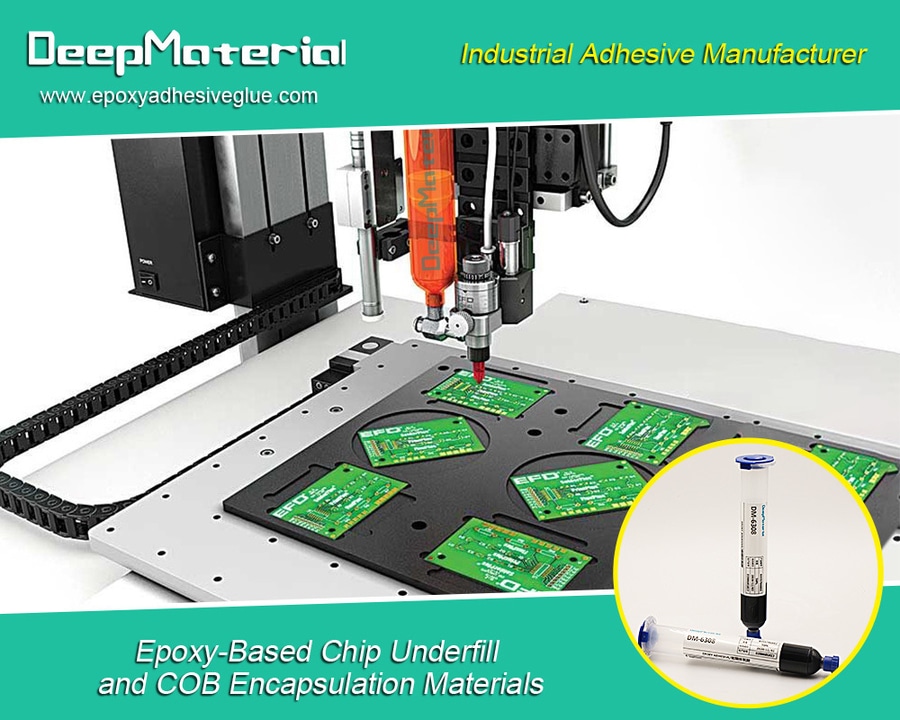
#Industry News
Can A LED Potting Compound Supplier Provide Custom Formulations?
Best LED Potting Compound Adhesive Glue Manufacturer
LED potting compounds are the go-to choice when it comes to safeguarding LED components. Total insulation? They tick the right boxes. Temperature control? Yes, of course. Overall environmental protection? These dependable materials come in various forms – liquid, gel, and solid – mostly comprised of epoxy or silicone, depending on the application they’re needed for.
For a high-temperature setup, an epoxy-based compound is a way to go due to its trustworthy electrical properties and impressive adhesive strength. In contrast, if flexibility with exposure to extreme elements such as moisture and chemicals were required, then a polymer like silicone would suffice.
Industrial Hot Melt Electronic Component Epoxy Adhesive And Sealants Glue manufacturers
Understanding the need for custom formulations
Standard LED potting compounds can indeed get the job done in many cases – but these solutions often leave something to be desired. If requirements and conditions are out of the ordinary, then you really need a tailored solution. That’s why custom formulations offer a better way to beat those liminal limitations and overcome what regular old solutions can’t do.
Take heat dissipation, for instance – this is mega important with high-power LEDs: if your hot little components don’t stay calm, their lifespan will take a hit! With customized formulas, we can dial up the thermal conductivity so it overachieves on cooling performance – now that might save your bacon!
And let’s not forget about UV or chemical exposure either; if they make contact with your LEDs, too much sunshine could be your undoing… Custom-formulated materials help protect them from such environmental threats, allowing reliable operation far into the future.
Benefits of custom LED potting compounds
Custom LED potting compounds offer several benefits over standard formulations:
Using specifically tailored LED potting compounds can drastically improve not only the performance but also the reliability of LEDs.
This custom approach offers greater thermal control to avoid running hot and risking compromised performance or lifespan, as well as superior protection from environmental perils like UV radiation, moisture, and chemicals.
Although there may be added cost upfront for a specialty blend over standard formulations, this investment pays off in improved efficiency that translates into long-term savings since service calls and switching out parts due to aging should diminish. All around, it’s a win.
How to communicate your requirements to the supplier
To effectively communicate your requirements to the supplier for custom LED potting compounds, follow these steps:
Define the application and operating conditions
What do we need to know about your application? Let us in on the range of operating temperatures, any possible environmental factors that could impact it and what you would like performance-wise. Lay out all relevant details so there’s no confusion! It will help us make sure this LED potting compound is suited up for duty.
Identify the desired properties and characteristics
It’s essential to outline clearly what you’d like in the custom formulation. Think of things like thermal conductivity, insulation properties, bendiness, how well it’ll stick together and resistance to heat or other environmental stuff. Don’t forget any key ingredients that could make or break the formula.
Provide samples and testing data
If possible, throw us a few samples of the LED components or prototypes you want to encase with your custom formulation. That’ll help the supplier out majorly – they’d get a better grasp of what your unique needs are – and be able to cook up an appropriate solution. Plus, give them any test data or performance requirements particular to this application as well.
The role of the supplier in developing custom formulations
The supplier plays a crucial role in developing custom LED potting compounds:
Formulation design and optimization
Meeting the customer requirements is our top priority, so we’ll pull out all the stops and customize a formulation that checks all their boxes. That means carefully selecting and blending key ingredients while running tests to make sure we hit the mark. It’s more art than science- but rest assured, we’ve got it covered.
Prototype development and testing
After the design is completed, the supplier cooks up a few prototypes to put through their paces. Time for testing – these things are about to get put through the wringer to assess their performance and dependability in various scenarios. No stone is left unturned here.
Scale-up and production
Well, that prototype testing went super smooth! Now, it’s time to ramp up production and make sure we can meet the customer’s needs. Quality control is a priority so nothing slips through the cracks, and then we have to tweak those production processes for maximum efficiency.
Testing and validation of custom LED potting compounds
Testing and validation are crucial steps in ensuring the performance and reliability of custom LED potting compounds:
Standard testing procedures
Standard tests must be performed on custom formulations to judge their electrical insulation, thermal conductivity, sticking force, suppleness, and resiliency toward external factors. We’re referring here to dielectric strength testing, thermal conduction analysis, peel measure trials and environmental experimentation. All of this is of great importance in making sure the final product meets high set standards.
Customized testing based on application requirements
On top of the norm, depending on how it’s going to be used, custom mixes might need some serious tailored testing. We’re talking accelerated aging assessments, UV light checks, chemical-resistant trials and mechanical tension tests – a lot more than your regular run-of-the-mill exams!
Validation through field trials and customer feedback
After the custom formulation passes its paces, it’s time to crack the whip and make sure everything checks out in the real world. We install our precious LED components, encapsulated with this new formulation into actual applications and see what kind of feedback we can get from customers.
If any of these field trials are duds or raise red flags, then we have to go back to the supplier and have them resolve any issues that pop up so that our customer expectations are met – no matter what.
Quality control measures for custom formulations
When it comes to making sure a product like LED potting compound is reliable and consistent, suppliers need stringent quality checks.
Of course, manufacturers should select only the most up-to-date raw materials that satisfy specs and expectations.
These have to be put through their paces, too – then there’s in-process testing throughout manufacture to make sure stuff like viscosity, curing timeframe, etc., is bang on before sending off with certification attesting its reliability.
Conclusion and final thoughts
Making the right decision on who to source custom LED potting compounds from is essential. Formulating it according to how your needs require guarantees you won’t run into any issues with performance and reliability and helps keep down costs, too. Your options for tinkering with standard LED compounds are vastly expanded, giving way to improved performance, heat control, and adequate protection against elements of all kinds.
For now, we’ve yet to witness the full potential that custom LED potting compounds can dole out – like higher UV proofing or increased thermal transmission – but as demand continues to swell in popularity for these ultra-high capacity LEDs, they’ll become even more critical. They so will snag the correct supplier that knows both their business and formulating inside out.
For more about choosing the best LED potting compound supplier, you can pay a visit to DeepMaterial at https://www.epoxyadhesiveglue.com/category/epoxy-adhesives-glue/ for more info.