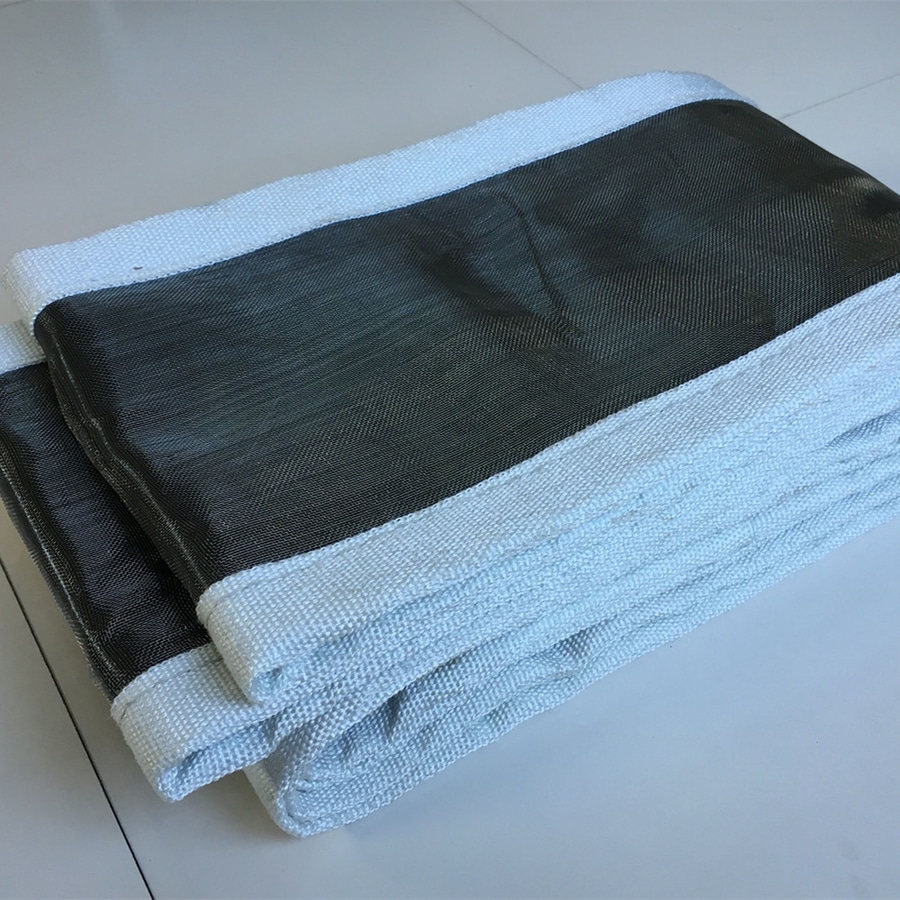
#Product Trends
Thermal insulation Fabric expansion joints
Fabric expansion joints
Fabric expansion joints are essential components in systems that carry hot gases and low-pressure fluids, offering flexibility and compensation for thermal expansion and contraction in ducts, pipes, and other exhaust systems. They are designed to handle high temperatures, varying flow rates, and challenging operating conditions, making them a popular choice for industries such as power generation, petrochemical, cement manufacturing, and HVAC systems. These joints effectively absorb vibrations, reduce noise, and accommodate thermal growth, ensuring the integrity of the system while maintaining smooth flow and minimal maintenance needs.
Fabric expansion joints are typically employed in applications where the medium being transported is a gas, air, or smoke at low pressures. The fabric’s composition is chosen based on the specific needs of the application, such as the temperature of the gases, the flow rate, the amount of solids suspended in the gases, and the chemical properties of the medium. The fabrics used in these joints are selected for their high heat resistance, durability, and ability to withstand the mechanical stresses induced by the temperature fluctuations and gas flow.
In some applications, multiple layers of different fabric materials are combined to enhance insulation properties and withstand the specific temperature and pressure requirements of the system. For instance, a combination of fiberglass, silicone, and other heat-resistant materials might be used for an industrial exhaust system where extreme temperatures and corrosive gases are present. The multi-layer construction offers enhanced protection, reducing the likelihood of wear and tear and extending the life of the fabric expansion joints.
Due to the demanding conditions in which fabric expansion joints operate, regular inspection and maintenance are required. Over time, these joints can degrade due to high temperatures, abrasive gases, or chemical exposure. In such cases, they may need to be replaced to maintain system efficiency and prevent potential failures. While fabric expansion joints are designed for durability, periodic replacement helps ensure optimal performance, preventing damage to the system and avoiding costly repairs.
A notable application of fabric expansion joints can be found in power plants, where they are used in the ducts of flue gas systems to absorb thermal expansion caused by varying combustion temperatures. In cement plants, these joints are used to accommodate the high temperatures and abrasive particles found in the exhaust gases, helping to reduce wear on the ducting system. Similarly, in the petrochemical industry, fabric expansion joints are used to manage the fluctuating temperatures and flow rates in pipes that transport gases and chemical vapors.
In conclusion, fabric expansion joints are crucial for ensuring the longevity and smooth operation of systems that handle high temperatures and low-pressure gases. Their ability to adapt to varying conditions, absorb vibrations, and accommodate thermal expansion makes them indispensable in numerous industrial applications. With proper maintenance and timely replacement, fabric expansion joints can continue to deliver reliable performance while minimizing downtime and operational disruptions.