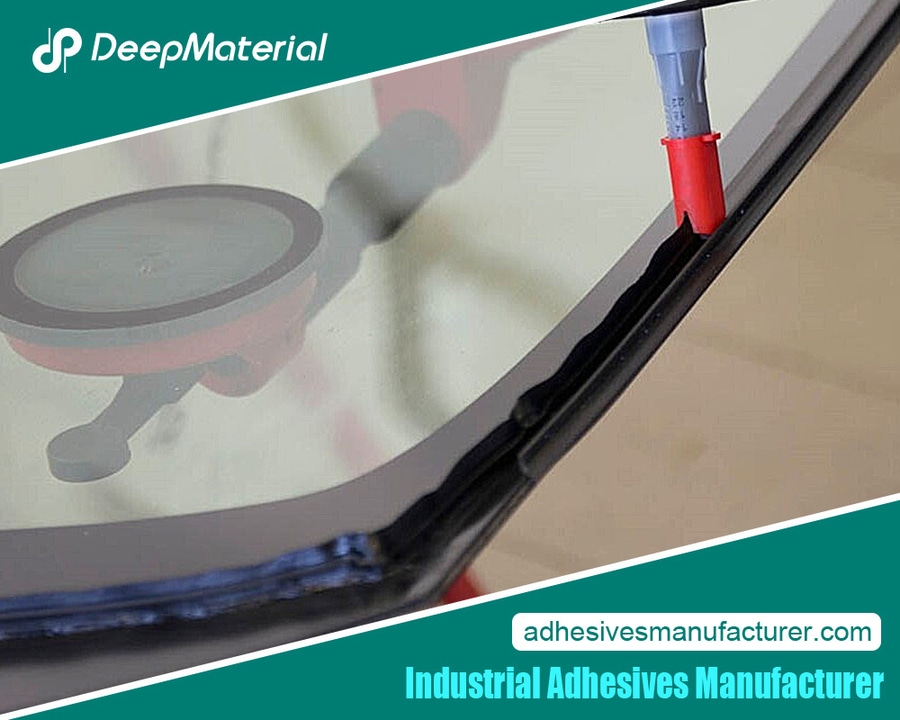
#Industry News
What Is Nonconductive Coating for Electronics
Best Nonconductive Coating Adhesive Glue for Electronics Manufacturer
Nonconductive coatings create a kind of shield to protect delicate components from intense heat or hazardous electricity, offering a great wall of resistance between the metal surface and whatever else it could come in contact with.
These protective coatings can be applied to both ferrous and non-ferrous metals – all while making sure temperatures stay low or electrical currents don’t reach levels that are out of control. A real savior when eked out for applications that involve either high temps or serious charges! In this article, we talk about the impact of nonconductive coating on electronic components.
Nonconductive Coatings Applications
Choosing a nonconductive coating (NCC) depends on the project’s particulars; thermal spraying and plasma spraying are common go-tos, each with its pros and cons. Your substrate material, the desired properties of the coating and any working conditions will determine which is best for you — an impossible decision to make without taking all those factors into account!
Benefits of Nonconductive Coatings Applications
Preventing Short-Circuits – Nonconductive coatings are a real boon when it comes to keeping the electricity where it should be – in the right place and nowhere else. This means no short circuits, ensuring that all your electronic components will work like clockwork – not a surprise failure in sight!
Dielectric Properties – Nonconductive coatings show off immense dielectric strength – which is key when it comes to withstanding electrical overload and preserving insulation, even under extreme voltage conditions. You’ve got to have fortitude in order to protect particular components from damage!
Moisture Resistance – Nonconductive coatings provide an effective bulwark against moisture, barring the entrance of water and shielding electronic parts from decay and destruction. With this extra layer of protection, our precious electronics can remain in tip-top condition – far away from the ravages of time and weather.
Chemical Resistance – Shielding components from the hostile forces of corrosive substances, these coatings provide resistance to a variety of harsh chemicals in rugged surroundings. By forming this protective barrier, they allow vital equipment to turn a blind eye to some of nature’s most treacherous elements.
Temperature Stability – Nonconductive coatings provide thermal insulation, shielding electronic components from unnatural highs and lows of temperature so they don’t suffer any heat-related wear and tear. This fortification goes a long way in ensuring optimal performance.
Mechanical Protection – Nonconductive coatings are your guardian angels, keeping you safe from unexpected shocks and vibrations. Especially when it comes to applications involving electronic components constantly on the go – think outer space shuttles and more – all that jostling could easily leave them damaged beyond repair if not for those trusty guard dogs of protection.
Suitable for Various Surfaces – The grip between these nonconductive coatings and anything you could think of – from metal to plastic, even circuit board materials – is unbelievable; it reinforces such a strong bond that you could rely on it any day. From the iron fist clinch, they create with just about anything, it’s clear these layers are here to stay!
Conformal Coating Abilities – These nonconductive coatings can bend and adapt to the contours of even the trickiest surfaces, meaning they’re total lifesavers when it comes to complexly shaped and super delicate electronic components. Talk about hitting two birds with one stone; it’s a beautiful thing!
Visual Clarity – When you need to check things visually, special coatings are made so your vision doesn’t get hazy. This is especially handy for sensor and display tasks – no blurring allowed! So, the “sight” stays clear-cut, and nonconductive finishes work their magic in all the right places.
Straightforward Application – Liquid nonconductive coatings make the application process smooth and precise, making sure even tiny details get covered properly. You have to look at every angle to ensure it’s plain sailing with a perfect uniform coverage.
According to Standard – With protective coatings that meet the necessary regulations, components remain reliable and compliant. It’s a critical piece of the puzzle to make sure you’re not putting lives at risk or sacrificing efficacy. You want to be certain that your coating makes sure everything – from performance to safety – is in tip-top shape.
Designed to Meet Specific Needs – Manufacturers are able to tailor nonconductive coatings precisely to their desired performance properties, be they maximum flexibility, superior hardness, or enhanced thermal conductivity. With such precise customization available, what these coatings can deliver is truly extraordinary!
Nonconductive coatings are irreplaceable, bolstering the reliability, longevity, and safety of electronic/electric parts used in multiple fields. Without a doubt, their inclusion is essential for almost any industrial undertaking out there. That is why nonconductive coatings have become too popular in the electronics manufacturing and assembly industry.
Any Difference Between Nonconductive Coating and Conductive Coating?
Nonconductive and conductive coatings have two distinct functions: one to insulate electrical components from factors like short circuits and environmental elements, and the other to help control electrical flow for grounding, static dissipation, and EMI shielding.
The critical separation between these two lies in their properties – non-conductives offer a protective shield. At the same time, conductives enable useful conduction fit for specific needs of industries like telecommunications, aerospace and electronics.
To put it metaphorically, one is an armor that blocks out current, while the other is a bridge that allows electricity flow according to the desired purpose. Both are essential items on any electronic device’s checklist as they both serve critical purposes, with neither being superfluous or interchangeable!
Final Thoughts
Nonconductive coatings for electronics are a must in this day and age – they provide insulation to shield electronic components from environmental hazards, reinforce longevity, and boost the reliability of these devices. Widespread across industries such as consumer products, cars, and aeronautics, such coatings nip electrical mishaps in the bud, preventing short circuits while protecting against any harm that hastens aging or destroys functionality. In truth, their role is essential–underlining just how vital they are for making sure that your electronics stay put and run optimally amidst varied applications.
For more about a complete guide to the Nonconductive Coating for Electronics, you can pay a visit to Deepmaterial at https://www.adhesivesmanufacturer.com/ for more info.