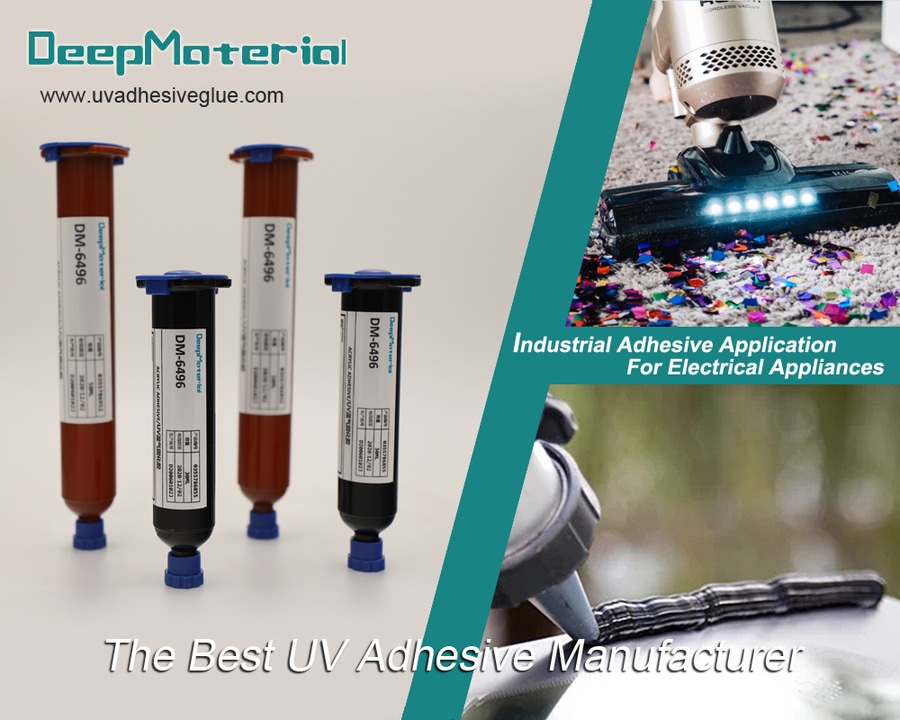
#Industry News
Are There Any UV Cure Adhesive For Metals?
best uv curing glue manufacturer
Of course, there are UV-curing glues that are designed for bonding metal surfaces. UV-curing glues, also known as UV glues or UV curable glues, are formulated to cure rapidly when exposed to ultraviolet (UV) light. These glues are often used in applications where fast curing times, high bond strength, and excellent adhesion are required. They are commonly used in industries such as electronics, medical devices, automotive, and more.
UV cure adhesive for metal typically come in different formulations to cater to various types of metal substrates and specific bonding requirements. Some common types of UV-curing glues for metal include:
UV Acrylate adhesives: These glues are often used for bonding metal surfaces. They provide good adhesion to a variety of metals, including stainless steel, aluminum, and more. They cure quickly when exposed to UV light and can offer high bond strength. UV acrylate adhesives offer several advantages over traditional glues:
Rapid Curing: UV acrylate adhesives cure quickly when exposed to UV light. This rapid curing process helps improve production efficiency and reduces the time required for bonding.
No Solvents or Volatile Organic Compounds (VOCs): UV acrylate adhesives are often solvent-free or low in VOCs, making them more environmentally friendly and safer for workers.
Strong Bonds: Once cured, UV acrylate adhesives can form strong and durable bonds on various substrates, including plastics, metals, glass, ceramics, and more.
Precision Application: UV glues can be applied precisely to specific areas, which is particularly useful for intricate assemblies and delicate components.
Minimal Heat Generation: The curing process of UV acrylate adhesives generates minimal heat, reducing the risk of damaging sensitive components.
Low Shrinkage: These glues tend to have low levels of shrinkage upon curing, which is important for maintaining dimensional stability in bonded parts.
Clear and Transparent Bonds: UV acrylate adhesives can cure to form clear and transparent bonds, making them suitable for applications where aesthetics are important.
UV Epoxy adhesives: UV-curable epoxy adhesives are used when a combination of high bond strength and resistance to harsh environments is required. They can bond metals as well as other materials effectively.Here are some key points about UV epoxy adhesives:
Dual Cure Mechanism: UV epoxy adhesives typically have a dual cure mechanism. They can cure through both UV light exposure and heat. This flexibility allows for curing in situations where direct UV light exposure might be limited.
Rapid Curing: Like other UV-curable adhesives, UV epoxy adhesives cure rapidly upon exposure to UV light. This characteristic is beneficial for applications where fast production cycles and reduced curing times are important.
Strong Bonds: UV epoxy adhesives can provide high bond strength on a variety of substrates, including metals, plastics, glass, ceramics, and more. The combination of epoxy’s inherent bonding properties with UV curing results in reliable and durable glue joints.
Low VOC Emissions: UV epoxy adhesives often have lower volatile organic compound (VOC) emissions compared to traditional solvent-based glues, contributing to a safer and more environmentally friendly bonding process.
Temperature Resistance: Epoxy glues, including UV epoxy formulations, are known for their thermal stability and resistance to elevated temperatures. This makes them suitable for applications that involve exposure to heat.
Versatility: UV epoxy adhesives can be used in a wide range of industries and applications, including electronics assembly, optics, medical devices, automotive components, aerospace, and more.
Clear and Transparent Bonds: Some UV epoxy adhesives are formulated to cure to a clear and transparent finish, making them suitable for applications that require optical clarity or an aesthetically pleasing appearance.
Precision Application: UV epoxy adhesives allow for precise application due to their liquid nature before curing. This precision is useful for intricate assemblies and bonding of delicate components.
UV Cyanoacrylate adhesives: UV-curing Cyanoacrylate adhesives are known for their fast curing times and excellent adhesion to metals. They are used in applications where rapid assembly or repair is essential.
Fast Bonding: Cyanoacrylate adhesives are known for their rapid bonding properties. They can create strong bonds in a matter of seconds upon contact with the substrate surfaces. This property allows for quick assembly and production processes.
UV Curing: UV Cyanoacrylate adhesives cure through a combination of the initial cyanoacrylate bonding reaction and subsequent UV light exposure. The UV light initiates further curing, enhancing the glue’s strength and durability.
Strong Bonds: These glues provide strong and reliable bonds on various substrates, including plastics, metals, rubbers, and more. The combination of cyanoacrylate’s inherent bonding properties with UV curing results in robust glue joints.
Versatility: UV Cyanoacrylate adhesives find applications in industries such as electronics, medical devices, automotive, and manufacturing. They can be used for bonding small components, sealing joints, and securing delicate parts.
Curing Control: UV curing offers control over the curing process. The glue doesn’t fully cure until exposed to UV light, allowing for precise alignment of parts before permanent bonding occurs.
Low Heat Generation: UV curing generates minimal heat, making these glues suitable for bonding heat-sensitive materials and components.
Instant Fixturing: The initial cyanoacrylate bonding reaction provides instant fixturing, while the subsequent UV curing enhances bond strength over time.
Reduced Blooming: Blooming, a phenomenon where white residues form around the bonded area due to cyanoacrylate fumes, can be reduced in UV-curable formulations.
UV Silicone adhesives: UV-curable Silicone adhesives are used when flexibility and high-temperature resistance are important. They can bond metals that might experience thermal expansion and contraction, resulting in durable and flexible bonds.
Flexibility and Durability: Silicone adhesives are known for their flexibility and excellent durability. UV Silicone adhesives retain these properties while also offering rapid curing through UV light exposure.
Rapid Curing: UV Silicone adhesives cure quickly upon exposure to UV light. This rapid curing process is advantageous for applications that require fast production cycles and reduced assembly times.
Strong Bonds: These glues provide strong adhesion to a wide range of substrates, including metals, plastics, glass, ceramics, and more. The combination of silicone’s inherent bonding capabilities with UV curing results in reliable glue joints.
Flexibility and Thermal Resistance: UV Silicone adhesives maintain their flexibility even after curing, making them suitable for applications that involve movement or thermal expansion. They can withstand a range of temperatures and environmental conditions.
Water and Chemical Resistance: Silicone adhesives, including UV-curable formulations, are known for their resistance to water, chemicals, and other environmental factors. This resistance makes them suitable for outdoor and harsh environment applications.
Electrical Insulation: UV Silicone adhesives often exhibit excellent electrical insulation properties, making them suitable for applications involving electronic components and insulating materials.
Versatility: UV Silicone adhesives find applications in industries such as electronics, automotive, medical devices, aerospace, and more. They can be used for bonding, sealing, gasketing, and encapsulation.
Curing Control: Similar to other UV-curable glues, UV Silicone adhesives offer control over the curing process. This enables precise positioning of parts before permanent bonding occurs.
UV Anaerobic adhesives: These glues cure in the presence of metal and the absence of oxygen. They are often used for threadlocking, thread sealing, and gasketing applications in metal assemblies.
Conclusion
When using UV cure adhesive for metal, it’s important to consider factors such as the type of metal being bonded, surface preparation, the specific glue formulation, the curing equipment (UV light source), and the intended application requirements. Additionally, proper surface cleaning and preparation are essential to ensure strong and durable bonds.
Always follow the manufacturer’s guidelines and recommendations for proper usage, application, and curing of UV cure adhesive for metal.