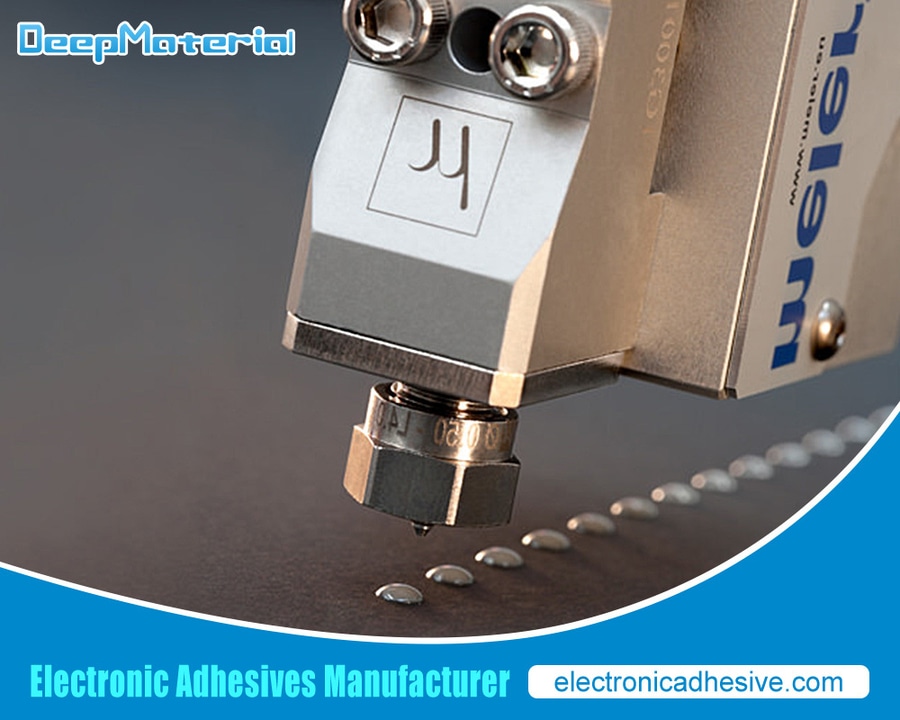
#Industry News
Exploring The Benefits of FPC Bonding Adhesive in Electronics Manufacturing
Best FPC Bonding Adhesive Glue Manufacturer
FPC bonding adhesive plays a crucial role in the electronics manufacturing industry. It is a specialized adhesive that is used to bond flexible printed circuits (FPCs) to various substrates and components. This adhesive is designed to provide a strong and reliable bond, ensuring the durability and functionality of electronic devices. In this article, we will explore the composition and importance of FPC bonding adhesive, as well as its advantages over traditional bonding methods.
Electronic Adhesive Electronic Glue Supplier And Factory China
Understanding FPC Bonding Adhesive
FPC bonding adhesive is a type of adhesive that is specifically formulated for bonding flexible printed circuits (FPCs) to different substrates and components. It is composed of a combination of polymers, resins, and additives that provide the necessary adhesion and flexibility required for bonding FPCs. The adhesive is typically applied in a thin layer between the FPC and the substrate or component, and then cured to form a strong bond.
The importance of FPC bonding adhesive in electronics manufacturing cannot be overstated. It is a critical component in the assembly process, as it ensures the proper functioning and reliability of electronic devices. Without a strong and reliable bond, FPCs can become detached from the substrate or component, leading to malfunctioning or non-functional devices. FPC bonding adhesive also provides protection against environmental factors such as moisture, dust, and temperature fluctuations, which can affect the performance of electronic devices.
Advantages of FPC Bonding Adhesive over Traditional Bonding Methods
FPC bonding adhesive offers several advantages over traditional bonding methods such as soldering or mechanical fastening. Firstly, FPC bonding adhesive provides a more durable and reliable bond compared to soldering or mechanical fastening. The adhesive forms a strong and flexible bond that can withstand vibrations, shocks, and thermal cycling, ensuring the longevity and reliability of electronic devices.
Secondly, FPC bonding adhesive offers greater flexibility and design freedom. Unlike soldering or mechanical fastening, which require specific shapes and sizes of components, FPC bonding adhesive can be used to bond FPCs to various substrates and components of different shapes and sizes. This allows for more flexibility in the design and layout of electronic devices, enabling manufacturers to create smaller and more compact devices.
Lastly, FPC bonding adhesive allows for easier and more efficient manufacturing processes. It eliminates the need for complex soldering or mechanical fastening techniques, reducing the time and effort required for assembly. The adhesive can be applied using automated dispensing systems, ensuring consistent and precise application. This results in higher production yields and lower manufacturing costs.
Improved Durability and Reliability
FPC bonding adhesive significantly improves the durability and reliability of electronic devices. The adhesive forms a strong and flexible bond between the FPC and the substrate or component, ensuring that they remain securely attached even under harsh conditions. This is particularly important in applications where the devices are subjected to vibrations, shocks, or thermal cycling.
One example of successful implementation of FPC bonding adhesive is in the automotive industry. In automotive electronics, where devices are exposed to extreme temperatures, vibrations, and moisture, FPC bonding adhesive has proven to be highly effective in ensuring the durability and reliability of electronic components. It provides a strong bond that can withstand the harsh conditions of automotive environments, resulting in longer-lasting and more reliable electronic devices.
Enhanced Flexibility and Design Freedom
FPC bonding adhesive offers enhanced flexibility and design freedom in electronics manufacturing. Unlike traditional bonding methods such as soldering or mechanical fastening, which require specific shapes and sizes of components, FPC bonding adhesive can be used to bond FPCs to various substrates and components of different shapes and sizes.
This flexibility allows manufacturers to design and create electronic devices with unique and innovative form factors. For example, FPC bonding adhesive has been successfully implemented in the development of flexible displays, where FPCs are bonded to flexible substrates to create bendable and foldable screens. This technology has revolutionized the display industry, enabling the production of curved and flexible displays for smartphones, televisions, and other electronic devices.
FPC bonding adhesive also offers design freedom in terms of circuit layout and interconnectivity. Unlike soldering, which requires specific locations for solder joints, FPC bonding adhesive allows for more flexibility in the placement of components and interconnections. This enables manufacturers to optimize the layout of electronic devices, improving performance and functionality.
Cost Savings
FPC bonding adhesive can result in significant cost savings in electronics manufacturing. Firstly, the adhesive eliminates the need for complex soldering or mechanical fastening techniques, reducing the time and effort required for assembly. This leads to higher production yields and lower manufacturing costs.
Secondly, FPC bonding adhesive allows for the use of less expensive materials. Unlike soldering, which requires specific types of components and substrates, FPC bonding adhesive can be used with a wide range of materials. This allows manufacturers to choose more cost-effective options without compromising on performance or reliability.
Compatibility with Various Substrates and Components
FPC bonding adhesive is compatible with a wide range of substrates and components, making it a versatile solution for electronics manufacturing. The adhesive can bond FPCs to substrates such as glass, plastic, metal, and ceramic, as well as components such as integrated circuits, connectors, and sensors.
This compatibility allows manufacturers to use FPC bonding adhesive in various industries and applications. For example, in the medical industry, FPC bonding adhesive is used to bond FPCs to medical devices such as pacemakers, defibrillators, and insulin pumps. The adhesive provides a secure and reliable bond that can withstand the demanding conditions of medical environments.
In the aerospace industry, FPC bonding adhesive is used to bond FPCs to aircraft components such as control panels, displays, and sensors. The adhesive ensures the durability and reliability of electronic devices in the extreme conditions of aerospace environments, including high temperatures, vibrations, and pressure differentials.
Application Techniques for FPC Bonding Adhesive
There are several application techniques for FPC bonding adhesive, depending on the specific requirements of the manufacturing process. The most common technique is automated dispensing, where the adhesive is applied in a controlled and precise manner using robotic dispensing systems. This technique ensures consistent and uniform application of the adhesive, resulting in reliable and high-quality bonds.
Other application techniques include screen printing, transfer tape, and die-cutting. Screen printing involves applying the adhesive through a fine mesh screen onto the substrate or component. Transfer tape involves pre-applying the adhesive onto a carrier film, which is then transferred onto the substrate or component. Die-cutting involves cutting the adhesive into specific shapes and sizes using a die-cutting machine, which are then applied to the substrate or component.
Electronic Adhesive Glue Manufacturers And Suppliers China
Final Thoughts
In conclusion, FPC bonding adhesive plays a crucial role in the electronics manufacturing industry. It provides a strong and reliable bond between flexible printed circuits (FPCs) and various substrates and components, ensuring the durability and functionality of electronic devices. FPC bonding adhesive offers several advantages over traditional bonding methods, including improved durability, reliability, flexibility, design freedom, and cost savings.
For more about choosing the Benefits of FPC Bonding Adhesive in Electronics Manufacturing, you can pay a visit to DeepMaterial at https://www.electronicadhesive.com/about/ for more info.