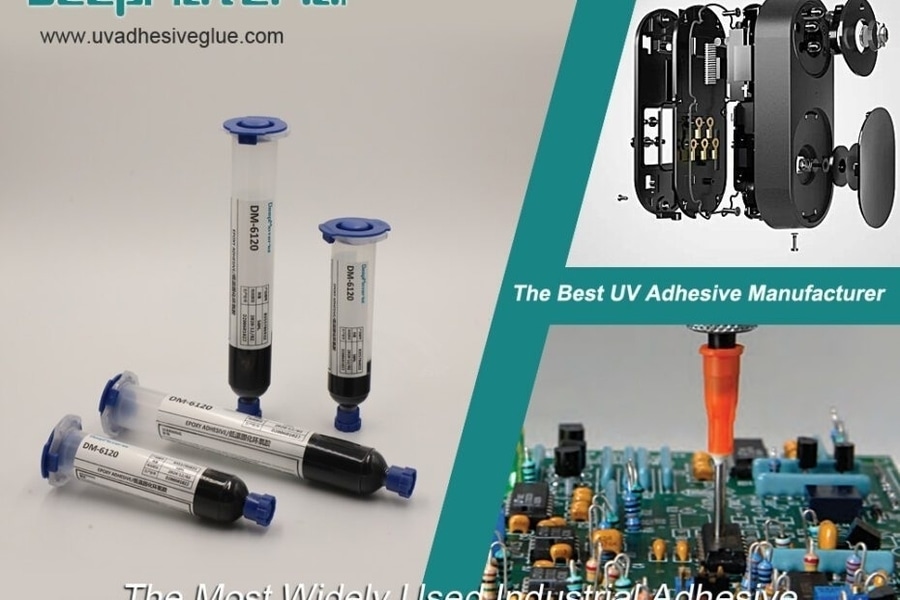
#Industry News
The Impact of UV Curable Optical Assembly Adhesives on Product Reliability and Performance
Best UV Curable Optical Assembly Adhesive Glue Manufacturer
UV curable optical assembly adhesives play a crucial role in ensuring the reliability and performance of various products across industries. These adhesives offer fast curing times, strong bonding strength, and improved optical clarity, making them ideal for applications in electronics, medical devices, and automotive industries.
In this article, we will explore the importance of UV curable optical assembly adhesives in product reliability and performance, their advantages over other types of adhesives, factors affecting their performance, testing and evaluation methods, successful case studies, challenges and limitations, and future trends and developments.
Importance of Product Reliability and Performance
Product reliability refers to the ability of a product to perform its intended function consistently over a specified period of time without failure or degradation. Product performance, on the other hand, refers to how well a product meets or exceeds its intended specifications and requirements.
Product reliability and performance are crucial factors in various industries. In the electronics industry, for example, reliable and high-performing products are essential to ensure the proper functioning of electronic devices. In the medical device industry, product reliability and performance are critical to patient safety and well-being. In the automotive industry, reliable and high-performing components are necessary for vehicle safety and longevity.
Adhesives play a significant role in ensuring product reliability and performance. They are used in the assembly of various products, providing structural integrity and bonding strength. The choice of adhesive can greatly impact the overall reliability and performance of a product.
The Role of Adhesives in Product Reliability and Performance
Adhesives have a direct impact on the reliability and performance of products. They provide structural support, distribute stress, and enhance the overall strength of the assembly. The choice of adhesive is crucial as it must be compatible with the substrates being bonded and provide sufficient bond strength to withstand the intended use and environmental conditions.
Different industries use different types of adhesives based on their specific requirements. For example, in the electronics industry, conductive adhesives are used to bond electrical components, while in the medical device industry, biocompatible adhesives are used to ensure compatibility with human tissues.
Using adhesives in product assembly offers several advantages. They provide uniform stress distribution, reducing the risk of mechanical failure. Adhesives also eliminate the need for mechanical fasteners, such as screws or rivets, which can weaken the substrate or create stress concentrations. Additionally, adhesives can bond dissimilar materials, allowing for the assembly of complex structures.
Advantages of UV Curable Optical Assembly Adhesives
UV curable optical assembly adhesives offer several advantages over other types of adhesives. One of the main advantages is their faster curing time. UV curable adhesives cure within seconds when exposed to UV light, allowing for faster production cycles and increased productivity.
Another advantage is their superior bonding strength. UV curable adhesives form strong bonds between substrates, providing excellent adhesion and durability. This is especially important in applications where high bond strength is required, such as in the assembly of electronic components or medical devices.
UV curable adhesives also offer improved optical clarity. They have low levels of haze and yellowing, making them ideal for applications where optical clarity is critical, such as in the assembly of display screens or optical lenses.
Furthermore, UV curable adhesives have a reduced environmental impact compared to other types of adhesives. They do not contain volatile organic compounds (VOCs) and do not emit harmful fumes during curing. This makes them safer for both workers and the environment.
Factors Affecting the Performance of UV Curable Optical Assembly Adhesives
Several factors can affect the performance of UV curable optical assembly adhesives. One of the key factors is substrate compatibility. UV curable adhesives may not bond well with certain substrates, such as low surface energy plastics or metals with high reflectivity. It is important to select an adhesive that is compatible with the specific substrates being bonded to ensure optimal performance.
Curing conditions also play a crucial role in the performance of UV curable adhesives. Factors such as UV light intensity, exposure time, and distance from the light source can affect the curing process. It is important to follow the manufacturer’s recommendations for curing conditions to ensure proper curing and optimal bond strength.
Exposure to UV light is another factor that can affect the performance of UV curable adhesives. Prolonged exposure to UV light can cause degradation of the adhesive, leading to reduced bond strength and durability. It is important to consider the intended use and environmental conditions of the product to ensure that the adhesive can withstand UV exposure over its expected lifespan.
Temperature and humidity can also impact the performance of UV curable adhesives. Extreme temperatures can cause the adhesive to become brittle or lose its bond strength. High humidity can affect the curing process and lead to reduced bond strength. It is important to consider the temperature and humidity conditions during the curing and application process to ensure optimal performance.
Testing and Evaluation of UV Curable Optical Assembly Adhesives
Testing and evaluation are crucial steps in the development and application of UV curable optical assembly adhesives. Various methods can be used to test the performance of adhesives, including lap shear testing, peel testing, and thermal cycling testing.
Lap shear testing is commonly used to measure the bond strength of adhesives. It involves bonding two substrates together and subjecting them to a tensile force until failure occurs. The force required to cause failure is measured and used as an indicator of bond strength.
Peel testing is used to measure the adhesion strength of adhesives. It involves bonding a flexible substrate to a rigid substrate and applying a tensile force to peel them apart. The force required to cause peeling is measured and used as an indicator of adhesion strength.
Thermal cycling testing is used to evaluate the durability of adhesives under temperature variations. It involves subjecting the bonded assembly to repeated cycles of temperature changes and measuring any changes in bond strength or integrity.
Testing and evaluation are important in ensuring that UV curable optical assembly adhesives meet the required specifications and performance standards. They help identify any potential issues or weaknesses in the adhesive and allow for adjustments or improvements to be made before the adhesive is used in production.
Conclusion
UV curable optical assembly adhesives play a crucial role in ensuring the reliability and performance of various products across industries. Their fast curing time, strong bonding strength, improved optical clarity, and reduced environmental impact make them ideal for applications in electronics, medical devices, and automotive industries. Factors such as substrate compatibility, curing conditions, exposure to UV light, and temperature and humidity can affect the performance of UV curable adhesives.
For more about choosing the UV Curable Optical Assembly Adhesives, you can pay a visit to DeepMaterial at https://www.epoxyadhesiveglue.com/uv-curing-uv-adhesive/ for more info.