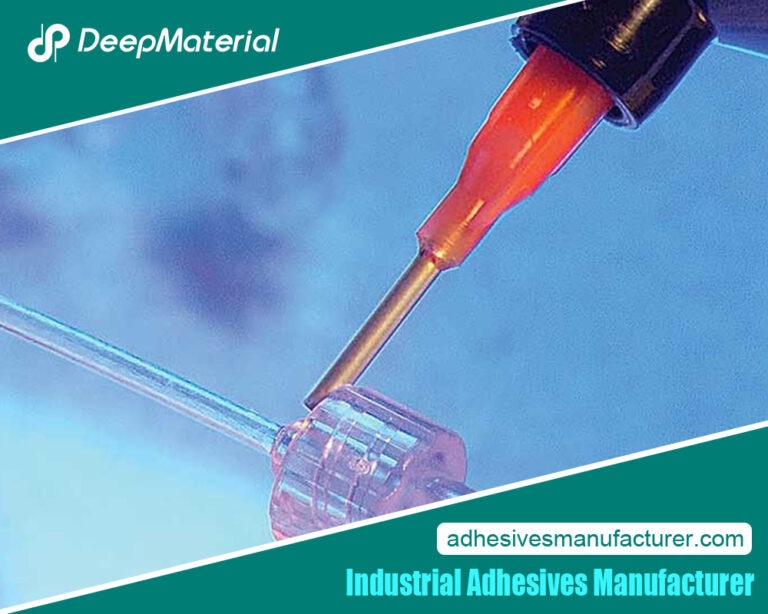
#Industry News
The Role of Electric Motor Epoxy in Preventing Corrosion and Extending Lifespan
Best Electronic Motor Epoxy Adhesive Glue Manufacturer
Electric motors are a crucial component in many industries, powering everything from machinery to vehicles. These motors are subjected to harsh operating conditions, including high temperatures, moisture, and corrosive chemicals. To protect them from these elements and ensure their longevity, electric motor epoxy coatings are used.
These coatings provide a protective barrier that prevents corrosion and extends the lifespan of the motor. In this article, we will be explaining the importance of electric motor epoxy coatings, their benefits, and how they can be applied effectively.
Importance of Electric Motor Epoxy Coatings
Epoxy coatings are a type of protective coating that is commonly used in various industries. They are made from a combination of epoxy resin and a curing agent, which chemically react to form a hard and durable surface. When applied to electric motors, epoxy coatings provide a protective barrier that shields the motor from environmental factors such as moisture, chemicals, and temperature fluctuations.
The importance of using epoxy coatings for electric motors cannot be overstated. These motors are often exposed to harsh conditions that can lead to corrosion and damage. Corrosion can cause the motor to malfunction, leading to costly repairs or even replacement. By applying epoxy coatings, the motor is protected from corrosion, ensuring its optimal performance and longevity.
How Corrosion Affects Electric Motors and Why Epoxy is the Solution
Corrosion is a common problem that affects electric motors. It occurs when metal surfaces come into contact with moisture or corrosive chemicals, leading to the degradation of the metal. In electric motors, corrosion can cause various issues such as reduced efficiency, increased friction, and even complete failure.
Epoxy coatings provide an effective solution to prevent corrosion in electric motors. The chemical properties of epoxy coatings make them resistant to moisture and chemicals, creating a barrier that prevents these substances from reaching the metal surface of the motor. This barrier not only protects the motor from corrosion but also improves its overall performance and efficiency.
The Science Behind Epoxy Coatings and Their Protective Properties
Epoxy coatings are made from a combination of epoxy resin and a curing agent. When these two components are mixed together, they undergo a chemical reaction called curing, which transforms them into a hard and durable surface. This cured surface provides excellent protection against corrosion, moisture, and chemicals.
The protective properties of epoxy coatings can be attributed to their chemical structure. Epoxy resins are composed of long chains of carbon atoms, which form a strong and stable network. This network creates a barrier that prevents moisture and chemicals from reaching the metal surface of the motor. Additionally, epoxy coatings have excellent adhesion properties, allowing them to bond tightly to the metal surface and provide long-lasting protection.
Different Types of Epoxy Coatings for Electric Motors and Their Applications
There are several different types of epoxy coatings available for electric motors, each with its own unique properties and applications. Some common types include:
Standard epoxy coatings: These coatings provide basic protection against corrosion and are suitable for general-purpose applications.
High-temperature epoxy coatings: These coatings are designed to withstand high temperatures and are ideal for motors that operate in extreme heat conditions.
Chemical-resistant epoxy coatings: These coatings are formulated to resist exposure to corrosive chemicals and are commonly used in industries such as chemical processing and wastewater treatment.
UV-resistant epoxy coatings: These coatings are designed to withstand exposure to ultraviolet (UV) radiation from sunlight and are suitable for outdoor applications.
The choice of epoxy coating depends on the specific requirements of the electric motor and the operating conditions it will be subjected to. It is important to consult with a coating specialist to determine the most suitable type of epoxy coating for your application.
The Benefits of Using Epoxy Coatings for Electric Motor Maintenance
Using epoxy coatings for electric motor maintenance offers several benefits. Firstly, these coatings provide a protective barrier that prevents corrosion, extending the lifespan of the motor and reducing the need for costly repairs or replacements. Additionally, epoxy coatings improve the efficiency and performance of the motor by reducing friction and heat buildup.
Furthermore, epoxy coatings are easy to apply and require minimal maintenance. Once applied, they provide long-lasting protection, reducing the need for frequent reapplication. This saves time and money in the long run, making epoxy coatings a cost-effective solution for electric motor maintenance.
How Epoxy Coatings Can Extend the Lifespan of Electric Motors
Epoxy coatings play a crucial role in extending the lifespan of electric motors. By providing a protective barrier against corrosion, these coatings prevent damage to the motor’s internal components. Corrosion can lead to increased friction, reduced efficiency, and even complete failure of the motor. By preventing corrosion, epoxy coatings ensure that the motor operates at its optimal performance level, extending its lifespan.
Real-world applications have demonstrated the effectiveness of epoxy coatings in extending the lifespan of electric motors. In industries such as manufacturing, where motors are subjected to harsh operating conditions, the use of epoxy coatings has significantly reduced the frequency of motor failures and increased their overall lifespan. This not only saves money on repairs and replacements but also improves productivity by minimizing downtime.
The Role of Proper Surface Preparation in Achieving Optimal Epoxy Coating Performance
Proper surface preparation is crucial for achieving optimal epoxy coating performance. The surface of the motor must be clean, dry, and free from contaminants such as oil, grease, and rust. Any existing corrosion or damage should be repaired before applying the epoxy coating.
The surface preparation process typically involves several steps, including cleaning, degreasing, and sanding. Cleaning and degreasing remove any dirt or contaminants from the surface, while sanding creates a rough texture that allows the epoxy coating to adhere properly. It is important to follow the manufacturer’s instructions and use the recommended cleaning agents and tools for surface preparation.
Final Words
In conclusion, electric motor epoxy coatings play a crucial role in protecting motors from corrosion and extending their lifespan. These coatings provide a protective barrier that shields the motor from moisture, chemicals, and temperature fluctuations. By preventing corrosion, epoxy coatings ensure optimal performance and efficiency of the motor, reducing the need for costly repairs or replacements.
When choosing an epoxy coating for your electric motor, it is important to consider factors such as operating conditions, adhesion properties, and compatibility. Proper surface preparation and application techniques are also crucial for achieving optimal results. By following best practices and staying informed about potential advancements in epoxy coatings, you can ensure that your electric motors are protected and perform at their best. Consider using epoxy coatings for your electric motors and reap the benefits of increased lifespan and improved performance.
For more about the electric motor epoxy, you can pay a visit to Deepmaterial at https://www.adhesivesmanufacturer.com/ for more info.