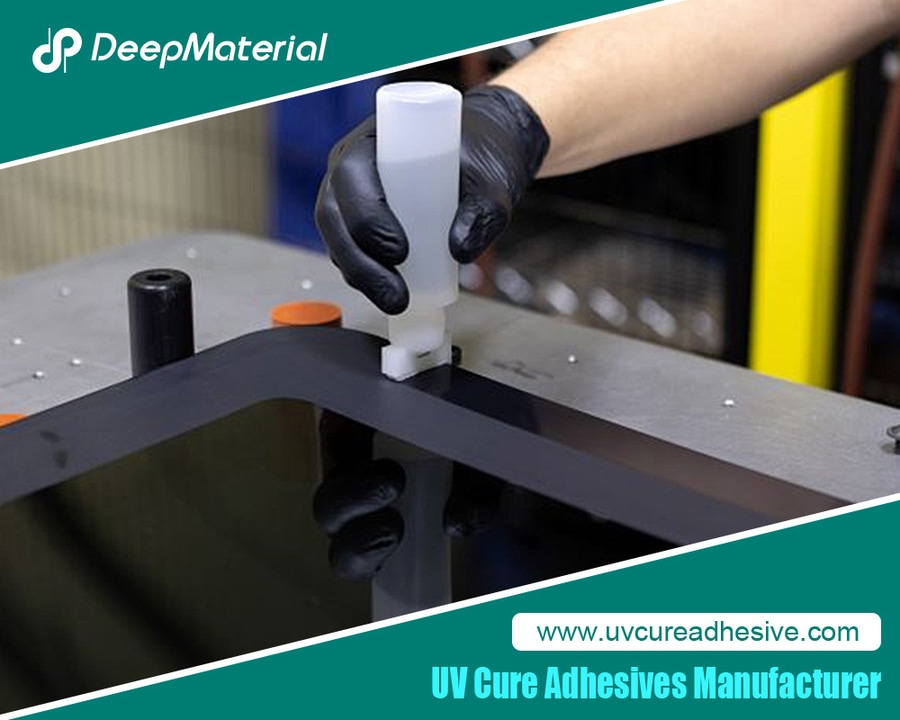
#Industry News
The Adhesive Manufacturing Process: A Comprehensive Guide
Best UV Adhesive Glue Manufacturer
The adhesive manufacturing process is a crucial aspect of many industries and indispensable in bonding various materials. Adhesives, commonly called glues or sealants, are essential in products ranging from simple household items to complex machinery and medical devices. With the growing demand for advanced materials and more sustainable solutions, adhesive manufacturing has evolved to meet industry requirements. In this article, we’ll explore the detailed adhesive manufacturing process, the materials involved, and the various applications of adhesives, offering a clear understanding of how these crucial substances are produced and utilized.
The Basics of Adhesive Manufacturing
Adhesive manufacturing involves synthesizing and formulating materials that can bind two surfaces when applied. These materials may include natural or synthetic compounds that, when activated, form a strong, durable bond. The primary components of adhesives include:
Polymers: The backbone of adhesive products, providing strength and flexibility.
Additives: Improve performance, modify viscosity, or enhance curing speed.
Solvents or Water: Used to dissolve or disperse the adhesive’s components.
Tackifiers:Enhance the stickiness of the adhesive for better surface grip.
The adhesive manufacturing process can be broken down into several key stages, from selecting raw materials to producing the final product.
Critical Stages of the Adhesive Manufacturing Process
Raw Material Selection
Selecting suitable raw materials is the foundation of producing a high-quality adhesive. Manufacturers choose materials based on the intended application, properties required, and environmental considerations.
Polymers: Depending on the adhesive type, polymers can be natural or synthetic. Rubber-based adhesives are often used in pressure-sensitive applications.
Fillers: These are added to increase the bulk and lower the cost of adhesives. They can also impart specific properties such as strength, durability, or conductivity.
Plasticizers: These plasticizers increase flexibility and reduce adhesive brittleness that may become hard and rigid after application.
Mixing and Compounding
Once the raw materials are selected, they are thoroughly mixed to form a homogenous adhesive. This phase ensures that the polymer base, additives, solvents, and tackifiers are uniformly blended, contributing to consistent quality and performance.
Batch Process: Ingredients are measured and mixed in batches. This process is standard for small-scale or highly customized adhesive production.
Continuous Process: A continuous flow of materials is mixed and compounded, which is ideal for large-scale production where efficiency and consistency are critical.
Depending on the type of adhesive, various methods are employed to combine the raw materials. These methods include mechanical, high-shear, or even ultrasonic mixing for precision.
Reactor Processing
In certain types of adhesives, such as epoxies or polyurethanes, the mixing process is followed by a chemical reaction inside a reactor. This phase ensures the polymerization of the adhesive ingredients, allowing them to reach their intended performance characteristics.
Exothermic Reactions: Some adhesives require heat to start a polymerization reaction. Careful temperature and pressure monitoring ensures the adhesive reaches the correct viscosity and bonding strength.
Endothermic Reactions: In other cases, reactions might absorb heat, requiring external energy to complete the chemical reaction and produce the adhesive.
This part of the process is critical for creating thermosetting adhesives that harden upon curing or exposure to heat.
Filtration and Degassing
Once the adhesive mixture has been chemically processed, it undergoes filtration to remove any impurities or undissolved particles. Degassing is an equally important step, as the adhesive must be free of air bubbles to ensure a smooth application and strong bonding.
Filtration Systems: Various filtration systems, such as mesh or cloth filters, remove particulates from the adhesive.
Vacuum Degassing: Some adhesives, particularly in aerospace and electronics, require high purity levels. A vacuum chamber removes entrapped gases, ensuring a defect-free adhesive layer upon application.
Packaging and Storage
After the adhesive has been processed and filtered, it is ready for packaging. Packaging can vary based on the type of adhesive and its intended use. Some adhesives are stored in bulk containers, while others are available in smaller tubes or cartridges.
Bulk Packaging: Often used for large-scale applications in manufacturing or construction. These can include drums, totes, or large pails.
Consumer Packaging: Adhesives may be packaged in tubes, spray bottles, or sticks for easy use in small-scale applications.
Appropriate packaging is crucial, as certain adhesives may have specific storage requirements, such as temperature control or protection from moisture.
Types of Adhesives and Their Manufacturing Variations
Different types of adhesives are manufactured through distinct processes, depending on the intended application and the chemical properties required. Below are some common types of adhesives and the specific processes involved in their production.
1. Water-based Adhesives
Water-based adhesives, often used in packaging, bookbinding, and construction, are created by dissolving polymers in water. These adhesives are environmentally safe and produce fewer volatile organic compounds (VOCs).
Production Process: The polymer is dispersed in water, creating a colloidal solution or emulsion. Additives such as preservatives, stabilizers, and thickeners are added to improve adhesion and increase shelf life.
Drying: After the adhesive is applied, the water evaporates, leaving behind a solid bond.
2. Solvent-based Adhesives
Solvent-based adhesives are typically used in applications where robust and quick bonding is needed, such as in the automotive or electronics industries. These adhesives are created by dissolving polymers in a solvent.
Production Process: The polymer is dissolved in an organic solvent to create a liquid adhesive. Solvents such as acetone or toluene may be used.
Evaporation: Once applied, the solvent evaporates, leaving behind a solidified bond. The type of solvent and adhesive thickness can control the evaporation rate.
3. Hot Melt Adhesives
Hot melt adhesives are popular in packaging, product assembly, and woodworking. These adhesives are thermoplastic, meaning they become liquid when heated and solidify upon cooling.
Production Process: Raw thermoplastic polymers, resins, and waxes are melted at high temperatures. The mixture is then cooled into solid blocks, pellets, or sticks for later use.
Application:The adhesive is reheated at the point of use and applied in a molten state. Upon cooling, it forms a strong bond.
4. Reactive Adhesives
Reactive adhesives require a chemical reaction to form a permanent bond. Examples include epoxies, cyanoacrylates (super glue), and polyurethanes.
Two-component System: Many reactive adhesives consist of two parts – a resin and a hardener. When combined, they undergo a chemical reaction to create a hardened bond.
Curing Process: These adhesives often require time to cure fully, during which the chemical reaction occurs. The curing speed can be influenced by temperature, humidity, and the adhesive formulation.
Critical Considerations in Adhesive Manufacturing
Manufacturing adhesives is not just about mixing ingredients. Several critical factors influence the final product’s performance, longevity, and safety. These considerations ensure that adhesives meet industry standards and customer requirements.
Environmental Impact
Reducing manufacturing processes’ environmental footprint is a priority in today’s world. Adhesive manufacturers focus on reducing volatile organic compounds (VOCs), minimizing waste, and developing eco-friendly formulations.
Water-based formulations: Water-based formulations produce lower emissions and are safer for the environment than solvent-based adhesives.
Biodegradable Adhesives: Some adhesives are formulated to be biodegradable, especially in industries like packaging and medical devices.
Safety and Compliance
Safety is paramount in the production and application of adhesives. Many adhesives contain chemicals that can be hazardous if not handled properly.
Hazardous Material Handling: To avoid chemical exposure, fires, or explosions, proper safety protocols must be followed during manufacturing.
Regulatory Compliance:Adhesives must comply with various regulations and standards, including environmental regulations, workplace safety laws, and specific industry standards.
Quality Control
Adhesives must perform consistently across various applications. Quality control procedures ensure the final product meets required strength, durability, and performance metrics standards.
Testing: Adhesives are subjected to rigorous testing, including shear strength, peel resistance, and environmental exposure tests.
Batch Consistency:In large-scale production, ensuring batch-to-batch consistency is crucial. Automated systems help maintain precise control over ingredients and processing conditions.
Conclusion
The adhesive manufacturing process is a complex and precise science that combines chemistry, engineering, and material science to create products essential in various industries. From raw material selection to the final application, every stage plays a critical role in ensuring the quality and effectiveness of the adhesive. With continuous technological advancements and the growing demand for environmentally friendly solutions, adhesive manufacturing will continue to evolve, driving innovation in industries like construction, automotive, electronics, and healthcare.
For more about choosing the adhesive manufacturing process: a comprehensive guide, you can pay a visit to DeepMaterial at https://www.uvcureadhesive.com/ for more info.