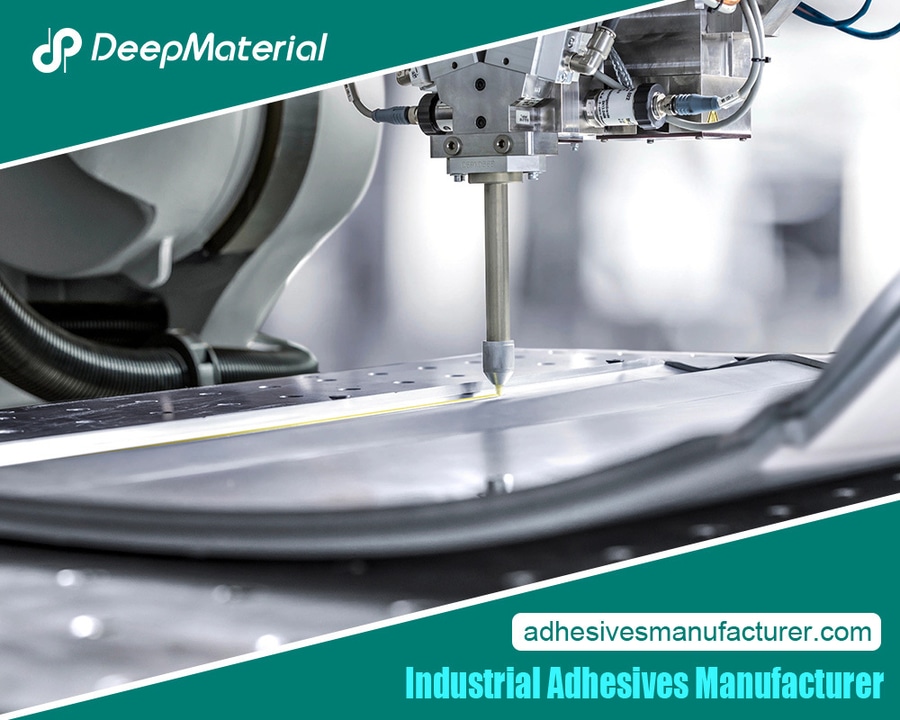
#Industry News
Common Challenges and Solutions In PCB Encapsulation Epoxy Applications
Best PCB Encapsulation Epoxy Adhesive Glue Manufacturer
PCB encapsulation epoxy refers to the process of using epoxy resin to protect and encapsulate printed circuit boards (PCBs) in electronic devices. Epoxy resin is a type of thermosetting polymer that, when cured, forms a strong and durable protective coating. This coating helps to protect the delicate electronic components on the PCB from environmental factors such as moisture, chemicals, and temperature fluctuations.
The importance of PCB encapsulation epoxy in electronic devices cannot be overstated. Without proper protection, PCBs are vulnerable to damage from moisture, dust, and other contaminants. This can lead to corrosion, short circuits, and ultimately, device failure. By encapsulating the PCB with epoxy resin, manufacturers can ensure that their electronic devices are reliable and long-lasting.
Common Challenges Faced in PCB Encapsulation Epoxy Applications
While PCB encapsulation epoxy offers numerous benefits, there are also several challenges that manufacturers must overcome. These challenges include:
Moisture and chemical resistance: One of the primary purposes of PCB encapsulation epoxy is to protect the PCB from moisture and chemicals. However, not all epoxy resins are created equal in terms of their resistance to these factors. It is important to select an epoxy resin that is specifically designed for the intended application and environment.
Thermal conductivity: Electronic devices generate heat during operation, and it is important for this heat to be dissipated effectively to prevent damage to the components. Some epoxy resins have low thermal conductivity, which can hinder heat dissipation. Manufacturers must consider the thermal properties of the epoxy resin and ensure that it is suitable for the specific application.
Adhesion to different substrates: PCBs are typically made from a variety of materials, including fiberglass, ceramic, and metal. The epoxy resin must have good adhesion to these substrates to ensure a strong bond and effective protection. Adhesion can be affected by factors such as surface preparation, curing conditions, and the compatibility of the epoxy resin with the substrate material.
Curing time and temperature: Epoxy resins require a specific curing time and temperature to achieve optimal performance. If the curing conditions are not met, the epoxy may not fully cure, leading to reduced mechanical strength and adhesion. Manufacturers must carefully follow the recommended curing instructions to ensure the best results.
Factors Affecting the Performance of PCB Encapsulation Epoxy
Several factors can affect the performance of PCB encapsulation epoxy. These factors include:
Type of epoxy resin and hardener: There are different types of epoxy resins available, each with its own unique properties and characteristics. The choice of epoxy resin and hardener will depend on the specific requirements of the application, such as temperature resistance, chemical resistance, and adhesion.
Mixing ratio and curing conditions: Epoxy resins typically require a specific mixing ratio of resin to hardener to achieve optimal curing. Deviating from the recommended mixing ratio can result in incomplete curing or reduced performance. Additionally, the curing conditions, such as temperature and humidity, must be carefully controlled to ensure proper curing.
Substrate material and surface preparation: The substrate material of the PCB and the surface preparation play a crucial role in the adhesion and performance of the epoxy resin. Different substrate materials may require different surface treatments, such as cleaning, sanding, or priming, to ensure proper adhesion.
Application method and equipment: The method of applying the epoxy resin can also affect its performance. Factors such as the viscosity of the epoxy, the application technique (e.g., brushing, spraying, or dipping), and the equipment used can all impact the quality and consistency of the coating.
Common Mistakes to Avoid in PCB Encapsulation Epoxy Applications
To ensure successful PCB encapsulation epoxy applications, it is important to avoid common mistakes that can compromise the performance of the epoxy resin. These mistakes include:
Inaccurate mixing ratio: As mentioned earlier, epoxy resins require a specific mixing ratio of resin to hardener for proper curing. It is crucial to carefully measure and mix the components according to the manufacturer’s instructions. Deviating from the recommended mixing ratio can result in incomplete curing or reduced performance.
Inadequate surface preparation: Proper surface preparation is essential for achieving good adhesion between the epoxy resin and the substrate material. Failing to clean, sand, or prime the surface adequately can result in poor adhesion and reduced performance. It is important to follow the recommended surface preparation procedures for the specific substrate material.
Improper curing conditions: Epoxy resins require specific curing conditions, such as temperature and humidity, to achieve optimal performance. Failing to control these conditions can result in incomplete curing or reduced mechanical strength. It is important to carefully follow the recommended curing instructions and use appropriate curing equipment if necessary.
Over-application or under-application: Applying too much or too little epoxy resin can lead to problems such as uneven coating, poor adhesion, or inadequate protection. It is important to apply the epoxy resin in the recommended thickness and ensure that it is evenly distributed across the PCB.
Troubleshooting Common Issues in PCB Encapsulation Epoxy Applications
Despite following best practices, issues can still arise in PCB encapsulation epoxy applications. Some common issues and their potential causes include:
Blistering, cracking, or delamination: These issues can be caused by inadequate surface preparation, improper mixing ratio, or improper curing conditions. Ensure that the surface is clean and properly prepared, follow the recommended mixing ratio, and control the curing conditions.
Incomplete curing or under-curing: Incomplete curing or under-curing can occur if the epoxy resin is not mixed or applied correctly, or if the curing conditions are not met. Double-check the mixing ratio and application method, and ensure that the curing conditions are properly controlled.
Poor adhesion or bonding: Poor adhesion or bonding can be caused by inadequate surface preparation, improper mixing ratio, or incompatible epoxy resin and substrate material. Ensure that the surface is properly prepared, follow the recommended mixing ratio, and choose an epoxy resin that is compatible with the substrate material.
Uneven or inconsistent coating: Uneven or inconsistent coating can be caused by improper application technique or equipment. Ensure that the epoxy resin is applied evenly and consistently across the PCB using a suitable method and equipment.
Conclusion: Overcoming Challenges and Achieving Success in PCB Encapsulation Epoxy Applications
PCB encapsulation epoxy plays a crucial role in protecting and enhancing the performance of electronic devices. By understanding the common challenges, importance, and factors affecting the performance of PCB encapsulation epoxy, manufacturers can make informed decisions and achieve successful applications.
By avoiding common mistakes, choosing the right epoxy resin, following best practices, and troubleshooting issues, manufacturers can ensure that their PCB encapsulation epoxy applications are reliable, durable, and long-lasting.
For more about the PCB encapsulation epoxy applications, you can pay a visit to Deepmaterial at https://www.adhesivesmanufacturer.com/ for more info.