulding
Plastic resin is injected into the mould, shaped, and then removed in an ejection system. In an injection mould, a sprue or gate seals tightly against the nozzle of the injection barrel, allowing the molten plastic to flow from the nozzle into the cavity images in the mold. The runner and sprue systems are machined into the face of the A and B plates of the mould, which allow the molten plastic to run along them during ejection.
Generally, the material of the mould can be aluminum or stainless steel; some types of tool steels are also used, such as hardened steel and Beryllium copper. These metals have good corrosion resistance and wear resistance, which is especially useful for the areas of the mould that see high levels of shear heat generated during machining.
Chromium plating is one of the most common surface treatment methods, which can passivate the surface of the metal, maintain its metallic luster for long periods of time, and prevent chemical reactions in acidic environments. The chromium layer has a very high hardness and can also resist high temperatures.
SMC (Silicon Molded Compound)
The SMC compound is an excellent insulation material, providing high-performance insulation resistance to prevent leakage, maintaining good dielectric properties at high frequencies, does not reflect, and has anti-creepage indicators that meet DIN / VDE-related standards. It has a low thermal conductivity, making it suitable for use in applications that require a high level of temperature stability, such as a battery box or engine cover.
SMC molds have been widely used in the automotive industry due to their excellent physical properties, such as strength and dimensional stability, which make them ideal for molding of bumpers, battery boxes, engine covers, structural beams, etc. They are also highly resistant to oxidation and can be heat treated after machining, resulting in a much longer life than other materials.
Injection Moulds for Fuel Cars
Several moulding techniques are available for new energy vehicle manufacturers to produce a wide range of plastic parts for their cars, including injection molding, CNC machining, and electro-plating. Each method has its own strengths and weaknesses, which can affect the quality and efficiency of the final product.
Injection of molded plastic parts can be a great way to reduce the weight of a new energy vehicle, which can help improve its fuel economy and increase driving distances. They can also be a cost-effective way to integrate many metal parts into a single unit, reducing the number of steps in the integration process and lowering production costs.