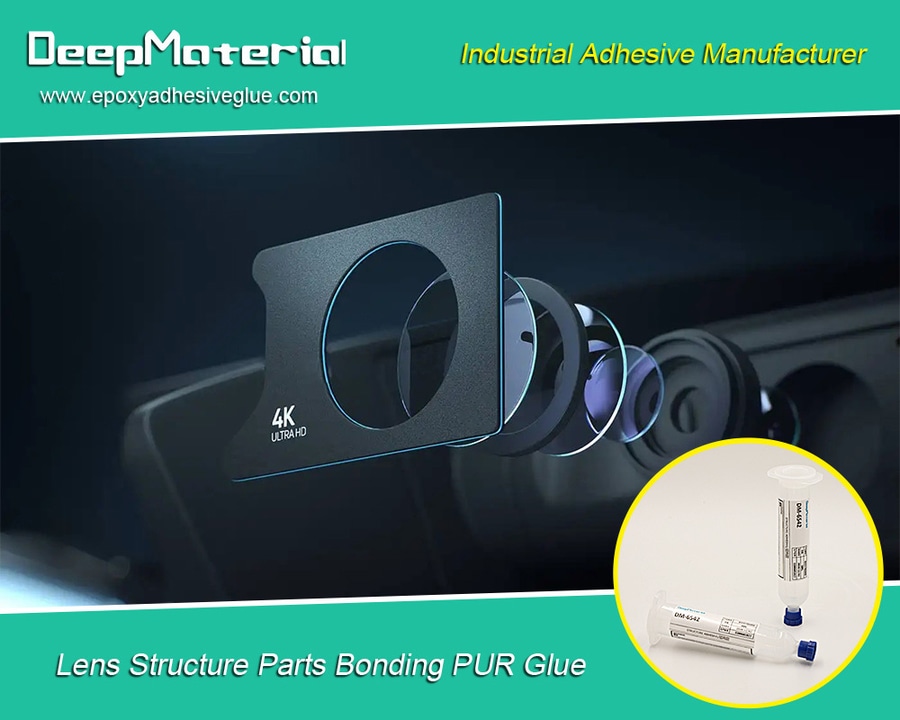
#Industry News
The Importance of Quality Control in Electronic Assembly Adhesive Selection
Best Electronic Assembly Adhesive Glue Manufacturer
Epoxies are commonly used in electronic assembly due to their high strength and resistance to chemicals and temperature. They are ideal for bonding metals, ceramics, and plastics. Acrylics are known for their fast curing time and excellent adhesion to a variety of substrates, including metals, plastics, and glass. They are also resistant to UV light and weathering. Silicones are flexible and have excellent electrical insulation properties, making them suitable for sealing and bonding electronic components.
Polyurethanes are known for their toughness and resistance to impact and abrasion, making them ideal for applications that require high durability. When selecting an adhesive for electronic assembly, it is essential to consider the operating conditions such as temperature, humidity, and exposure to chemicals or solvents.
The curing time of the adhesive should also be taken into account as it can affect the production cycle time. Environmental factors such as RoHS compliance should also be considered when selecting an adhesive for electronic assembly.
The Role of Quality Control in Electronic Assembly
The importance of quality control in electronic assembly cannot be overstated. It is a critical step in the manufacturing process that helps to ensure that the final product meets the required standards for performance and reliability. Quality control measures are designed to identify defects and issues early in the manufacturing process, reducing the risk of costly rework or product recalls.
This is particularly important in electronic assembly, where even minor defects can have significant consequences for the performance and safety of the final product. One of the key benefits of quality control is that it helps to ensure that all components are correctly assembled and that they meet the required specifications. This is achieved through a range of testing and inspection processes, which are designed to identify any issues with the components or the assembly process itself.
By catching these issues early, manufacturers can take corrective action before the final product is shipped to customers. Another benefit of quality control is that it helps to maintain consistency in the manufacturing process. By ensuring that all components are correctly assembled and meet the required specifications, manufacturers can produce products that are consistent in terms of performance and reliability. This is important for customers who rely on these products for critical applications, such as medical devices or aerospace components.
The Impact of Adhesive Selection on Electronic Assembly Quality
When it comes to electronic devices, the adhesive used to hold components together is a crucial factor in ensuring their quality and reliability. Choosing the right adhesive can make all the difference in preventing product failures, maintaining optimal performance, and keeping costs down. Adhesive-related issues can cause a range of problems, such as poor adhesion between components, delamination of layers, and outgassing of volatile compounds.
Poor adhesion can lead to components becoming loose or falling off entirely, while delamination can cause layers to separate and compromise the integrity of the device. Outgassing can release harmful substances that can damage sensitive electronic components or interfere with their performance. Therefore, it is essential to carefully consider the adhesive properties and compatibility with the materials being used in electronic assembly to avoid these issues.
Common Adhesive Selection Mistakes and their Consequences
When selecting adhesives for electronic assembly, it is important to consider a range of factors beyond just cost. Environmental factors such as temperature, humidity, and chemical exposure can all impact the performance of the adhesive, so it is important to choose an adhesive that is specifically designed to withstand these conditions. Additionally, it is crucial to test the adhesive before use to ensure that it will provide the necessary level of adhesion and performance.
Failing to do so can lead to poor adhesion, reduced performance, and increased costs due to the need for rework or replacement. By taking the time to carefully select and test adhesives for electronic assembly, manufacturers can ensure that their products meet the highest standards of quality and reliability.
Key Factors to Consider when Selecting Electronic Assembly Adhesives
Several key factors need to be considered when selecting adhesives for electronic assembly, including substrate material compatibility, operating conditions, curing time, environmental factors, and regulatory requirements. These factors can impact the performance and reliability of the final product.
The Importance of Adhesive Testing and Validation in Quality Control
Adhesive testing and validation are critical aspects of quality control in electronic assembly. Testing helps to ensure that the adhesive selected meets the required standards for performance and reliability. Common testing methods used in electronic assembly include lap shear testing, peel testing, and thermal cycling testing.
Best Practices for Electronic Assembly Adhesive Application and Inspection
Some of the best practices for adhesive application and inspection in electronic assembly include ensuring that all surfaces are clean and free from contaminants before applying the adhesive, using the correct amount of adhesive, and ensuring that the adhesive is cured correctly. Inspection should be carried out at every stage of the manufacturing process to identify defects early.
The Role of Quality Control in Ensuring Adhesive Compatibility with Electronic Components
Adhesive compatibility with electronic components is critical to ensure that the final product meets the required standards for performance and reliability. Quality control measures can help to ensure that adhesives are compatible with all components used in electronic assembly.
The Benefits of Implementing a Quality Control Program for Electronic Assembly Adhesive Selection
Implementing a quality control program for adhesive selection in electronic assembly can lead to several benefits, including improved product quality and reliability, reduced costs due to fewer defects and rework, increased customer satisfaction, and compliance with regulatory requirements.
Conclusion: The Critical Role of Quality Control in Electronic Assembly Adhesive Selection
In conclusion, quality control is a critical aspect of electronic assembly adhesive selection. Selecting the right adhesive is essential to ensure the quality and reliability of electronic devices. Quality control measures help to identify defects early in the manufacturing process, reducing costs and improving customer satisfaction. Implementing a quality control program for adhesive selection can lead to several benefits for manufacturers and customers alike.
For more about choosing the Importance of Quality Control in Electronic Assembly Adhesive Selection,you can pay a visit to DeepMaterial at https://www.electronicadhesive.com/solving-common-challenges-with-electronic-assembly-adhesive/ for more info.