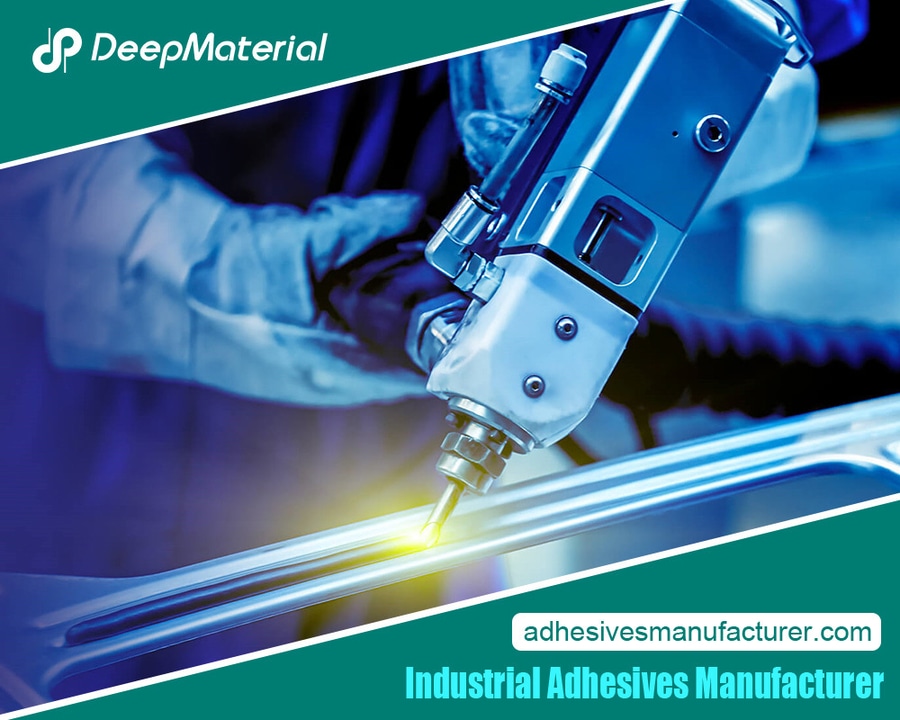
#Industry News
What types of industrial adhesive solutions are used in
Best industrial Adhesive Glue Manufacturer
When it comes to industrial adhesive solutions, you can find plenty of options for adhesive solutions formulated for varying applications. The adhesive solutions are formulated depending on the specific requirements and usage. For instance, there are various formulations available in the market keeping in mind the durability, chemical resistance, thermal resistance, and bonding strength. You can choose the solution that matches your specifications depending on the industry and usage.
Wondering what types of industrial adhesive solutions are available for you to use in your industrial applications? Well, do not feel overwhelmed because in this article I am going to mention all the commonly formulated and available adhesives. You can find the specific formulation and specialty of all these adhesives and choose which one is the best fit as per your requirements.
Types of adhesive solutions
Here are the common types of adhesive solutions that you can use for industrial applications.
Epoxy Adhesives: The adhesives that are formulated with epoxy resins and a curing agent (or hardener) are known for their durability, chemical resistance, temperature resistance, and high bonding strength. These are the most versatile types of adhesives because they can be composed in various formulations by changing the ratio of epoxy resins and hardeners and by adding an additive agent. They are strong adhesives that can bond with various surfaces by chemicals developing a strong bond on the surface level. They can create bonds with composites, metals, and other type of materials. They are widely used in various industries including automotive, construction, aerospace, electronics, and marine.
Polyurethane Adhesives: Polyurethane adhesives are known for their flexibility, high strength, and weather resistance. These adhesives can develop a strong bond with different types of substrates and varying coefficients of thermal expansion. These types of adhesives are strong enough to bear harsh environmental factors and still offer strong adhesion. They are commonly used in the construction industry, woodworking, and automotive assembly.
Acrylic Adhesives: Acrylic adhesives are famous for their durability, high bond strength, flexibility, quick cure time, and exceptional resistance to extreme temperatures. They can be bonded with various types of substrates including glass, metal, and plastics. These adhesives are widely used in structural applications and outdoor applications owing to their exceptional resistance to UV radiations. Acrylic adhesives are commonly used in automotive, electronics, and other such industries where the bonding structure is kept outdoors.
Cyanoacrylate Adhesives: If you need instant bonding then cyanoacrylate adhesives are the best option for you. In fact, these adhesives are also famous with the name instant adhesives and super glue. This is because they have exceptionally high cure time and offer quick bonding with surface materials of varying types including metals, ceramics, plastics, and even rubber. They instantly form adhesion when they come in contact with moisture. The adhesion they offer is of high strength and rigid. Their quick assembly makes these desirable when users need an instant bonding solution. This is why they are deemed ideal for medical devices, automotive repair, and the electronics industry.
Structural Adhesives: As the name suggests, these adhesives are ideal for structural applications where a high-strength bond is required for load-bearing components. These adhesives offer high resistance to harsh environmental factors, are durable, and have high strength. Their bonds are strong enough to bear high mechanical stress and rapid variations in temperature. Structural adhesives found their application in multiple industries including automotive, construction, and aerospace. Offer exceptional bonds for engineered plastics and composites.
Hot Melt Adhesives: As the name implies, these adhesives are melted and then applied hot when in the liquid state. These adhesives are made with thermoplastic materials. These adhesives are used for bonding when they are in a liquid state but as they cool down they naturally solidify creating a strong rigid bond with the surface. They can be bonded with various substrates including cardboard, wood, plastics, and even paper. These adhesives are normally used in paper assembly, packaging, and woodwork. Hot melt adhesives are known for their speedy bonding and fast processing speed.
Pressure-sensitive adhesives: Pressure-sensitive adhesives or PSA create a bond with the surface with a light pressure. They do not need any solvent activation, heating, cooling, or moisture. They are also known as self-adhesive or self-stick adhesives due to their bonding quality. These adhesives immediately form bonds and have a quick cure time as they offer a combination of viscosity and elasticity. They are widely used in tapes, graphic films, and labels.
Silicone Adhesives: Silicone adhesives are known for high resistance towards temperature change, great flexibility, weather resistance, and exceptional sealing qualities. They can be bonded with various substrates including glass, metals, and plastics. They are commonly used in construction, electronics, automotive, and medical industries. It might sound surprising but they are also widely used in plumbing owing to their exceptional sealing feature.
Specialty adhesives: these adhesives are formulated for specialized applications. For instance, they can be formulated for healthcare products with special regard to medical-grade adhesion. Similarly, for extreme environments, the adhesives are formulated that can withstand high-temperature shifts, and for electronics, the conductive adhesives are formulated specially. Since these adhesives are designed for the purpose at hand, this is why they are called specialty adhesives.
UV curing adhesives: These are the adhesives that work on UV radiation or other sources of radiation to form the bond. They basically follow the principle of radiation curing and offer a permanent bond with the substrate. These adhesives don’t require heating, moisture or other reactions and merely initiate the bonding with UV lights which offer quick and instant bonding.
Conclusion:
There are numerous industrial adhesive solutions available in the market for industrial applications. To choose the right adhesive, you need to list down basic factors such as the industry you need the adhesion for, he material you are using, and any environmental, chemical, or thermal factors related to the adhesion. By listing down these factors, you can shortlist the available adhesives and find the one that matches your requirements and offers the result you are looking for.
For more about a complete guide to industrial adhesive solutions, you can pay a visit to Deepmaterial at https://www.adhesivesmanufacturer.com/ for more info.