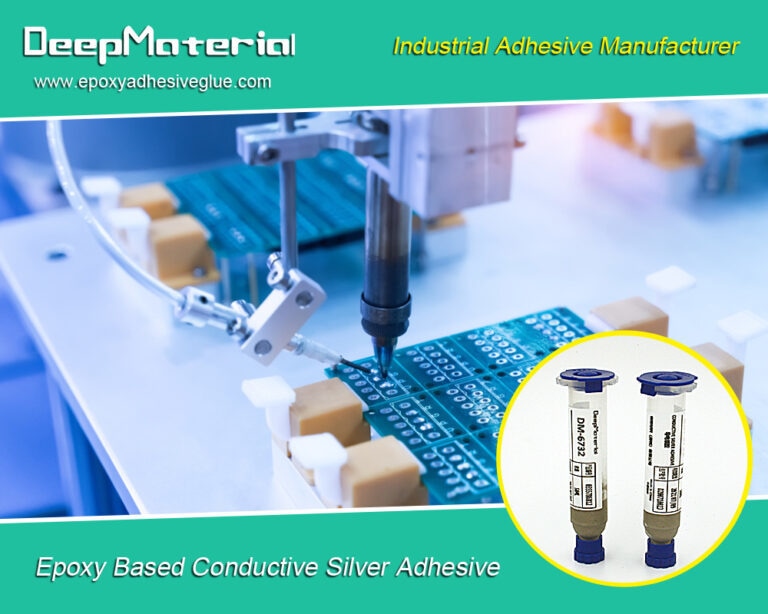
#Industry News
Troubleshooting Common Issues with UV Cure Adhesive Glue For Polypropylene
Best UV Cure Adhesive Glue For Polypropylene Manufacturer
UV-cure glue is a top pick for quick-setting applications and forming strong bonds, especially with tricky materials like polypropylene. Yet, even the best glues can run into trouble, affecting how well they work. Let’s dive into some common issues like poor curing, adhesion failures, and environmental resistance when using UV cure adhesive on polypropylene surfaces, and how to fix them.
Issue 1: Poor Adhesion
A frequent hiccup when using UV-cure adhesive with polypropylene is poor adhesion. This can stem from a few places:
One major culprit is surface contamination. Polypropylene can often harbor oils, greases, or other slick agents that mess with the glue’s ability to stick. Make sure to clean and degrease the surfaces thoroughly before you start gluing. Also, prepping the surface correctly is key—roughening it up or applying a primer can make a big difference in bond strength.
Choosing the wrong adhesive can also lead to headaches. Not all UV cure adhesives are cut out for polypropylene. Pick one that’s specially made for it, often enhanced with additives that help the glue spread and stick better.
For better adhesion, consider surface activation techniques like corona or flame treatment to bump up the surface energy, or plasma treatment to tweak the surface chemistry and improve stickiness.
Issue 2: Curing Problems
Curing issues are another snag you might hit with UV cure glue for polypropylene, leading to weak or delayed curing. Here are some factors to watch:
Lack of UV light exposure is a common issue. UV-cure adhesives need enough UV light to kickstart the curing process. Not getting enough UV light means the glue might not set properly or could take longer to cure. Make sure the adhesive gets ample UV light for the necessary time.
Using the wrong curing equipment can also throw a wrench in the works. The UV light’s intensity and wavelength need to match the adhesive’s requirements for effective curing. Plus, the positioning of the light source in relation to the adhesive matters too, ensuring enough light hits the glue.
Sometimes, the adhesive itself might not be up to par. Different UV cure adhesives need specific types of UV light to cure correctly. Select an adhesive that fits your curing equipment and process settings.
To improve curing, you might need to up the UV exposure time, tweak the distance between the light source and the adhesive, or switch up your adhesive choice. Always check the manufacturer’s guidelines for the best curing practices.
By understanding these issues and how to tackle them, you’ll be better equipped to handle projects involving polypropylene with UV cure adhesive glue, ensuring stronger, more reliable results.
Issue 3: Yellowing or Discoloration
Yellowing or discoloration is a pesky problem you might face when using UV cure glue on polypropylene, which can mess up the look of your project. Several factors contribute to this, but there are ways to prevent it and keep your bond looking as good as new.
Exposure to UV light is a common culprit for yellowing. It can break down both the adhesive and polypropylene, changing their color. Choosing an adhesive that’s resistant to UV degradation is a smart move to maintain color stability over time.
Heat is another factor that can cause yellowing. High temperatures can speed up the degradation of both the adhesive and the polypropylene, leading to unwanted color changes. Make sure the adhesive you choose can handle the temperatures it’ll face in its working environment.
Certain chemicals can also lead to discoloration. Even though polypropylene resists many chemicals, some can react with the adhesive or the polypropylene itself, altering the color. Picking an adhesive that’s chemically compatible with the environment it’ll be used in is crucial.
To fend off yellowing or discoloration, using UV-resistant adhesives, steering clear of high heat, and choosing chemically compatible adhesives are key. Also, proper storage and handling of the adhesive help keep its color true.
Issue 4: Brittle or Cracked Bond
Brittle or cracked bonds are a real bummer and can weaken the integrity of your project. This issue can stem from several factors but fret not—there are ways to tackle them.
Choosing the wrong adhesive can leave you with a bond that’s too rigid and prone to cracking. Not all UV cure adhesives are flexible enough for polypropylene. Opt for an adhesive specifically designed for flexible applications, which usually have higher elongation properties to cope with movement and stress.
A poorly designed bond can also lead to issues. It’s important to consider joint geometry, stress distribution, and expected movements or vibrations. A well-thought-out bond design helps distribute stress evenly and reduces the risk of failure.
Improper curing conditions can also lead to a brittle bond. If the adhesive doesn’t fully cure or achieve its optimal mechanical properties, the bond may be weak and prone to cracking. Ensure the adhesive is exposed to the right curing conditions for the necessary time.
Improving bond strength and flexibility can involve selecting the right adhesive formulation, optimizing the bond design, and ensuring proper curing conditions.
Issue 5: Incomplete Curing
Incomplete curing is another common issue that results in a bond that’s not as strong as it should be. Several factors can lead to this, but they can be managed with a few tweaks.
Insufficient UV exposure is often to blame. If the adhesive doesn’t get enough UV light, it won’t cure properly. Make sure the adhesive is exposed to the correct amount of UV light for the time recommended by the manufacturer.
Using unsuitable curing equipment can also cause problems. The intensity and wavelength of the UV light need to match the adhesive’s requirements for effective curing. Additionally, the distance between the light source and the adhesive should be just right to ensure the adhesive gets enough UV light.
Sometimes, the issue may be with the adhesive formula itself. Different adhesives need different types of UV light to cure. It’s important to use an adhesive that’s compatible with your curing equipment and process parameters.
To improve curing, you might need to adjust the UV exposure time, tweak the distance between the light source and the adhesive, or switch to a different adhesive formulation. Always follow the adhesive manufacturer’s guidelines for the best results.
Troubleshooting Techniques for UV-Cure Adhesive Glue for Polypropylene
Tackling common issues with UV cure adhesive glue for polypropylene involves having a solid troubleshooting strategy. For poor adhesion, ensure you clean and degrease the surfaces thoroughly. If contamination is still an issue, consider using a primer or surface activation techniques like corona discharge or flame treatment. For curing problems, adjust the UV exposure time or the distance between the light source and the adhesive. Make sure the curing equipment meets the adhesive’s needs.
For yellowing or discoloration, choose UV-resistant adhesives and avoid high temperatures and incompatible chemicals. For brittle or cracked bonds, select adhesives designed for flexibility and optimize your bond design. For incomplete curing, ensure adequate UV exposure and compatibility with your equipment.
Last Words
In conclusion, UV cure glue for polypropylene is a reliable choice for many projects, but understanding its challenges is key to successful applications. Addressing issues like poor adhesion, curing problems, yellowing, brittleness, and incomplete curing helps enhance the performance and reliability of your bonds. With the right preventive measures and troubleshooting techniques, you can achieve durable and aesthetically pleasing results in your projects involving polypropylene.
For more about troubleshooting common issues with UV cure adhesive glue for polypropylene, you can pay a visit to DeepMaterial at https://www.epoxyadhesiveglue.com/category/epoxy-adhesives-glue/ for more info.