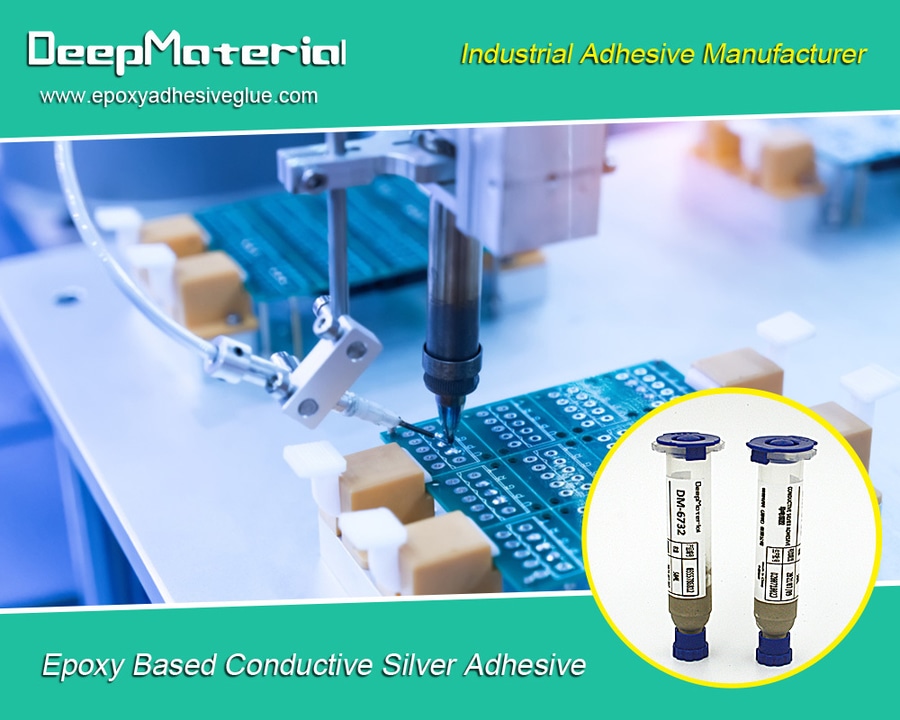
#Industry News
The Benefits of Using Composite Bonding Adhesives in Manufacturing
Best Epoxy Composite Bonding Adhesive Glue Manufacturer
Composite bonding adhesives are a type of adhesive that is used to bond composite materials together. Composite materials are made up of two or more materials that have different properties, such as strength, weight, nd durability. Composite bonding adhesives are important in manufacturing because they provide a strong and durable bond between the different materials, which improves the overall strength and durability of the composite material.
Advantages of Using Composite Bonding Adhesives in Manufacturing
Improved durability and strength of composite materials: Composite bonding adhesives are specially designed to create a strong and lasting bond between different materials in a composite material. This type of adhesiave is commonly used in the manufacturing of various products such as aircraft, boats, cars, and even buildings. The adhesive works by creating a chemical bond between the different materials, which results in a strong and durable bond that can withstand extreme conditions.
Composite bonding adhesives are typically made from high-performance polymers that have excellent adhesive properties. These adhesives are also resistant to water, heat, and chemicals, which makes them ideal for use in harsh environments. Additionally, the use of composite bonding adhesives can help reduce the weight of composite materials, which can lead to improved fuel efficiency and lower operating costs. materials, making them an essential component in many industries.
Enhanced design flexibility with composite bonding adhesives: Composite bonding adhesives are a type of adhesive that can bond different types of materials together, such as metals, plastics, ceramics, and composites. This allows for greater design flexibility in manufacturing, as designers can combine different materials to create unique and innovative products.
For example, composite bonding adhesives can be used to bond metal to plastic, which is useful in creating lightweight and durable products. Additionally, these adhesives can be used to bond dissimilar materials, such as carbon fiber to aluminum, which is important in the aerospace industry.
Reduced weight and cost of manufacturing with composite bonding adhesives: Composite bonding adhesives are a popular choice for manufacturers who want to reduce the weight and cost of their products. These adhesives are designed to bond lightweight materials together, such as plastics, composites, and metals.
By using these adhesives, manufacturers can create products that are lighter and more efficient, without sacrificing strength or durability. This is particularly important in industries such as aerospace, automotive, and construction, where weight reduction is a key factor in improving performance and reducing costs.
Increased resistance to environmental factors with composite bonding adhesives: Composite bonding adhesives are a type of adhesive that is designed to bond two or more materials together. They are often used in industrial applications where the strength and durability of the bond are critical.
One of the main advantages of composite bonding adhesives is their resistance to environmental factors such as moisture, heat, and cold. This means that they can be used in harsh environments where traditional bonding methods may fail. For example, composite bonding adhesives are commonly used in the aerospace industry to bond components together in aircraft and spacecraft.
Improved safety and reliability of composite materials: Composite bonding adhesives are essential in the manufacturing of composite materials, which are widely used in various industries such as aerospace, automotive, construction, and sports equipment. These adhesives are designed to bond different materials together, such as carbon fibers, fiberglass, Kevlar, and other polymers.
The bonding process involves the application of the adhesive to the surfaces of the materials to be bonded, followed by curing or hardening of the adhesive. The resulting bond is strong and durable, with excellent resistance to impact, fatigue, and environmental factors such as moisture and temperature changes.
Applications of Composite Bonding Adhesives in Various Industries
Aerospace industry: Composite bonding adhesives are used extensively in the aerospace industry to bond lightweight materials together. This reduces the weight of aircraft, which improves fuel efficiency and reduces emissions.
Automotive industry: Composite bonding adhesives are useful in the car manufacturing industry for bonding lightweight materials together. This helps to reduce the weight of cars, thereby improving fuel efficiency and reduces emissions.
Construction industry: Composite bonding adhesives are used in the construction industry to bond different types of building materials together. This allows for greater design flexibility and reduces the weight of buildings.
Marine industry: Composite bonding adhesives are used in the marine industry to bond different types of materials together, such as fiberglass and wood. This improves the overall strength and durability of boats and other marine vessels.
Sports equipment industry: Composite bonding adhesives are used in the sports equipment industry to bond different types of materials together, such as carbon fiber and aluminum. This improves the overall strength and durability of sports equipment such as bicycles and tennis rackets.
Comparison of Composite Bonding Adhesives with Traditional Bonding Methods
Strength and durability: Composite bonding adhesives provide a stronger and more durable bond than traditional bonding methods such as welding or riveting.
Design flexibility: Composite bonding adhesives allow for greater design flexibility than traditional bonding methods, as they can be used to bond different types of materials together.
Weight and cost: Composite bonding adhesives can reduce the weight and cost of manufacturing by allowing for the use of lightweight materials.
Resistance to environmental factors: Composite bonding adhesives are often more resistant to environmental factors such as moisture, heat, and cold than traditional bonding methods.
Safety and reliability: Composite bonding adhesives provide a strong and durable bond between different materials, which improves the overall safety and reliability of the finished product.
Future Developments and Trends in Composite Bonding Adhesives Technology
Advancements in nanotechnology: Nanotechnology is being used to develop new types of composite bonding adhesives that are stronger, more durable, and more resistant to environmental factors than current adhesives.
Development of bio-based adhesives: Bio-based adhesives are being developed that are made from renewable resources such as plant-based materials. These adhesives are more environmentally friendly than traditional petroleum-based adhesives.
Increased use of automation in manufacturing processes: Automation is being used more extensively in manufacturing processes, which allows for greater precision in applying composite bonding adhesives. This improves the overall quality and consistency of finished products.
Conclusion
Composite bonding adhesives are an important part of modern manufacturing processes. They provide a strong and durable bond between different types of materials, which improves the overall strength, durability, safety, and reliability of finished products. As technology continues to advance, new types of composite bonding adhesives will be developed that are even stronger, more durable, and more environmentally friendly than current adhesives. It is important for manufacturers to stay up-to-date with these advancements in order to remain competitive in their respective industries.
For more about choosing the Composite Bonding Adhesives in Manufacturing, you can pay a visit to DeepMaterial at https://www.epoxyadhesiveglue.com/ for more info.