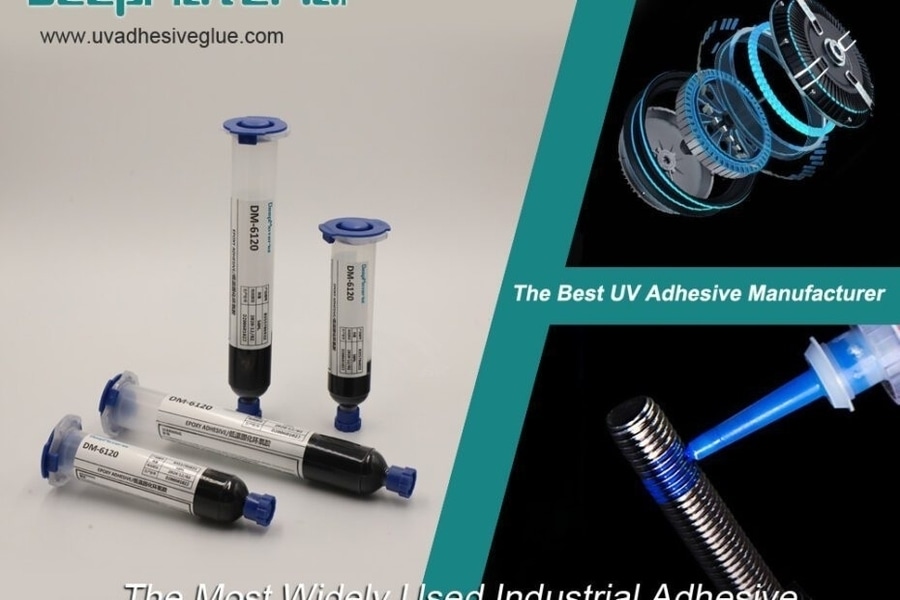
#Industry News
Innovative Techniques for UV Bonding Glass to Metal: Breaking New Grounds
Best UV Adhesive Glue Bonding Glass to Metal Manufacturer
Innovative Techniques for UV Bonding Glass to Metal: Breaking New Grounds
In the ever-evolving world of material science and engineering, the quest for innovative techniques to bond different materials together is a constant pursuit. One such area that has seen significant advancements in recent years is the bonding of glass to metal using Ultraviolet (UV) light. This process, known as UV bonding, has opened up a plethora of possibilities in various industries, from automotive and aerospace to electronics and home appliances.
This blog post aims to delve into the intricacies of this groundbreaking technique, exploring its benefits, applications, and the latest advancements that are pushing the boundaries of what’s possible.
The Importance of Innovative Techniques in UV Bonding
Innovative techniques in UV bonding offer several advantages over traditional methods. One of the main benefits is the ability to achieve a stronger bond between glass and metal surfaces. This is crucial in applications where the bond needs to withstand high levels of stress or pressure. Innovative techniques also allow for greater precision and control during the bonding process, resulting in improved quality and reliability.
Furthermore, innovative techniques in UV bonding can help to reduce production time and costs. By using advanced equipment and materials, manufacturers can streamline the bonding process and increase efficiency. This not only saves time but also reduces the need for manual labor, leading to cost savings. Additionally, innovative techniques can result in a more aesthetically pleasing final product, as they allow for seamless bonding without the need for visible fasteners or adhesives.
Traditional Techniques vs. Innovative Techniques in UV Bonding
When comparing traditional techniques to innovative techniques in UV bonding, there are several key differences. Traditional techniques often involve the use of mechanical fasteners or chemical adhesives that require curing at elevated temperatures. These methods can be time-consuming and may result in a less aesthetically pleasing final product.
On the other hand, innovative techniques in UV bonding utilize UV-cured adhesives that offer several advantages. UV-cured adhesives cure quickly when exposed to UV light, allowing for faster production times. This is particularly beneficial in high-volume manufacturing environments where efficiency is crucial. Additionally, UV-cured adhesives do not require elevated temperatures for curing, reducing the risk of damage to sensitive components or materials.
Furthermore, innovative techniques in UV bonding allow for greater precision and control during the bonding process. Advanced equipment and materials enable manufacturers to achieve a more accurate and consistent bond between glass and metal surfaces. This results in improved quality and reliability of the final product.
Breaking New Grounds in UV Bonding Glass to Metal
In recent years, new techniques have emerged that are revolutionizing the UV bonding industry. One such technique is the use of nanotechnology in UV bonding. Nanotechnology involves manipulating materials at the nanoscale level to enhance their properties. By incorporating nanoparticles into UV-cured adhesives, manufacturers can achieve even stronger bonds between glass and metal surfaces.
Another innovative technique is the use of 3D printing in UV bonding. 3D printing allows for the creation of complex shapes and structures, making it ideal for applications where customization is required. By combining 3D printing with UV bonding, manufacturers can create intricate designs that were previously not possible.
Furthermore, advancements in UV light sources have also contributed to the development of new techniques in UV bonding. High-intensity UV lamps and LED technology have made it possible to cure adhesives more quickly and efficiently. This has resulted in faster production times and improved productivity.
The Role of Technology in UV Bonding
Technology plays a crucial role in advancing UV bonding techniques. One example is the use of robotic systems for precise and automated application of UV-cured adhesives. Robotic systems can be programmed to apply the adhesive with high accuracy, ensuring consistent and reliable bonds. This eliminates the need for manual labor and reduces the risk of human error.
Another technological advancement in UV bonding is the development of advanced adhesive formulations. Manufacturers are constantly researching and developing new adhesive formulations that offer improved adhesion properties, faster curing times, and increased durability. These advancements allow for stronger and more reliable bonds between glass and metal surfaces.
Case Studies: Successful Applications of Innovative UV Bonding Techniques
There have been numerous successful applications of innovative UV bonding techniques in various industries. One example is the automotive industry, where UV bonding is used to bond glass windows to metal frames. The use of UV-cured adhesives allows for a strong and durable bond that can withstand the harsh conditions of the road. Additionally, the seamless and invisible bond achieved through UV bonding enhances the aesthetic appeal of the vehicle.
Another example is the electronics industry, where UV bonding is used to assemble electronic devices. The precise and controlled application of UV-cured adhesives ensures reliable and consistent bonds between glass and metal components. This is crucial in electronic devices where the bond needs to withstand vibrations, temperature changes, and other environmental factors.
Furthermore, the medical device industry has also benefited from innovative UV bonding techniques. UV bonding is used to assemble medical devices such as syringes, catheters, and surgical instruments. The strong and durable bond achieved through UV bonding ensures the safety and reliability of these devices, which are critical in medical applications.
Future of UV Bonding Glass to Metal: Trends and Developments
The future of UV bonding glass to metal looks very promising as some trends are likely to become popular. One trend is the use of bio-based adhesives in UV bonding. Bio-based adhesives are made from renewable resources and offer several environmental benefits. They are also biodegradable, making them a sustainable choice for manufacturers.
Another trend is the development of self-healing adhesives in UV bonding. Self-healing adhesives have the ability to repair themselves when damaged, resulting in a longer-lasting bond. This is particularly beneficial in applications where the bond is subjected to wear and tear or frequent stress.
Furthermore, advancements in nanotechnology are expected to continue shaping the future of UV bonding. Nanoparticles can be incorporated into UV-cured adhesives to enhance their properties, such as strength, flexibility, and conductivity. This opens up new possibilities for applications in various industries.
Last Words
In conclusion, the use of innovative techniques in UV bonding glass to metal offers numerous benefits and improvements to the bonding process. These techniques allow for stronger bonds, improved aesthetics, and cost savings. The advancements in technology and adhesive formulations have further enhanced the capabilities of UV bonding.
It is important for manufacturers to embrace innovation in UV bonding and stay updated with the latest trends and developments in the industry. By doing so, they can improve the quality and reliability of their products, increase efficiency, and stay ahead of the competition. Embracing innovation in UV bonding not only benefits the industry but also customers who rely on high-quality and durable products.
For more about choosing the UV bonding glass to metal, you can pay a visit to DeepMaterial at https://www.epoxyadhesiveglue.com/uv-curing-uv-adhesive/ for more info.