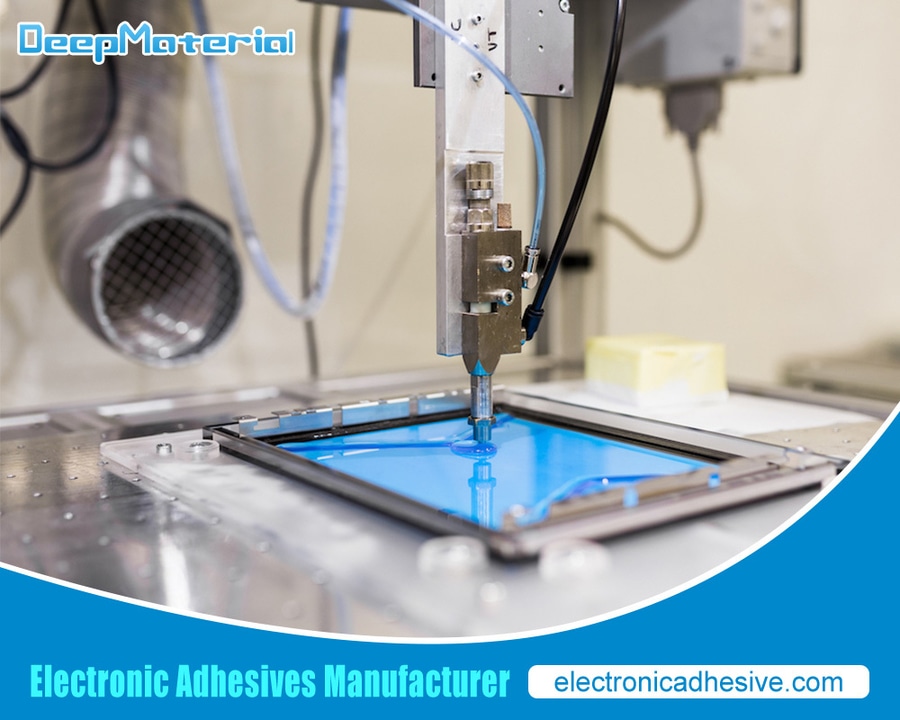
#Industry News
What Is Non-Conductive Coating For Electronics, And Why Is It Important?
Best Non-Conductive Coating Adhesive Glue For Electronic Manufacturer
Non-conductive coatings are a vital part of electronics and play a significant role in protecting components. This added layer works to shield from electrical interruptions, short circuits, and more while extending the life expectancy of devices – promoting smooth operation at its finest.
Let’s delve into conductivity in the electronic world: the importance of non-conductive solutions, types available, advantages they bring with them for use, factors to consider when deciding what coating is right for you, proper ways to apply them, popular applications & how they fit into our plans nowadays as well as where things might be going down the road.
The concept of conductivity in electronics
Conductivity is essentially the system behind how electric current flows through materials – it’s what makes electronic devices perform and function as they’re supposed to. It’s a critical part of electronics because conductive materials allow electricity to flow freely, while non-conductive ones hinder or stop their movement completely. For that reason, with components and circuits especially, controlling conductivity is key for ensuring optimum operation and avoiding electrical interference or any unsafe short-circuiting.
The importance of non-conductive coating in electronics
Nothing’s worse than damaged electronics due to electrical interference or short circuits. That’s why non-conductive coatings are essential: they act as insulators, shielding electric gadgets from harmful currents and forming a crucial barrier between conductive materials.
Providing such protection gives electronic devices the assurance of stability and functionality – plus an extra layer of toughness against moisture, dust, or chemicals that threaten their extended use.
Types of non-conductive coatings for electronics
There are several types of non-conductive coatings available for use in electronics:
Polymer coatings
Polymer-based coatings are the go-to for electronics; they’ve got excellent insulation and are really easy to apply. What’s more? It can be done any which way – whether you spray, dip, or brush it on – no hassle at all! These coatings provide an extra safeguard against potential interference or short circuits landing you in a world of trouble.
Ceramic coatings
Ceramic coatings are renowned for their insulation capabilities, both thermally and electrically. In fact, they’re usually put to use in highly heated locations when other coatings just don’t cut it. Nowadays, these coatings can be applied with plasma spraying or chemical vapor deposition tactics – two pretty amazing methods.
Epoxy coatings
Epoxy-based coatings are the go-to in electronics because of their super glue-type adhesion plus unrivaled defense against chemicals. This layer of protection makes sure electrical interference and short-circuits stay away – you can apply it by spraying, dipping, or brushing on. These coatings sure come in handy.
Parylene coatings
Parylene coatings are like no other, set apart by their one-of-a-kind vapor installation. Fashioned into a thin film when solidified, they deliver fantabulous protection from dampness, toxins, and electrical meddling – so much so that it’s become common in medical mechanisms and the aerospace industry.
Advantages of using non-conductive coatings in electronics
The benefits of employing non-conductive coatings in electronics are manifold.
Protection against environmental factors
Simply put, these coatings provide an extra layer of protection against a range of environmental elements – from moisture and dust to more toxic substances – mitigating the risk of electrical interference and short circuits, all of which can damage or degrade system performance.
Improved safety
Their sturdy barriers offer heightened levels of user safety, too!
Enhanced performance
Unsurprisingly, then, non-conductive coatings remain a stalwart in ensuring optimal operation across electronic devices.
Factors to consider when choosing a non-conductive coating
Picking the proper non-conductive protection for your electronics can be a tricky thing to do. There are a few key points you need to consider before making any decision:
Compatibility with electronic components
First of all, it’s essential that the coating is compatible with whatever components or materials it will be covering. This ensures a reliable and solid connection as well as its long-lasting performance.
Application method
Plus, make sure you pick an application method – spraying, dipping, brushing, and so on – that is suitable for the actual parts being covered while at the same time guaranteeing the desired thickness.
Cost-effectiveness
And finally – don’t forget about costs! Try finding a sweet spot between cost efficiency and your desired outcome in terms of functionality and reliability.
How to apply a non-conductive coating to electronics
The application of non-conductive coatings to electronics involves several steps:
Surface Preparation
Before one can give electronics the non-conductive coating they desire, they must make sure that the surface of the gear is squeaky clean. This could mean eliminating any residues or grime from them and even sculpting a curvy landscape on them with an abrasive before adding a primer if needed.
Application techniques
Then comes the time to apply said protective layer using several means such as spraying, dipping into it like butter in a hot pan, or literally just brushing it on there like one would do painting an old dresser. It really depends on how thick you want this bedding and what suits your endeavor best.
Curing process
Finally, after doing all that fiasco, remember to do all your hard work according to instructions handed by the ones who supplied you with the material! That could go from leaving it exposed to solar radiation to Soothing heat for some length of time -or- giving it a chemical bath if required by circumstance.
Typical applications of non-conductive coatings in electronics
Non-conductive coatings find a wide range of applications in the electronics industry:
Protecting vital components with their non-conductive coatings, Printed Circuit Boards (PCBs), sensors, and medical devices are all insulated from the risks of environmental factors like humidity, dust, and interference.
Thus, these coverings ensure that PCBs remain reliable, sensors maintain their accuracy, and medical devices can operate safely – without being compromised.
In the aerospace and defense world especially, this level of insulation is essential for them to perform optimally on mission-critical equipment over time.
Last Words
Non-conductive coatings loom large in the realm of improving performance and safety when it comes to electronics. Everything from preventing short circuits and protecting against electrical interference to enhancing durability hinges on selecting a suitable coating that is applied properly. The terrain in this area is constantly changing, with new materials and application techniques emerging all the time. It’s not surprising then that demand for enhanced electronic devices coupled with increased safety means non-conductive coatings are only being tapped more going forward.
For more about choosing the Top Non-Conductive Coating For Electronics, you can pay a visit to DeepMaterial at https://www.electronicadhesive.com/about/ for more info.