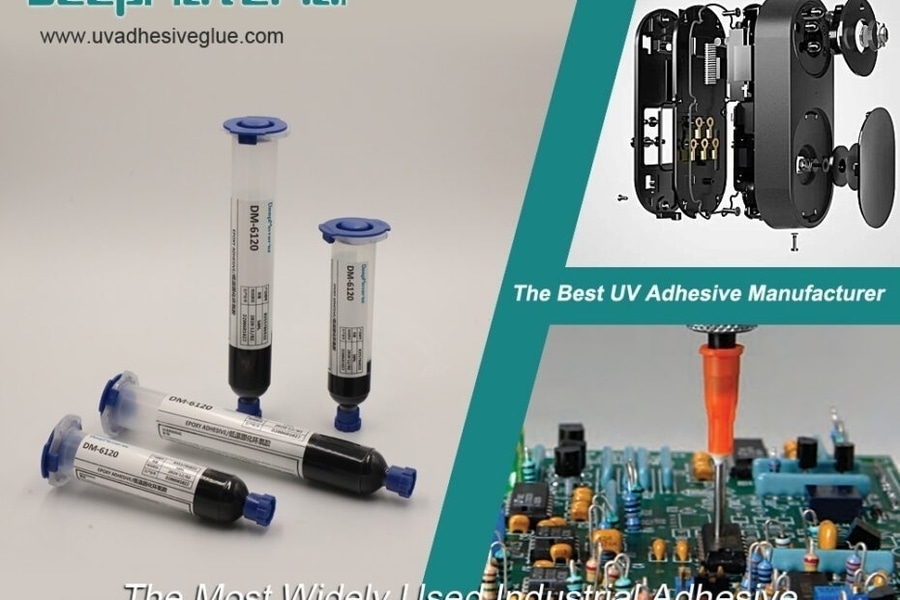
#Industry News
Lighting the Way to Reliability: Electronic Assembly UV Curing Adhesive Solutions
Best UV Curing Adhesive Glue Manufacturer
Electronic assembly talks about how electronics components are connected in electronic devices and products. The components are planted on a PCB or some kind of substrate. Electronic assembly requires that electronics components are securely attached onto the printed circuit board. Some of the components in question include microchips, capacitors, resistors, connectors, and many others. Bonding is extremely important when it comes to electronic assembly.
In this article, we discuss the benefits of using electronic assembly UV curing adhesive solutions for electronic assembly purposes. After reading this post, you can decide if it’s okay to invest in such solutions or not.
The Significance of Electronic Assembly UV Curing Adhesives
The assembly of electronic components is a vital process in the manufacture of electronics devices. Whether it is smartphones or laptops or medical devices, components assembly remains an indispensable part of the manufacturing process. Proper assembly is essential for ensuring the functionality, reliability, and longevity of electronic products.
Adhesives play an important role in the electronic assembly industry. As a matter of fact, they have changed how components are attached to a printed circuit board. That is because these adhesives are not just for attachment. They can also be used to ensure environmental protection, electrical insulation, and thermal management.
Electronic assembly UV curing adhesives guarantee certain benefits that one can never get with traditional bonding methods. The significance of using adhesives for electronic assembly will be highlighted in the section below;
Precision & Control– UV curing adhesives offer meticulous control during the curing process. This allows manufacturers to apply adhesive with pinpoint accuracy to designated areas. This precision ensures an even and consistent distribution before the curing phase, a critical factor in establishing dependable bonds, particularly in the realm of miniaturized electronics.
Reliability – Electronic assembly UV curing adhesives are famous for creating long lasting bonds. Fortunately, that will help prolong the lifespan of the device. This way, it will also increase its reliability. This is especially important in many industries.
Miniaturization and Component Placement– As electronics continue to miniaturize, precise adhesive placement becomes increasingly critical. UV curing adhesives excel in these applications, providing the accuracy needed to bond tiny components effectively.
Compatibility – Electronic assembly UV curing adhesives demonstrate a high level of compatibility for various electronic materials. This is why they can be used for various electronics applications.
Strong bonds – Creating strong bonds between electronics components and different substrates is essential for high-quality assembly and device durability. These bonds are actually stronger than the substrates or electronic materials.
Swift Curing – UV curing adhesives undergo rapid curing upon exposure to ultraviolet (UV) light. This swift curing mechanism substantially shortens assembly duration, leading to heightened production efficiency. This advantage is particularly valuable in electronic manufacturing, where there is a pressing need to rapidly attach large volumes of components, giving UV curing adhesives a competitive edge.
Environmental Safety – Electronic assembly UV curing adhesives are safe to use in any environment because they do not contain any harmful chemicals. The environmentally safe nature of UV adhesives makes them perfect for such applications. It also important to mention that UV adhesives are not known to generate heat.
UV curing adhesive solutions are highly significant in electronic assembly due to their rapid curing, precision, strength, environmental benefits, and compatibility with electronic materials. They contribute to the efficient and reliable manufacturing of electronic devices, ensuring that these products meet stringent performance and quality standards.
Potential Challenges & Considerations in UV Curing Adhesives
The advantages associated with using electronic assembly UV curing adhesives are numerous. However, the use of such adhesives is not devoid of certain challenges and considerations that manufacturers need to be aware of for optimal implementations.
Adhesion Selection for Certain Components
Temperature Resistance – Electronic components may operate under varying temperature conditions. Adhesive selection should consider the temperature range in which the assembly will operate to ensure the adhesive’s thermal stability. In high-temperature applications, the adhesive must resist heat-induced degradation.
Material Compatibility – All the electronic components and substrates do not have the same properties. They exhibit slight variations in their properties and surface adherence. Choosing the UV curing adhesive for specific applications is key to a successful electronic assembly. Using the wrong adhesives can produce weak bonds and culminate in product failures.
Chemical Resistance – There is the possibility of exposing an electronic assembly to chemicals. For instance, they can come in direct contact with cleaning reagents during their service life. The best thing is to opt for electronic assembly UV curing adhesives because they exhibit chemically resistant properties that make them inert to such solvents.
Adhesives used in electronic assembly must exhibit good electrical insulation properties to prevent short circuits or electrical leakage. Understanding the dielectric strength and resistivity of the adhesive is essential, especially when bonding close to sensitive electronic circuitry.
Design Considerations for Choosing UV Curing Adhesives
UV Exposure – Electronic assembly design ought to take into consideration how much UV light exposure will be needed for the bond to cure. Structures that are enclosed may pose a bit of challenge in this regard. Because getting light to reach all the components may be difficult.
Curing Equipment Integration – Integrating UV curing equipment into the production line should be carefully planned. Proper alignment and calibration of UV lamps or LEDs to ensure uniform curing across the entire assembly are essential. Any misalignment or inadequate intensity can result in incomplete or uneven curing.
By tackling these challenges and taking these considerations into account, electronic assembly processes can seamlessly incorporate UV curing adhesives. Manufacturers should meticulously assess their unique application needs and collaborate closely with adhesive suppliers to select the optimal formulations and procedures, thus ensuring the success of electronic bonding.
Final Words
Apparently, electronics assembly UV curing adhesives are ideal for bonding electronic components to any substrate. They have proven to be exceptional over and again. Consider investing in such adhesives as that will help guarantee long-lasting devices.
For more about choosing the electronics assembly UV curing adhesives, you can pay a visit to DeepMaterial at https://www.uvadhesiveglue.com/ for more info.