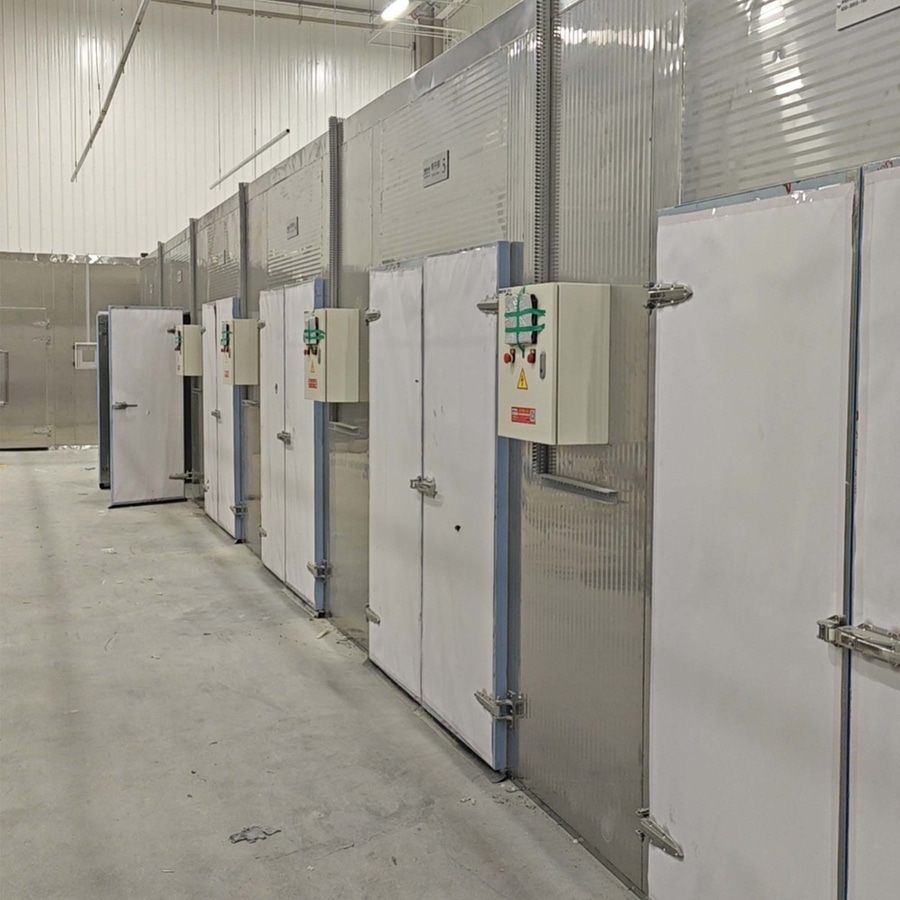
#Industry News
Classification of Drying Equipment
WesternFlag
Ⅰ. Convection Drying
In drying equipment, the more common type of drying equipment is the convection heat transfer dryer. For example, hot air drying, hot air and material contact for heat exchange in order to evaporate moisture. Common types of convection drying equipment are air suspension dryers, such as fluidized bed dryers, flash dryers, air dryers, spray dryers, ventilation dryers, flow dryers, air flow rotary dryers, stirring dryers, parallel flow dryers, rotary dryers and so on.
In practical application, there are single machines used and combined machines used. Air flow dryer, fluidized bed dryer, spray dryer, etc. are using hot air as heat source, and the transfer of materials is completed while drying, and such dryers are mainly characterized by the absence of transmission parts.
Ventilation dryer
Make the surface of the block or the material that has become fixed shape contact with the hot air. Drying rate is low, but the application range is wide.
Fluidized bed dryer
Let the hot air blow in evenly from the bottom of the layer of powder and granular materials and make it flow, so that the materials will be vigorously mixed and dispersed. The drying rate is high.
Airflow dryer
This method makes the powder dispersed in high temperature hot air and conveys the material while drying. This model has a short drying time and is suitable for handling materials in large quantities. If the material into the dryer before using mechanical methods to remove most of the water before entering the air dryer is more economical.
Spray dryer
So that the solution or slurry materials in the high temperature hot air atomization, droplets falling at the same time instantaneous drying. This method of drying time is short, suitable for mass production, for pharmaceuticals, punch, dye drying.
Rotary cylinder dryer
Make the powder, block, slurry materials through the rotating drum contact hot air. This method is suitable for mass production. After drying the mud material can be discharged as granular material, many high temperature resistant mineral drying are used in this way.
Flash dryer
The material is stirred by the high-speed rotating stirring blade, so that it is dispersed in the rotating movement of the gas stream at the same time drying. Generally applicable to the drying of medium-volume materials, mostly used for drying paste materials.
Ⅱ. Conduction Drying
Conduction drying is very adaptable to moist particles, and conduction drying equipment has a high thermal efficiency. The evaporated water vapor is extracted by vacuum or discharged by airflow, which is the main carrier of moisture, and vacuum operation is recommended for heat-sensitive granular materials. In conduction drying equipment, paddle dryer is used for drying paste materials. Rotary dryers with internal flow tubes have now been designed, such as the immersion fluidized bed dryer for drying heat-sensitive polymers or fat pellets, which is only one-third of the size of an ordinary fluidized bed dryer.
Vacuum drying is the process of low temperature and low pressure drying by heating the material under vacuum conditions to make the moisture diffuse internally, evaporate internally, sublimate, and evaporate on the surface. It has the advantages of low heating temperature, good antioxidant performance, uniform product moisture content, superior quality and application. Vacuum drying is expensive to operate, and vacuum drying is recommended only when the material must be dried under low temperature or oxygen deficiency, or when it will be deteriorated by drying under heating medium and high temperature. For a certain evaporation efficiency, high temperature operation is used so that the gas flow rate can be reduced and the volume of equipment can be reduced. For low-temperature drying operation, appropriate low-temperature waste heat or solar collector can be selected as the heat source, but the volume of the dryer is relatively large.
Ⅲ. Combination drying
Using different drying methods, different drying principle combination, can play their respective strengths and make up for their shortcomings of the drying equipment. For example, direct drying method and indirect drying method and use indirect drying method to provide drying the majority of the heat required. In this way, the drying rate can be improved, and the direct and indirect drying method and drying equipment with small equipment volume and high thermal efficiency can be obtained.
Combined drying equipment is also used more and more, such as spray dryer and vibration fluidized bed dryer combination, rake dryer and vibration fluidized bed dryer combination, rotary mixing dryer, conduction mixing dryer, air dryer and fluidized bed dryer combination. Combination of the purpose is to obtain lower moisture, such as single spray dryer can be obtained 1% -3% moisture content of the product, such as the moisture content of 0.3% or less, the exhaust temperature is often required to 120 ℃ or more, the loss of heat energy is very large. Similarly, if there are further requirements for moisture, moisture content of less than 0.1%, the exhaust temperature is required above 130 ℃. In order to save thermal energy, in the design of the general use of 90 ℃ exhaust temperature of the spray dryer, so that the moisture to 2%, heat recovery generated by the 60 ℃ hot air can be used in series for the drying of the horizontal fluidized bed, the end of the moisture can reach 0.1% or less, and thermal energy can save 20%.
In some cases, when the product is dried or processed, the heat sensitivity of the product produces a change, or the characteristics of the product change. Obviously, in this case the use of two or more than two different forms of drying equipment combination of drying is good.
Then, how to choose suitable dryers for your materials ?
Welcome to communicate!