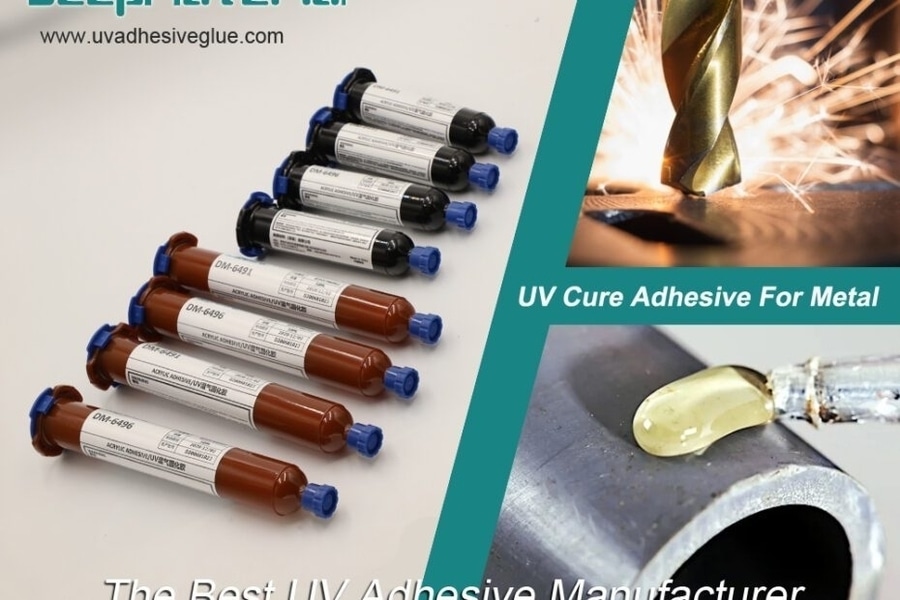
#Industry News
The Role of UV and Light Curing Adhesives in Automotive Manufacturing
Best UV and Light Curing Adhesive Glue Manufacturer
Adhesives play a crucial role in the manufacturing of automobiles, providing strong and durable bonds between various components. One type of adhesive that has gained popularity in recent years is UV and light curing adhesives. These adhesives offer several advantages over traditional adhesives, including faster curing times, improved bond strength, reduced waste, and increased design flexibility. In this article, we will explore the advantages, types, applications, and challenges of using UV and light curing adhesives in automotive manufacturing.
Advantages of UV and Light Curing Adhesives in Automotive Manufacturing
One of the main advantages of UV and light curing adhesives is their faster curing times. Unlike traditional adhesives that require hours or even days to fully cure, UV and light curing adhesives can cure within seconds or minutes when exposed to UV or visible light. This significantly reduces production time and allows for faster assembly of automotive components.
In addition to faster curing times, UV and light curing adhesives also offer improved bond strength. The curing process of these adhesives creates a strong and durable bond that can withstand the harsh conditions of automotive applications, such as temperature fluctuations, vibrations, and exposure to chemicals. This ensures the longevity and reliability of the bonded components.
Another advantage of UV and light curing adhesives is their reduced waste and environmental impact. Traditional adhesives often require mixing and application in large quantities, leading to excess adhesive that goes to waste. UV and light curing adhesives, on the other hand, can be applied in precise amounts, minimizing waste. Additionally, these adhesives do not contain volatile organic compounds (VOCs) or emit harmful fumes during the curing process, making them more environmentally friendly.
Furthermore, UV and light curing adhesives offer increased design flexibility in automotive manufacturing. These adhesives can be formulated to have different viscosities, allowing for easy application on various substrates and complex geometries. They can also be used to bond dissimilar materials, such as metal to plastic or glass to plastic, expanding the design possibilities for automotive components.
Types of UV and Light Curing Adhesives Used in Automotive Manufacturing
There are several types of UV and light curing adhesives that are commonly used in automotive manufacturing. These include acrylics, epoxies, silicones, and polyurethanes.
Acrylic adhesives are known for their high bond strength and excellent resistance to temperature, chemicals, and UV exposure. They are commonly used for bonding interior and exterior components, such as trim, emblems, and badges. Acrylic adhesives also provide good adhesion to a wide range of substrates, including metals, plastics, and composites.
Epoxies are another type of UV and light curing adhesive that are widely used in automotive manufacturing. They offer high bond strength, excellent chemical resistance, and good thermal stability. Epoxies are often used for structural bonding applications, such as bonding metal brackets or reinforcing joints. They can also be used for glass bonding and sealing applications.
Silicone adhesives are known for their flexibility, high temperature resistance, and excellent electrical insulation properties. They are commonly used for sealing and gasketing applications in automotive manufacturing, such as sealing windows, doors, and engine compartments. Silicone adhesives also provide good adhesion to a variety of substrates, including metals, plastics, and glass.
Polyurethane adhesives are another popular choice for automotive manufacturing. They offer high bond strength, excellent flexibility, and good resistance to temperature and chemicals. Polyurethane adhesives are commonly used for bonding interior and exterior components, such as body panels, spoilers, and mirrors. They can also be used for structural bonding applications.
Applications of UV and Light Curing Adhesives in Automotive Manufacturing
UV and light curing adhesives have a wide range of applications in automotive manufacturing. Some of the common applications include bonding of interior and exterior components, glass bonding, structural bonding, and sealing and gasketing.
In the bonding of interior and exterior components, UV and light curing adhesives are used to bond various components, such as trim, emblems, badges, and panels. These adhesives provide strong and durable bonds that can withstand the harsh conditions of automotive applications, ensuring the longevity and reliability of the bonded components.
Glass bonding is another important application of UV and light curing adhesives in automotive manufacturing. These adhesives are used to bond windshields, side windows, and rear windows to the vehicle body. The strong and durable bonds created by UV and light curing adhesives ensure the safety and structural integrity of the vehicle.
Structural bonding is another critical application of UV and light curing adhesives in automotive manufacturing. These adhesives are used to bond metal brackets, reinforcements, and joints, providing strength and stability to the vehicle structure. The fast curing times of UV and light curing adhesives allow for efficient assembly of structural components.
Sealing and gasketing is another important application of UV and light curing adhesives in automotive manufacturing. These adhesives are used to seal windows, doors, engine compartments, and other areas where a watertight or airtight seal is required. The flexibility and excellent adhesion properties of UV and light curing adhesives ensure effective sealing and gasketing.
Factors to Consider When Choosing UV and Light Curing Adhesives for Automotive Manufacturing
When choosing UV and light curing adhesives for automotive manufacturing, several factors need to be considered. These include substrate materials, curing requirements, environmental conditions, and production volume and speed.
Substrate materials play a crucial role in adhesive selection. Different adhesives have different adhesion properties and may be more suitable for bonding specific substrates. It is important to consider the compatibility of the adhesive with the substrate materials to ensure a strong and durable bond.
Curing requirements also need to be taken into account. Different adhesives have different curing mechanisms and may require specific wavelengths or intensities of light for curing. It is important to choose an adhesive that can be effectively cured within the given production time and conditions.
Environmental conditions, such as temperature, humidity, and exposure to chemicals, should also be considered when selecting UV and light curing adhesives. Some adhesives may have better resistance to temperature or chemicals, making them more suitable for specific automotive applications.
Production volume and speed are also important factors to consider. Some UV and light curing adhesives may require specialized equipment or longer curing times, which may not be feasible for high-volume production. It is important to choose an adhesive that can be efficiently applied and cured within the production constraints.
Conclusion: The Importance of UV and Light Curing Adhesives in Automotive Manufacturing
UV and light curing adhesives play a crucial role in automotive manufacturing, offering several advantages over traditional adhesives. These adhesives provide faster curing times, improved bond strength, reduced waste, and increased design flexibility. They are used in a wide range of applications, including bonding of interior and exterior components, glass bonding, structural bonding, and sealing and gasketing.
For more about choosing a UV adhesive, you can pay a visit to DeepMaterial at https://www.uvadhesiveglue.com/uv-adhesive/ for more info.