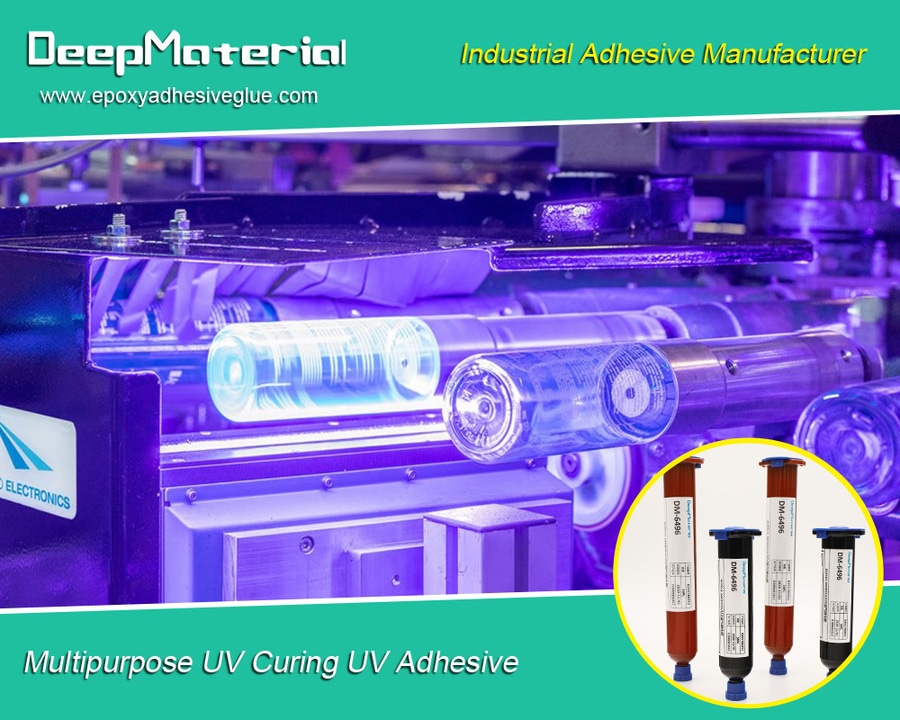
#Industry News
A Comprehensive Guide to UV Cure Silicone Adhesives
Best UV Cure Silicone Adhesive Glue Manufacturer
A Comprehensive Guide to UV Cure Silicone Adhesives
The importance of UV cure silicone adhesives lies in their ability to provide strong and durable bonding while being easy to handle and use. They are also resistant to heat, moisture, and chemicals. Such makes them ideal for use in harsh environments. Again, they are used in various industries and have unique properties that make them stand out from other types of adhesives.
The purpose of this guide is to provide a thorough understanding of UV cure silicone adhesives, including their properties, applications, types, preparation, testing, safety considerations, and environmental impact. By the end of this guide, you will have a comprehensive knowledge of such adhesives and be able to make informed decisions about their use.
Properties of UV cure silicone adhesives
UV cure silicone adhesives have a unique chemical structure that sets them apart from other types of adhesives. They are made up of a silicone polymer backbone with organic and inorganic groups attached to it. This structure gives UV cure silicone adhesives their unique properties and advantages.
Chemical structure of UV cure silicone adhesives
One of the most significant advantages of UV cure silicone adhesives is their ability to cure quickly and efficiently using UV light. This allows for fast and easy bonding, reducing production time and costs. Also, UV cure silicone adhesives have a high degree of flexibility, making them ideal for bonding materials that undergo frequent expansion and contraction.
Unique properties and advantages of UV cure silicone adhesives
UV cure silicone adhesives also have excellent thermal stability and are resistant to a wide range of chemicals. These include solvents, acids, and bases. This makes them great for use in harsh environments where other types of adhesives may fail.
Comparison with other types of adhesives
In comparison to other types of adhesives, such as epoxy and cyanoacrylate, UV cure silicone adhesives offer several advantages. For example, they have a longer shelf life and can be stored for longer periods without losing their properties. They also have a lower viscosity, allowing for easier dispensing and application.
Applications of UV cure silicone adhesives
UV cure silicone adhesives find use in a wide range of industries and products. Some of the industries that commonly use UV cure silicone adhesives include electronics, medical devices, automotive, aerospace, and construction.
In the electronics industry, UV cure silicone adhesives are useful for bonding components and protecting them from moisture, vibration, and temperature fluctuations. They are also used to encapsulate and seal components, such as circuit boards and sensors.
Again, UV cure silicone adhesives are used for bonding and sealing medical devices, such as catheters, pacemakers, and implantable devices. They are biocompatible and can withstand sterilization, making them ideal for use in medical applications.
In the automotive industry, UV cure silicone adhesives are used for bonding and sealing components, such as lights, mirrors, and trim. They offer excellent adhesion to various substrates, including plastics, metals, and composites. These are known to withstand exposure to heat, chemicals, and weathering.
In the aerospace industry, UV cure silicone adhesives are used for bonding and sealing components like composites, metal, and glass. They offer excellent adhesion and flexibility, making them perfect for use in aircraft and space applications.
UV cure silicone adhesives are used in the construction industry for bonding and sealing materials, such as glass, metal, and concrete. They are weather-resistant and offer excellent adhesion and flexibility. Due to this, they can be used in construction applications.
The advantages of using UV cure silicone adhesives in these industries include fast cure times, high strength and durability, excellent thermal stability, and resistance to moisture, chemicals, and weathering. They offer excellent adhesion to a wide range of substrates. Such makes them a versatile choice for various bonding applications.
Types of UV cure silicone adhesives
UV cure silicone adhesives can be classified based on their functionality and application. Some of the common types of UV cure silicone adhesives include:
Structural UV cure silicone adhesives
These are high-strength adhesives that are used for bonding and sealing structural components. They offer excellent adhesion to various substrates and have high elongation and flexibility.
Electronic UV cure silicone adhesives
These adhesives are designed for use in the electronics industry, where they are used to bond and seal components. They offer excellent moisture resistance and thermal stability.
Medical UV cure silicone adhesives
These adhesives are biocompatible and are used for bonding and sealing medical devices. They can withstand sterilization and offer excellent adhesion to various substrates.
Optical UV cure silicone adhesives
These adhesives are used for bonding and sealing optical components such as lenses and prisms. They offer excellent clarity and light transmission.
When choosing the right type of UV cure silicone adhesive, several criteria should be considered. These are the type of substrate to be bonded, the environmental conditions, and required properties of the bond. Some of the properties to consider include adhesion strength, flexibility, thermal stability, chemical resistance, and moisture resistance.
Preparation and application of UV cure silicone adhesives
The preparation process requires attention to several critical factors to ensure proper bonding and curing.
Surface preparation and cleaning are crucial steps before applying UV cure silicone adhesives. The surfaces to be bonded should be clean, dry, and free of any contaminants such as oils, dust, and rust. Cleaning can be done using solvents or detergents. Also, the surfaces should be rinsed thoroughly with water and allowed to dry completely.
UV cure silicone adhesives should be mixed and dispensed according to the manufacturer instructions. Mixing and dispensing techniques may vary depending on the viscosity of the adhesive, application method, and equipment used. It is essential to ensure that the adhesive is thoroughly mixed and applied uniformly to avoid uneven curing or bonding.
Several factors can affect the curing process of UV cure silicone adhesives, including the intensity and wavelength of the UV light, the distance between the UV source and the adhesive, the thickness of the adhesive layer, and the presence of air or oxygen. It is essential to follow the manufacturer instructions regarding curing conditions and to ensure that the adhesive is fully cured before subjecting it to any stress or strain.
Conclusion
UV cure silicone adhesives offer unique properties and advantages over other types of adhesives, making them an attractive choice for various applications in industries such as electronics, medical devices, automotive, aerospace, and construction. The classification of UV cure silicone adhesives based on functionality and application provides users with a range of options to choose from, depending on their specific bonding needs.
For more about choosing a comprehensive guide to UV cure silicone adhesives, you can pay a visit to DeepMaterial at https://www.epoxyadhesiveglue.com/uv-curing-uv-adhesive/ for more info.