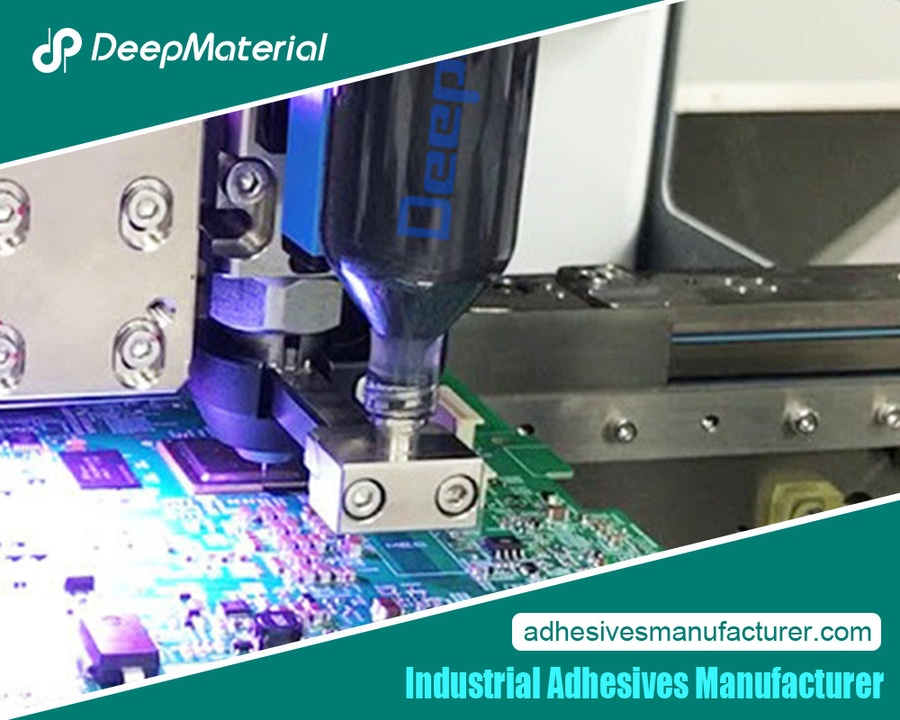
#Industry News
Finding the Perfect Fit: Choosing the Best UV Glue for Glass Bonding
Best UV Adhesive Glue for Glass Bonding Manufacturer
UV (Ultraviolet) glue holds a paramount role in glass bonding, offering a unique and indispensable solution in various industries. It enables the secure and precise adhesion of glass components in applications ranging from electronics and automotive to medical devices and architectural design.
Selecting the appropriate UV glue for glass bonding is a critical decision, as it directly impacts the performance, durability, and longevity of bonded glass structures. The right choice ensures not only strong and reliable bonds but also the optimal balance of properties to withstand diverse environmental conditions and industry-specific demands. This article delves into the intricacies of making this essential selection.
Factors to Consider When Choosing UV Glue
Glass Type and Surface Preparation – The type of glass being bonded, whether it’s soda-lime, borosilicate, tempered, or specialty glass, influences adhesive compatibility. Surface preparation, including cleaning and roughening, is crucial to ensure proper adhesion. Different glass types may require specific surface treatments.
Bonding Environment and Conditions – The environment where bonding takes place matters. Consider factors like temperature, humidity, and exposure to chemicals or UV radiation. Indoor and outdoor applications may have different adhesive requirements, necessitating UV glues with varying levels of environmental resistance.
Strength and Durability Requirements – Assess the load-bearing capacity, mechanical stresses, and long-term performance expectations of the bonded glass components. High-stress applications may require UV glues with enhanced strength and durability properties.
UV Light Source and Curing Process – The choice of UV light source (e.g., UV LED, mercury vapor lamp) and curing process (spot, flood, or conveyor curing) directly impacts adhesive curing time and effectiveness. Ensure that the UV glue selected matches the specifications of the UV light source and curing process used in your manufacturing or bonding process.
Types of UV Glue for Glass Bonding
UV-Curable Liquid Adhesives – UV-curable liquid adhesives are versatile and widely used for glass bonding. They offer excellent flow and wetting properties, ensuring complete coverage of glass surfaces. Liquid adhesives are suitable for applications where precise control over adhesive placement is required, such as bonding glass components with intricate geometries.
UV-Curable Gels and Pastes – UV-curable gels and pastes have higher viscosity compared to liquid adhesives, making them ideal for vertical or overhead bonding applications. They offer better gap-filling capabilities and are commonly used in structural bonding where gap tolerance is a consideration.
UV-Curable Tapes and Films – UV-curable tapes and films are pre-coated with UV adhesive and are often used for bonding glass to glass or glass to other materials. They provide convenience and uniform adhesive thickness, making them suitable for large-scale manufacturing and automated assembly processes.
Specialty UV Adhesives – Specialty UV adhesives are formulated to meet specific industry or application requirements. Examples include optically clear adhesives (OCA) for display assembly and flexible UV adhesives for bonding flexible substrates. These adhesives are designed to address unique challenges and performance criteria in specialized glass bonding applications.
How to Apply UV Glue for Glass Bonding
Surface Preparation and Cleaning – Begin with thorough glass surface cleaning to remove contaminants like dirt, grease, and oils. Properly cleaned surfaces ensure strong adhesive bonds. Depending on the adhesive and glass type, additional surface treatments like UV ozone cleaning or plasma treatment may be necessary for optimal adhesion.
Proper Dispensing and Application Techniques – Use precision dispensing equipment to apply the UV glue evenly on the glass surfaces. Ensure that the adhesive layer is uniform without gaps or excess material. Pay attention to the adhesive quantity, as too much or too little adhesive can affect bond strength and appearance.
Curing and Quality Control – After adhesive application, bring the glass components together in the desired configuration. Expose the adhesive to the appropriate UV light source for the specified duration. Monitor the curing process to ensure complete and uniform curing. Implement quality control measures to inspect the bonded glass for defects or incomplete curing. This may involve visual inspection, adhesion testing, and performance evaluations.
Following these steps meticulously is essential to achieve strong and reliable bonds when using UV glue for glass bonding. Proper surface preparation, precise application, and thorough curing ensure the integrity of the bonded glass components.
Best Practices and Tips for Successful Glass Bonding
Storage and Handling of UV Glue – Store UV glue in a cool, dark place to prevent premature curing due to exposure to UV light or elevated temperatures. Keep containers tightly sealed to prevent moisture ingress, which can affect adhesive performance. Follow the manufacturer’s recommendations for shelf life and storage conditions.
Safety Precautions During the Bonding Process – Wear appropriate personal protective equipment (PPE), including safety glasses and gloves, when handling UV glue. Ensure adequate ventilation in the workspace to dissipate any fumes or vapors that may be released during curing. Follow safety data sheet (SDS) guidelines provided by the adhesive manufacturer for safe handling, disposal, and emergency procedures.
Maintenance and Long-Term Care – Periodically inspect bonded glass components for signs of degradation, such as discoloration, cracking, or loss of adhesion. Implement a maintenance schedule to address any issues promptly, which may involve re-bonding or reapplication of UV glue as needed.
Consider environmental factors and exposure conditions that could impact the long-term performance of bonded glass, and plan for maintenance and repairs accordingly. Adhering to these best practices and safety measures not only ensures successful glass bonding but also contributes to the longevity and reliability of bonded glass structures. Proper handling, storage, and ongoing maintenance are essential for optimal results.
Final Words
The selection and application of UV glue for glass bonding demand careful consideration and adherence to best practices. UV glue plays a pivotal role in various industries, offering strong, efficient, and durable bonding solutions. From proper surface preparation to meticulous curing and vigilant long-term maintenance, every step is critical to achieving successful and reliable glass bonds. Ensuring the safety of personnel during the bonding process and complying with storage and handling guidelines are paramount.
For more about the best UV glue for glass bonding, you can pay a visit to Deepmaterial at https://www.adhesivesmanufacturer.com/ for more info.