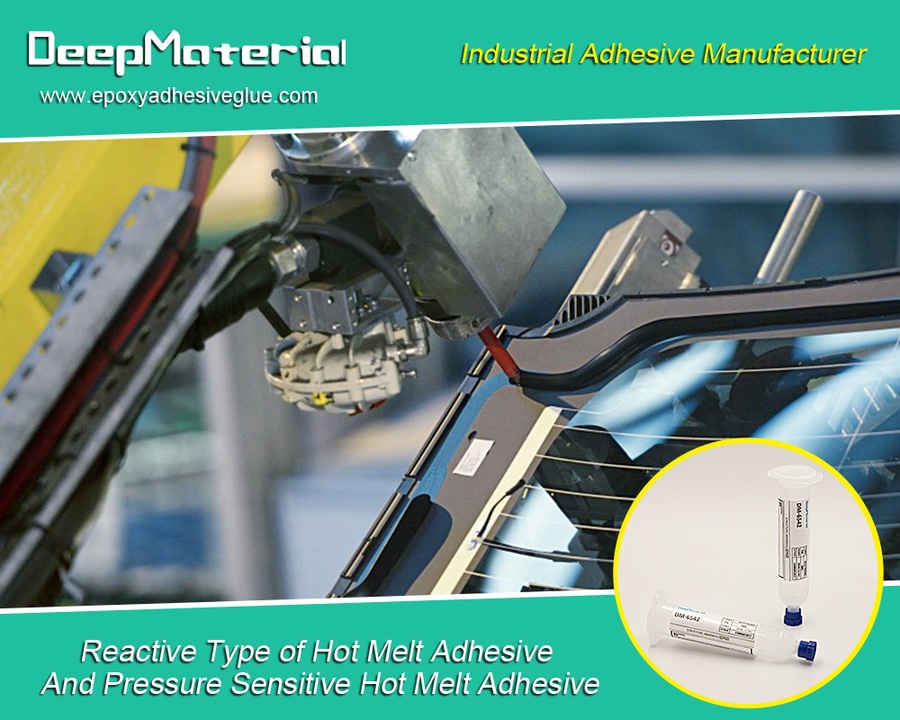
#Industry News
Comprehensive Guide to BGA Underfill Epoxy
Best BGA Underfill Epoxy Adhesive Glue Manufacturer
Ball Grid Array (BGA) packages are surface-mount packaging for integrated circuits. These packages provide:
High-density connections.
Making them ideal for advanced electronic devices such as smartphones.
Various consumer electronics. However
Due to the delicate nature of BGAs, underfill epoxy is often used to enhance their reliability and performance. This article delves into the intricacies of BGA underfill epoxy, its importance, types, application processes, and benefits.
What is BGA Underfill Epoxy?
BGA underfill epoxy fills the gap between a BGA package and the printed circuit board (PCB). This epoxy material is crucial for improving the solder joints’ mechanical strength and thermal cycling reliability. The primary purpose of underfill is to protect the solder joints from mechanical stress, thermal expansion, and environmental factors that can cause failure.
Composition and Properties
BGA underfill epoxies typically comprise a thermosetting resin, such as epoxy, filled with various additives to enhance its properties. Key properties include:
Thermal Conductivity:Helps dissipate heat away from the solder joints.
Low Viscosity:Ensures the epoxy can flow and fill the gaps effectively.
High Adhesion:Provides strong bonding to the BGA package and the PCB.
Curing Characteristics:The epoxy must cure adequately to form a reliable underfill.
Importance of BGA Underfill Epoxy
Enhancing Mechanical Strength
One of the primary functions of BGA underfill epoxy is to enhance the mechanical strength of the solder joints. Without underfill, the solder joints can be susceptible to cracking or breaking due to mechanical stress, such as vibrations or physical shocks. The epoxy acts as a cushion, absorbing and distributing these stresses more evenly.
Thermal Cycling Reliability
Electronic devices often experience temperature variations during operation, leading to thermal expansion and contraction. This can cause fatigue in solder joints over time. BGA underfill epoxy mitigates this issue by providing a uniform thermal expansion coefficient, reducing the stress on the solder joints, and enhancing the overall thermal cycling reliability.
Protection Against Environmental Factors
BGA underfill epoxy protects against environmental factors such as moisture, dust, and other contaminants, which can lead to corrosion or degradation of the solder joints. The epoxy forms a protective barrier, ensuring the longevity and reliability of the electronic device.
Types of BGA Underfill Epoxy
Several types of BGA underfill epoxies are available, each with specific characteristics and application methods. The choice of underfill depends on the application’s particular requirements and the manufacturing process.
Capillary Flow Underfill
Capillary flow underfill is the most commonly used type of underfill. It is applied to the edge of the BGA package and relies on capillary action to flow underneath it, filling the gap between the package and the PCB. This type of underfill is ideal for high-volume production due to its ease of application and reliability.
No-Flow Underfill
No-flow underfill is applied before the reflow soldering process. As the name suggests, this type of underfill does not flow after application. During the reflow process, the underfill cures and forms a solid bond. This method is suitable for applications where traditional capillary flow underfill may need to be more effective.
Molded Underfill
Molded underfill is used in advanced packaging technologies, such as flip-chip BGAs. The underfill is applied and cured in a mold, ensuring precise control over the underfill material and its distribution. This method offers excellent reliability and is used in high-performance electronic devices.
Pre-Applied Underfill
Pre-applied underfill is deposited onto the PCB before the BGA package is placed. This method simplifies the manufacturing process by eliminating the need for a separate underfill dispensing step, and it is particularly useful in high-speed manufacturing environments.
Application Process of BGA Underfill Epoxy
The BGA underfill epoxy application process is critical to ensuring proper adhesion, coverage, and curing. It typically involves several steps, including surface preparation, dispensing, and curing.
Surface Preparation
Surface preparation is a crucial step in the application of BGA underfill epoxy. To ensure proper adhesion, the surfaces of both the BGA package and the PCB must be clean and free of contaminants. This may involve cleaning with solvents, plasma treatment, or other methods to remove any residues or particles.
Dispensing
The underfill epoxy can be dispensed using various methods, depending on the underfill and the specific application requirements. Standard dispensing methods include:
Needle Dispensing:A needle is used to apply the underfill epoxy to the edge of the BGA package. This method is commonly used for capillary flow underfill.
Jet Dispensing:Jet dispensers can rapidly apply small amounts of underfill epoxy with high precision. This method is ideal for high-speed production lines.
Stencil Printing:For pre-applied underfill, stencil printing can be used to deposit the epoxy onto the PCB in a controlled manner.
Curing
Curing is the final step in the application process, where the underfilled epoxy is transformed from a liquid to a solid state. The curing process can be done using various methods, including thermal, UV, or a combination of both. The curing parameters, such as temperature and time, must be carefully controlled to ensure the underfilled epoxy’s proper curing and optimal performance.
Benefits of Using BGA Underfill Epoxy
Improved Reliability
The primary benefit of using BGA underfill epoxy is electronic device reliability. By protecting the solder joints from mechanical stress, thermal cycling, and environmental factors, underfilling epoxy ensures the longevity and performance of the device.
Enhanced Performance
BGA underfill epoxy can also enhance the performance of electronic devices by improving thermal conductivity and reducing thermal resistance. This helps in effective heat dissipation, prevents overheating, and ensures stable operation.
Cost-Effective Solution
Although applying underfill epoxy adds an extra step to the manufacturing process, it can be a cost-effective solution in the long run. Underfill epoxy can save costs associated with device failures and warranty claims by preventing failures and reducing the need for repairs or replacements.
Versatility
BGA underfill epoxy is versatile and can be used in various applications, from consumer electronics to industrial and automotive applications. Its adaptability to multiple manufacturing processes and requirements makes it a valuable material in the electronics industry.
Challenges and Considerations
While BGA underfill epoxy offers numerous benefits, challenges and considerations must also be addressed to ensure its effective use.
Material Selection
Choosing the right underfill epoxy material is crucial for achieving optimal performance. Factors such as thermal conductivity, viscosity, curing characteristics, and adhesion properties must be carefully considered based on the specific application requirements.
Process Control
The application process of underfill epoxy requires precise control to ensure consistent and reliable results. This includes controlling the dispensing parameters, curing conditions, and surface preparation methods. Any variations in the process can lead to defects or suboptimal performance of the underfill epoxy.
Compatibility with Other Materials
Compatibility with other materials used in the electronic device, such as the BGA package, PCB, and solder materials, is essential for achieving proper adhesion and performance. The underfill epoxy must be compatible with these materials to avoid issues such as delamination or poor bonding.
Environmental and Safety Considerations
The use of underfill epoxy also involves environmental and safety considerations. Proper handling, disposal, and compliance with environmental regulations are essential to minimize the environmental impact and ensure the safety of workers engaged in the application process.
Future Trends in BGA Underfill Epoxy
As electronic devices evolve, the demand for more advanced and reliable packaging solutions, including BGA underfill epoxy, is expected to grow. Future trends in BGA underfill epoxy include:
Development of Advanced Materials
Research and development efforts are focused on creating advanced underfill epoxy materials with improved properties, such as higher thermal conductivity, lower viscosity, and faster curing times. These materials will enable more efficient and reliable underfill solutions for next-generation electronic devices.
Automation and Process Optimization
Applying BGA underfill epoxy is moving towards greater automation and process optimization. Advanced dispensing technologies, such as jet dispensing and automated inspection systems, are being developed to improve the precision and efficiency of the underfill application process.
Integration with Emerging Technologies
BGA underfill epoxy is also integrated with emerging technologies, such as flexible electronics and 3D packaging. These technologies require innovative underfill solutions to address the unique challenges associated with their design and manufacturing processes.
Conclusion
BGA underfill epoxy plays a crucial role in enhancing electronic devices’ reliability, performance, and longevity. Its ability to protect solder joints from mechanical stress, thermal cycling, and environmental factors makes it an indispensable material in the electronics industry. Manufacturers can ensure the production of high-quality and reliable electronic devices by understanding the importance, types, application processes, and benefits of BGA underfill epoxy. As technology advances, developing new materials and application techniques will further enhance the capabilities and effectiveness of BGA underfill epoxy in meeting the demands of next-generation electronics.
For more about choosing the Comprehensive Guide to BGA Underfill Epoxy, you can pay a visit to DeepMaterial at https://www.epoxyadhesiveglue.com/category/epoxy-adhesives-glue/ for more info.