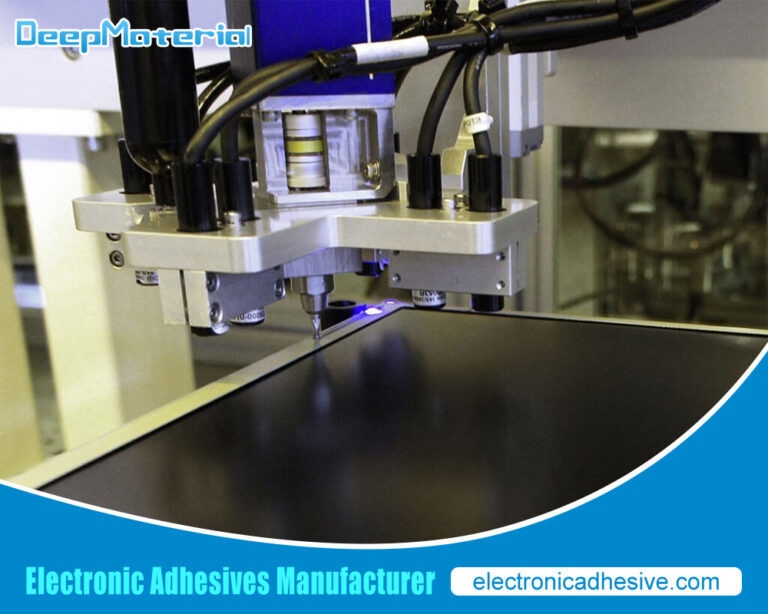
#Industry News
Exploring the Different Types of Pack Assembly Adhesives and Their Applications
Best Pack Assembly Adhesives Adhesive Glue Manufacturer
In the vast and intricate world of manufacturing, pack assembly adhesives play a pivotal role that often goes unnoticed. These unsung heroes of the assembly line ensure that our everyday products, from food packaging to electronics, are held together securely and efficiently. However, not all adhesives are created equal. There exists a diverse range of pack assembly adhesives, each with its unique properties, strengths, and applications. This blog post aims to delve into the fascinating realm of these adhesives, exploring the different types available and their specific uses in various industries.
Hot Melt Adhesives for Pack Assembly
Hot melt adhesives are widely used in the packaging industry due to their fast setting time and excellent bond strength. These adhesives are thermoplastic, meaning they are solid at room temperature but melt when heated. Hot melt adhesives are typically applied using hot melt glue guns or automated dispensing systems.
Hot melt adhesives work by melting the adhesive pellets or sticks and applying the molten adhesive onto the substrate. As the adhesive cools, it solidifies and forms a strong bond with the substrate. The fast setting time of hot melt adhesives allows for high-speed production and efficient packaging processes.
One of the advantages of hot melt adhesives is their versatility. They can bond a wide range of substrates, including paper, cardboard, plastic, and metal. Hot melt adhesives also offer excellent bond strength, which ensures that the packaging remains intact and secure throughout its journey.
Water-Based Adhesives for Pack Assembly
Water-based adhesives are environmentally friendly adhesives that use water as a carrier instead of solvents. These adhesives have low VOC emissions and are considered safer to use compared to solvent-based adhesives. Water-based adhesives are commonly used in packaging applications where a strong bond is required.
Water-based adhesives work by dispersing the adhesive particles in water and applying the adhesive onto the substrate. As the water evaporates, the adhesive particles come into contact with each other and form a strong bond with the substrate. The drying time of water-based adhesives can vary depending on the formulation and environmental conditions.
One of the advantages of water-based adhesives is their environmental friendliness. They have low VOC emissions, which means they have minimal impact on air quality. Water-based adhesives are also non-flammable and non-toxic, making them safer to use compared to solvent-based adhesives.
Solvent-Based Adhesives for Pack Assembly
Solvent-based adhesives are adhesives that use solvents as a carrier. These adhesives offer great adhesion to various substrates and have a fast drying time. Solvent-based adhesives are commonly used in packaging applications where a high bond strength is required.
Solvent-based adhesives work by dissolving the adhesive in a solvent and applying the adhesive onto the substrate. As the solvent evaporates, the adhesive forms a strong bond with the substrate. The drying time of solvent-based adhesives can vary depending on the formulation and environmental conditions.
One of the advantages of solvent-based adhesives is their excellent bond strength. They offer high initial tack and adhesion, which ensures that the packaging remains intact and secure. Solvent-based adhesives also have a fast drying time, which allows for high-speed production and efficient packaging processes.
Reactive Adhesives for Pack Assembly
Reactive adhesives are adhesives that require a chemical reaction to cure and form a bond. These adhesives offer excellent bond strength and resistance to heat, chemicals, and moisture. Reactive adhesives are commonly used in packaging applications where a high level of durability is required.
Reactive adhesives work by mixing two or more components together, such as a resin and a hardener, to initiate the curing process. The chemical reaction between the components causes the adhesive to harden and form a strong bond with the substrate. The curing time of reactive adhesives can vary depending on the formulation and environmental conditions.
One of the advantages of reactive adhesives is their excellent bond strength and durability. They offer high shear and peel strength, which ensures that the packaging remains intact and secure even under extreme conditions. Reactive adhesives also have excellent resistance to heat, chemicals, and moisture, making them suitable for applications where exposure to harsh environments is expected.
Pressure-Sensitive Adhesives for Pack Assembly
These adhesives form an instant bond when pressure is applied. These adhesives offer excellent tack and adhesion to a wide range of substrates. Pressure-sensitive adhesives are commonly used in packaging applications where ease of use and repositionability are important.
They work by using a combination of adhesive properties, such as tackiness, cohesion, and elasticity, to form a bond with the substrate. When pressure is applied, the adhesive flows into the surface irregularities of the substrate and creates a strong bond. Pressure-sensitive adhesives do not need heat or even solvent activation.
One of the advantages of these adhesives is their ease of use. They can be applied and repositioned without the need for additional tools or equipment. Pressure-sensitive adhesives also offer excellent adhesion to a wide range of substrates, including paper, cardboard, plastic, and metal.
They are commonly used in applications such as labeling, tape applications, and resealable closures. They are also used in the production of adhesive-backed products, such as stickers and decals.
However, pressure-sensitive adhesives do have some disadvantages. They can lose their tackiness over time, especially when exposed to heat or UV radiation. Pressure-sensitive adhesives also have a limited temperature resistance, which means they may not be suitable for applications where high temperatures are involved.
Final Thoughts
Pack assembly adhesives play a crucial role in the packaging industry. They provide a strong and durable bond that ensures the integrity of the packaging throughout its journey from the manufacturer to the end consumer. There are several types of pack assembly adhesives available in the market, each with its own unique properties and applications.
Hot melt adhesives offer fast setting time and excellent bond strength. Water-based adhesives are environmentally friendly and offer excellent bond strength. Solvent-based adhesives offer excellent adhesion and have a fast drying time. Reactive adhesives offer excellent bond strength and durability. Pressure-sensitive adhesives offer ease of use and repositionability.
When choosing the right pack assembly adhesive for your packaging needs, it is important to consider factors such as the substrate, application method, and environmental conditions. By selecting the right adhesive, you can ensure that your packaging remains intact and secure, resulting in customer satisfaction and financial success.
For more about choosing the Different Types of Pack Assembly Adhesives and Their Applications, you can pay a visit to DeepMaterial at https://www.electronicadhesive.com/about/ for more info.