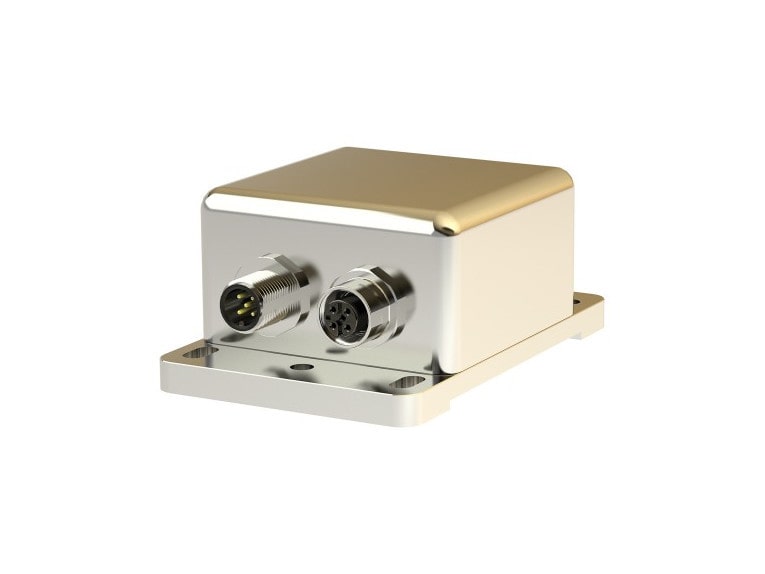
#Product Trends
Inclination sensor with gyroscope correction - we got the hang of it
TWK contributes by means of sensor fusion with a gyroscope and offers inclination sensors with gyroscope correction.
Something is moving - but if possible not in such a way that disruptions in an operating process occur and certainly not accidents. TWK makes a contribution with the help of sensor fusion with a gyroscope and offers inclination sensors with gyroscope correction. Gyros comes from Greek and means rotation - so it has to do with turning movements. It is a clever combination of measurement signals to produce a corrected output signal that displays the measurement angle exactly - even under adverse operating conditions.
What is the task?
Well: It's about inclination measurement. An inexpensive and yet good method is to use so-called MEMS sensors for this purpose. These electronic chips are small and consist of electronic and micromechanical structures, i.e. in addition to the usual microelectronic circuits there are also mechanically movable structures in the chips. These structures deflect when the g-force of the earth acts on them. At the same time the capacitances (capacitors) formed by these structures change. These are measured and an angle of inclination is calculated and output.
If, however, this MEMS cell is subjected to other accelerations in addition to the acceleration due to gravity - be it from vibrations or from acceleration in a vehicle - these MEMS structures are also moved and a falsified tilt value is output. The connected controller may react incorrectly and an accident may occur - for example with a mobile machine: mobile cranes, concrete pumps, forklift trucks, etc.
Now the gyroscope comes into play. It is a rotation rate sensor, also in MEMS technology. However, the micromechanical structures are designed in such a way that angular velocities (°/s) are measured and output as an output signal. It therefore measures changes in a tilt angle and not the tilt angle itself when the MEMS gyroscope rotates around its own axis or an extended axis. The advantage is that the linear accelerations mentioned above, which interfere with the accelerometer MEMS sensor, do not affect the gyroscope MEMS sensor as they do not represent rotation.
So how can these two sensors be combined to form a tilt measurement system that is insensitive to interference?
With sensor data fusion and Kalman filter! The solution is to merge both measuring signals and optimize them using a specific filter - the Kalman filter. This filter technology makes it possible to calculate, correct and predetermine the measured value to be output, i.e. to determine it in advance for a short time. This is necessary because the accelerometer cannot provide an exact tilt measurement value when dynamic interfering accelerations occur. Instead, a recursive algorithm is used in real time (<1 ms cycle time) to first estimate the next output values based on the previous measured values and then constantly optimize them with the aid of new real measured values. In order for the signal of the rotation rate sensor to be added, it must first be integrated over time. Finally, a series of parameters are used to optimize the system as well as possible, to smooth the measured values and, if necessary, to adapt them to application-specific conditions. All kinds of application-related simulations and measurements at TWK show that the sensor fusion system works precisely and reliably and enables update rates of significantly less than 1 ms - not least thanks to clever and 'space-saving' programming in the controller.
The picture (Kalman Filter) shows a tilt change measurement with disturbance components (red). A simple averaging over 1000 values (green) of the pure acceleration data can smooth moderate vibrations, but causes a noticeable time delay (~1 s). Combining both sensors via the Kalman filter (blue) leads to an almost ideal behaviour.
This sensor system ensures safe, hazard-avoiding use not only for mobile machines, but also during operation of engines, hydraulic pumps or other actions that generate strong vibrations. It measures more accurately and faster than the previous sensors and is largely insensitive to interfering accelerations and, in addition, also to lateral inclination deflection. These sensors are very well suited for applications with dynamic requirements, where precise inclination angles must nevertheless be continuously detected and transmitted to a control system.
Where can they be used?
A good example for the use of the merged sensors are mobile concrete pumps. These vehicles drive to a construction site, are aligned - i.e. the undercarriage is set horizontally - and the boom with the trunk is extended. The undercarriage and boom are equipped with inclination sensors - so far, everything is fine. However, when the concrete pump delivers the concrete, there are short but strong impacts. The accelerations that occur disturb the tilt measurement. The signal from the gyroscope is 'zero' despite the linear interfering acceleration. The calculation algorithm then recognizes that there is no change in inclination and retains the previous inclination value, which is now subject to strong fluctuations on the MEMS side. If the slope changes exactly at the time of the disturbance, the gyroscope outputs a change in °/s with a non-zero integral. Both values are considered by the Kalman filter and are used to generate a useful slope value.
The combined sensors have an operating temperature range of -40° to +85° C and measure inclination angles up to ±100° with a resolution of 0.01° and an accuracy in the range of ±0.1°. The response time is 0.1 s. It can be measured in one or two axes. The robust aluminium housing with an IP67 protection class can withstand even adverse environmental conditions without any problems. Protection classes up to IP69K are possible.
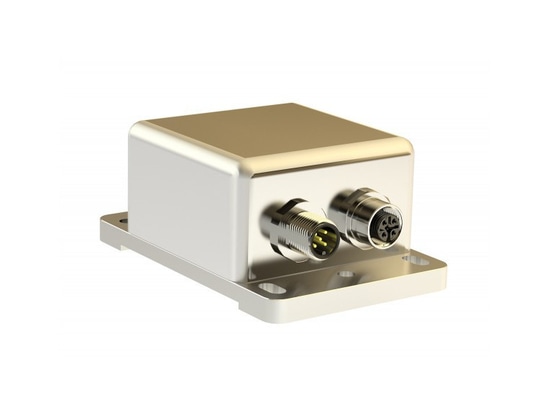