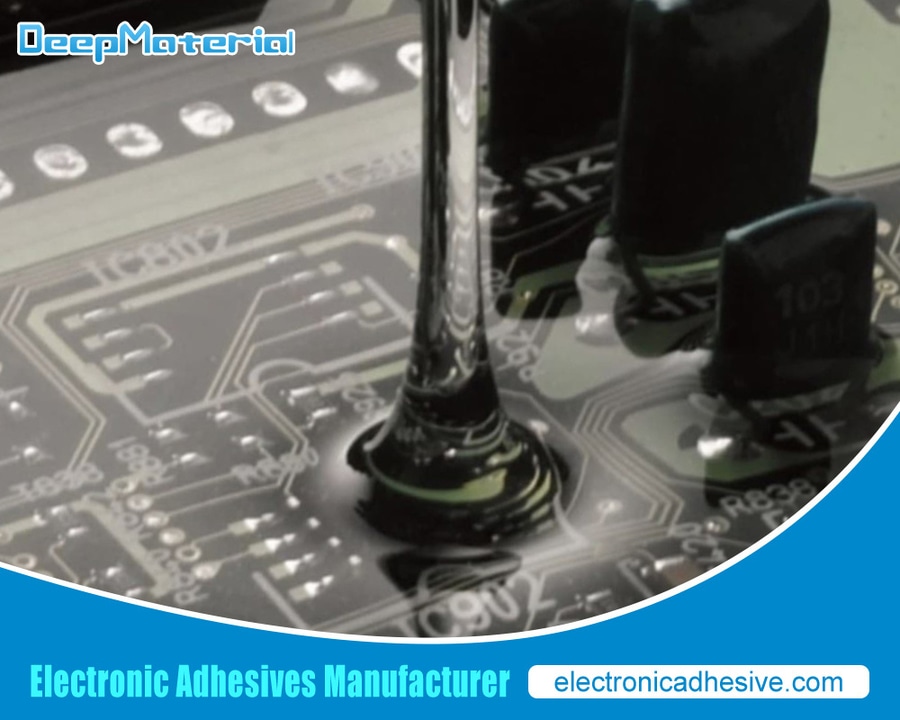
#Industry News
Industrial Bonding Adhesives: A Comprehensive Guide
Best Industrial Bonding Adhesive Glue Manufacturer
Introduction to Industrial Bonding Adhesives
Industrial bonding adhesives are crucial in manufacturing and assembly processes across various industries. They join materials together, providing strength, durability, and often unique benefits that traditional mechanical fastening methods cannot offer. Industrial adhesives have become indispensable in industries ranging from automotive to aerospace, electronics to construction, enabling innovations and improving efficiency.
Types of Industrial Bonding Adhesives
There are several types of industrial bonding adhesives, each with distinct properties and applications. Understanding these types is essential for selecting the suitable adhesive for specific tasks.
Epoxy Adhesives
Epoxy adhesives are renowned for their exceptional strength and durability. They consist of two components: a resin and a hardener. When mixed, they undergo a chemical reaction that forms a rigid, high-strength bond. Epoxies are widely used in the aerospace and automotive industries due to their resistance to chemicals, heat, and environmental conditions.
Polyurethane Adhesives
Polyurethane adhesives offer flexibility and toughness, making them ideal for applications requiring resistance to impact and vibration. They bond well with various materials, including plastics, metals, and wood. Polyurethanes are commonly used in the construction industry to bond insulation panels and in the automotive sector to bond plastic parts.
Acrylic Adhesives
Acrylic adhesives are known for their fast curing times and intense bonds. They can bond various materials, including metals, plastics, and composites. Acrylics are often used in electronics and medical devices where quick assembly and strong bonding are critical.
Cyanoacrylate Adhesives
Cyanoacrylate adhesives, or superglues, are characterized by their rapid bonding capabilities. They are ideal for small, precise applications and can bond rubber, plastic, and metal in seconds. However, their brittleness limits their use in high-stress applications.
Silicone Adhesives
Silicone adhesives are valued for their flexibility, heat resistance, and sealing properties. They are commonly used in the automotive and electronics industries to seal and bond components exposed to high temperatures and harsh environments.
Applications of Industrial Bonding Adhesives
Industrial bonding adhesives’ versatility allows them to be used in a multitude of applications across various industries. Here are some key sectors where these adhesives are indispensable.
Automotive Industry
Adhesives are extensively used in the automotive industry to bond various components, including body panels, glass, and interior parts. They help reduce vehicle weight, improve fuel efficiency, and enhance crashworthiness. Structural adhesives provide robust bonds that contribute to the overall strength and safety of the vehicle.
Aerospace Industry
The aerospace industry demands materials and bonding solutions that can withstand extreme conditions. Epoxy and polyurethane adhesives are commonly used to bond lightweight composites and metals, ensuring the integrity and performance of aircraft structures. Adhesives also play a vital role in reducing aircraft weight, leading to improved fuel efficiency and reduced emissions.
Electronics Industry
In electronics manufacturing, adhesives are essential for assembling and encapsulating components. They provide electrical insulation, thermal management, and protection against environmental factors. Silicone and acrylic adhesives are widely used for potting and sealing electronic components, ensuring their reliability and longevity.
Construction Industry
Adhesives benefit the construction industry in various applications, including bonding insulation panels, flooring, and structural elements. Polyurethane and epoxy adhesives provide strong, durable bonds that enhance buildings’ structural integrity. Adhesives also offer speed and ease of installation advantages compared to traditional mechanical fastening methods.
Medical Industry
Medical devices require adhesives that meet stringent safety and performance standards. Acrylic and silicone adhesives are commonly used in the medical field for bonding components of diagnostic equipment, wearable devices, and disposable products. These adhesives offer biocompatibility, sterilization resistance, and reliable bonding in critical applications.
Advantages of Using Industrial Bonding Adhesives
Industrial bonding adhesives offer numerous advantages over traditional fastening methods, making them a preferred choice in many applications.
Weight Reduction
Adhesives enable the bonding of lightweight materials, reducing the overall weight of products. This is particularly important in industries like automotive and aerospace, where weight reduction leads to improved fuel efficiency and performance.
Stress Distribution
Unlike mechanical fasteners, which create localized stress points, adhesives distribute stress evenly across the bonded area. This results in more robust, durable bonds and reduces the risk of material fatigue and failure.
Design Flexibility
Adhesives offer greater design flexibility, allowing dissimilar materials and complex shapes to join. This opens up new possibilities for innovative product designs and manufacturing processes.
Improved Aesthetics
Adhesives provide clean, seamless bonds that enhance the aesthetics of finished products. They eliminate the need for visible screws, rivets, or welds, resulting in a smoother and more visually appealing appearance.
Enhanced Performance
Many industrial adhesives offer superior resistance to environmental factors such as heat, moisture, chemicals, and UV radiation. This enhances the performance and longevity of bonded components in demanding applications.
Challenges and Considerations in Using Industrial Bonding Adhesives
While industrial bonding adhesives offer significant advantages, there are also challenges and considerations to consider when using them.
Surface Preparation
Proper surface preparation is crucial for achieving solid and durable adhesive bonds. Contaminants such as oil, dust, and oxidation can weaken the bond, so thorough cleaning and, in some cases, surface treatments like abrasion or priming are necessary.
Curing Time
Adhesives’ curing times can vary widely, from seconds to several hours or even days. Understanding the curing process and allowing adequate time for the adhesive to fully cure is essential to ensuring optimal bond strength.
Environmental Factors
Environmental conditions such as temperature and humidity can affect adhesive performance. Therefore, it is important to select adhesives that are suitable for the specific conditions they will be exposed to during both application and service life.
Compatibility with Materials
Not all adhesives are compatible with every material. To ensure a strong and lasting bond, it is important to select an adhesive designed for the specific materials being bonded.
Health and Safety
Some adhesives contain chemicals that can harm health if not handled properly. When working with adhesives, it is essential to follow safety guidelines, use appropriate personal protective equipment (PPE), and ensure proper ventilation.
Future Trends in Industrial Bonding Adhesives
Industrial bonding adhesives are continually evolving, driven by materials science and advancements in manufacturing technology. Here are some trends shaping the future of industrial adhesives.
Sustainable Adhesives
As industries strive for more sustainable practices, there is a growing demand for environmentally friendly adhesives. Research is focused on developing adhesives with reduced environmental impact, such as bio-based adhesives and formulations with lower volatile organic compound (VOC) content.
Smart Adhesives
Innovative adhesives with added functionalities, such as self-healing, conductivity, and sensing capabilities, are being developed. These advanced adhesives can enhance the performance and reliability of bonded components, particularly in high-tech industries like electronics and aerospace.
Enhanced Bonding Technologies
Innovations in bonding technologies, such as ultraviolet (UV) curing and advanced dispensing systems, are improving the efficiency and precision of adhesive application. These technologies enable faster curing times, reduced waste, and more consistent bond quality.
Customized Adhesive Solutions
Manufacturers are increasingly seeking customized adhesive solutions tailored to their specific applications. This trend is driving the development of adhesives with specialized properties, such as high-temperature resistance, flexibility, and chemical compatibility, to meet the unique demands of different industries.
Conclusion
Industrial bonding adhesives have revolutionized how materials are joined in manufacturing and assembly processes. Their versatility, strength, and unique benefits make them indispensable in various industries, from automotive and aerospace to electronics and construction. As technology advances and sustainability becomes a greater focus, the development of innovative and environmentally friendly adhesives will continue to drive the evolution of this essential field. Understanding industrial bonding adhesives’ types, applications, advantages, and challenges is critical to leveraging their full potential in modern manufacturing and beyond.
For more about choosing the top industrial bonding adhesives: a comprehensive guide, you can pay a visit to DeepMaterial at https://www.electronicadhesive.com/ for more info.