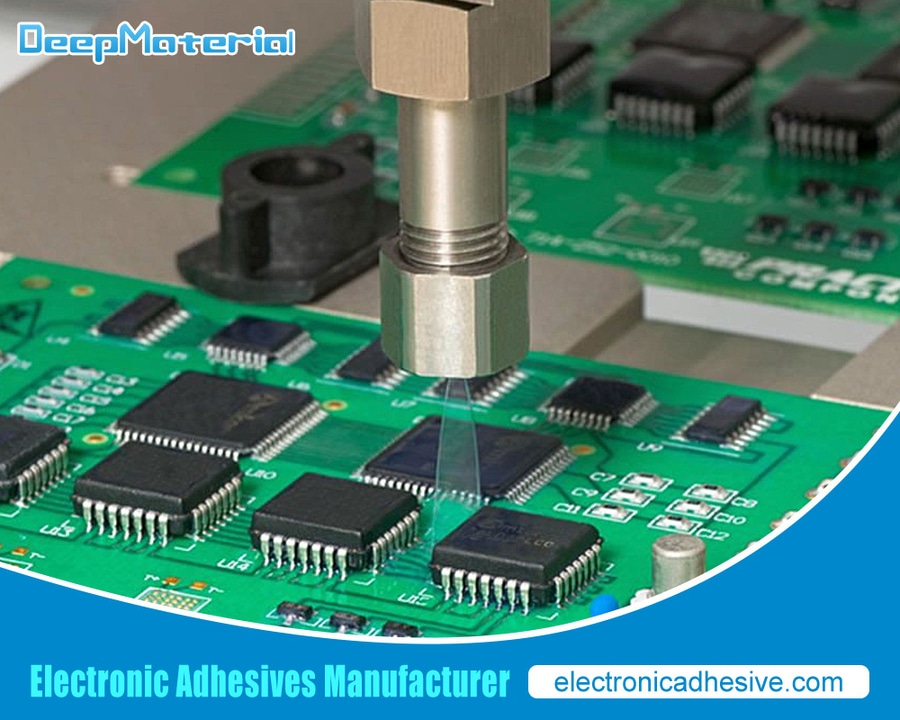
#Industry News
Innovative Approaches to MEMS Adhesive Bonding for Reliable Device Integration
Best MEMS Adhesive Bonding for Reliable Device Integration Manufacturer
In the world of microelectromechanical systems (MEMS), the quest for reliable, efficient, and cost-effective device integration is a constant challenge. The intricate dance of design, fabrication, and assembly requires not only precision but also innovation. One critical aspect that often gets overlooked in this process is adhesive bonding – a seemingly simple yet profoundly complex procedure that can make or break the overall performance and reliability of MEMS devices.
In this blog post, we delve into the innovative approaches to MEMS adhesive bonding that are revolutionizing the way we integrate these tiny yet powerful devices into our everyday lives. We will explore how these cutting-edge techniques are pushing the boundaries of what’s possible, ensuring MEMS devices are not only more reliable but also more robust and versatile than ever before.
Challenges in MEMS Adhesive Bonding
The miniaturization and complexity of MEMS devices pose significant challenges in adhesive bonding. As MEMS devices become smaller and more intricate, the bonding process must be able to accommodate these complex geometries and ensure precise alignment of the components. Additionally, the compatibility of adhesive materials with MEMS materials is a challenge. MEMS devices are often made from a variety of materials, such as silicon, polymers, and metals, and the adhesive material must be able to bond to these different materials without compromising their properties. Environmental factors, such as temperature, humidity, and chemical exposure, can also affect the performance of adhesive bonding in MEMS devices.
Traditional Approaches to MEMS Adhesive Bonding
Anodic bonding is a commonly used technique for bonding silicon-based MEMS devices. It involves applying a high voltage to the silicon wafer and a glass substrate, causing a chemical reaction that forms a strong bond between the two materials. Eutectic bonding is another traditional approach, which involves heating two materials with a low melting point until they form a eutectic alloy that bonds the components together. Wafer bonding is a technique that involves bonding two wafers together using an adhesive material, such as an epoxy or a polymer.
Innovative Approaches to MEMS Adhesive Bonding
To overcome the challenges in MEMS adhesive bonding, researchers have developed innovative approaches that improve the adhesion between the components of MEMS devices. Surface modification techniques, such as plasma treatment, chemical functionalization, and laser ablation, can be used to enhance the adhesion properties of the materials. Novel adhesive materials, such as polymer-based adhesives, nanocomposite adhesives, and bio-inspired adhesives, have also been developed to improve the bonding strength and compatibility with MEMS materials. Advanced bonding techniques, such as microfluidic bonding, transfer printing, and direct write printing, offer new ways to integrate MEMS devices with high precision and reliability.
Surface Modification Techniques for Improved Adhesion
Surface modification techniques can improve the adhesion properties of materials used in MEMS adhesive bonding. Plasma treatment involves exposing the surface of the material to a plasma gas, which creates reactive species that can chemically bond to the adhesive material. Chemical functionalization involves modifying the surface of the material with functional groups that can interact with the adhesive material. Laser ablation uses a laser beam to remove a thin layer of material from the surface, creating a roughened surface that enhances the adhesion.
Novel Adhesive Materials for MEMS Bonding
Novel adhesive materials have been developed to improve the bonding strength and compatibility with MEMS materials. Polymer-based adhesives offer advantages such as flexibility, low cost, and ease of processing. Nanocomposite adhesives incorporate nanoparticles into the adhesive material, which can enhance the mechanical properties and adhesion strength. Bio-inspired adhesives are inspired by natural adhesion mechanisms, such as gecko feet or mussel adhesive proteins, and offer unique properties such as reversible adhesion or self-healing capabilities.
Advanced Bonding Techniques for MEMS Integration
Advanced bonding techniques offer new ways to integrate MEMS devices with high precision and reliability. Microfluidic bonding involves using microfluidic channels to deliver the adhesive material to the bonding interface, ensuring uniform coverage and minimizing voids or defects. Transfer printing involves transferring pre-fabricated MEMS devices onto a target substrate using a stamp or a pick-and-place method. Direct write printing uses a printing technique, such as inkjet printing or aerosol jet printing, to deposit the adhesive material onto the bonding interface with high precision.
Characterization and Testing of Adhesive Bonded MEMS Devices
Characterization and testing of adhesive bonded MEMS devices are crucial to ensure their reliability and performance. Mechanical testing involves measuring the bonding strength, adhesion energy, and fracture toughness of the adhesive bond. Electrical testing is performed to evaluate the electrical conductivity and resistance of the adhesive bond. Thermal testing is conducted to assess the thermal stability and resistance of the adhesive bond to temperature variations.
Applications of Innovative MEMS Adhesive Bonding
Innovative MEMS adhesive bonding techniques have a wide range of applications in various industries. In the biomedical field, adhesive bonded MEMS devices are used in implantable medical devices, drug delivery systems, and biosensors. In microfluidics, adhesive bonding is used to fabricate microfluidic channels, valves, and pumps for lab-on-a-chip devices. In the aerospace and defense industry, adhesive bonded MEMS devices are used in navigation systems, sensors, and actuators for aircraft and spacecraft.
Future Directions in MEMS Adhesive Bonding Research
Future research in MEMS adhesive bonding will focus on the development of new adhesive materials and techniques. Researchers will continue to explore novel materials, such as conductive adhesives or self-healing adhesives, that can enhance the functionality and reliability of MEMS devices. Integration of MEMS devices with flexible substrates, such as polymers or textiles, will also be an area of interest. Additionally, there is a need to explore new applications for MEMS adhesive bonding, such as energy harvesting, wearable electronics, and Internet of Things (IoT) devices.
Conclusion
Innovative approaches to MEMS adhesive bonding have addressed the challenges posed by miniaturization, complexity, and compatibility of materials. Surface modification techniques, novel adhesive materials, and advanced bonding techniques have improved the adhesion properties and reliability of MEMS devices. Characterization and testing methods ensure the performance and functionality of adhesive bonded MEMS devices. These advancements have enabled the development of MEMS devices for various applications in biomedical, microfluidics, aerospace, and defense industries.
For more about choosing the MEMS Adhesive Bonding for Reliable Device Integration, you can pay a visit to DeepMaterial at https://www.electronicadhesive.com/ for more info.