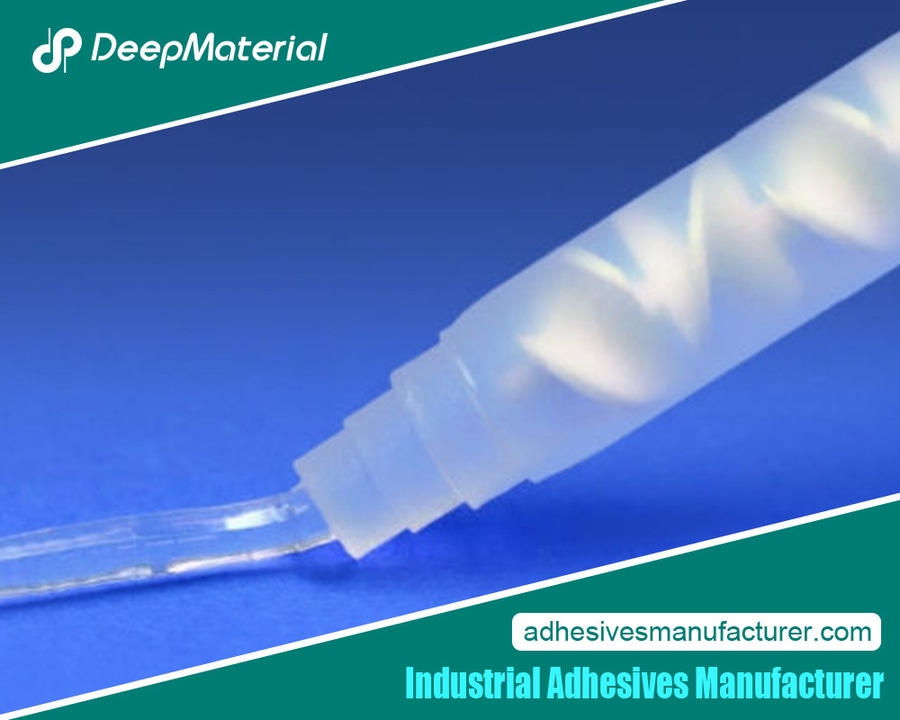
#Industry News
Why do we need nonconductive coatings?
Best nonconductive coatings Adhesive Glue Manufacturer
Electricity is the backbone of every industry these days. No industry can operate without a continuous supply of electricity. Electricity surely offers unparalleled benefits to various industries but it also comes with an inherent risk. Electric insulation is desired in various industries such as aerospace and manufacturing to insulate the equipment against electric currents. This indispensable need requires the usage of non-conductive coatings to offer the needed protection and ensure the longevity and efficiency of the electronic systems you are dealing with.
That is just the tip of the iceberg, non-conductive coatings are used for many other benefits that they offer. You must be interested to find out in detail the need for using non-conductive coatings. Well, in this article you can find out all the reasons to need non-conductive coatings in any industry. But before we delve into the need, we will start by introducing what non-conductive coatings are.
Non-conductive coatings: Non-conductive coatings, as the name suggests, are coatings that do not let the heat or electricity pass through. These are specially designed coatings that restrict the electricity and heat passing through the metal surfaces.
These coatings are also known as insulation coating, dielectric coating, or insulating coating. These coatings protect the electrical units or equipment from malfunctions or short circuits. If these coatings are not in place then the electric failures can lead to catastrophic disasters.
Most of the non-conductive coatings are made with organic substances which makes them the ideal material as these are naturally free from zinc, copper, and nickel.
The most used non-conductive coatings are made from polymers, epoxies, polyurethanes, and ceramics.
Need for non-conductive coatings:
Here are the reasons why we need non-conductive coatings in industries.
Safety measure: Safety is the first and foremost priority no matter which industry you deal in. This is the reason that you need non-conductive coatings to protect your electric equipment. The responsibility to employ protective measures is of paramount importance if the electrical equipment is operational in an area where humans work alongside. When humans interact with sensitive electric equipment then the insulation becomes even more necessary. Non-conductive works as a protective layer that diminishes the risk of short circuits and electric shocks. Some major industries rely on these coatings for protection including automotive, construction, and consumer electronics. These industries benefit from these coatings to maintain their safety standards and protect their machinery, labor, and facility from probable accidents.
Avoid chances of electric leakage: Electric leakage is a major concern in many industries. A minor leakage can compromise the reliability and performance of electrical equipment. To protect the electrical devices against possible electric leakage you need to apply non-conductive coatings. They can also work to preserve the electric circuits from damage and lower the chances of device malfunction. These coatings largely minimize the risks of voltage fluctuations, and short circuits that can destroy the machinery of your devices. This not only protects your devices from harmful impacts but also increases the useful life of the electric devices or equipment.
Resistance against corrosion: Electrical equipment is often placed in an environment where it is exposed to chemicals, moisture, and thermal variations. All these environmental factors can lead to corrosion. Non-conductive coatings can save your electrical equipment and their components from degradation by corrosion. Corrosion can affect the functionality of electrical equipment and also affect its structural integrity. These coatings create a barrier or layer that doesn’t let the environment interact with the substrate aiding in protecting it against any chance of corrosion. Resistance against corrosion not only saves the equipment from harmful environmental effects but also enhances mechanical efficiency, enhance longevity, and lowers maintenance costs.
Thermal insulation: when exposed to temperature variations, electrical equipment can get overheated. This overheating can affect the functionality of the equipment and can even lead to component degradation, component failure, short-circuit, and even faulty equipment. This not only becomes a stress for you but also needs high maintenance and in some cases replacement costs that can disrupt your budget. This is why you need to use non-conductive coatings to get the required thermal insulation that helps to dissipate heat and ensures that your equipment works perfectly. By keeping away the heat from sensitive electrical components, you can enhance the performance. The equipment and components become reliable when they are treated for thermal insulation. These features make these coatings ideal for high-power applications like LED lighting and power electronics.
Facilitate innovative miniaturization: Technological innovations are improving the design and quality of electrical equipment while minimizing its size to fit in your hands and pockets easily. Miniaturization is one such trend that is getting recognition among innovation lovers. For miniaturization, you have to put critical components in a closely knitted network which increases the chances of electric conduction that can disrupt the entire electric flow. This is why you need to use non-conductive coatings in such equipment to keep the design compact and minimal. This helps you to densely pack sensitive electric components without compromising on performance. These coatings help cutting-edge technologists design their structures without any risk of electric conduction. These coatings are widely installed in IoT sensors, wearable gadgets, and medical implants.
Improve dielectric strength: The electric devices can break down by facing electric stress. Non-conductive coatings have great dielectric strength which keeps the electric equipment intact and saves it from breaking down even when exposed to electric stress. This is why you need to apply non-conductive coatings on the electrical equipment when the chances of electric stress are higher. By applying these coatings, you can improve the dielectric strength of electrical equipment and ensure that it functions even at high voltage without any chance of breakdown or component failure.
Compliance with regulatory standards: Almost all industries have some regulatory policies and standards that the operating companies have to follow. To ensure reliability and safety, many industries that deal with sensitive electric equipment have made it mandatory to use non-conductive coatings owing to the benefits they offer. This is why you need to apply these coatings to conform to the regulatory standards.
For more about a complete guide to the nonconductive coatings, you can pay a visit to Deepmaterial at https://www.adhesivesmanufacturer.com/ for more info.