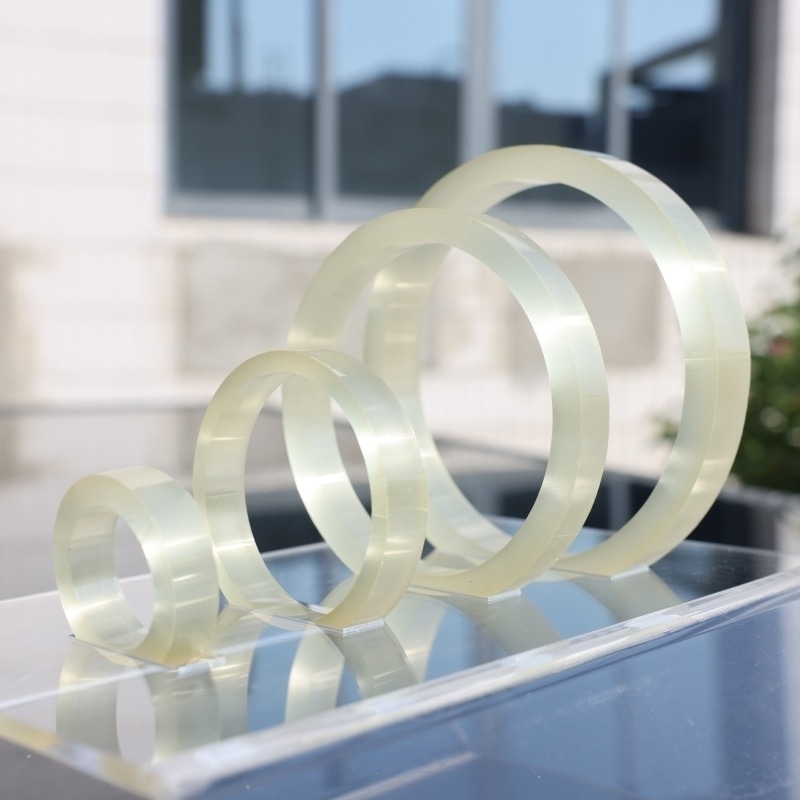
#Product Trends
The UV Curing Process and Equipment for Fiber Optic Coils
UV Curing Process and Equipment for Fiber Optic Coils
The fiber optic coil is a core component of the fiber optic gyroscope (FOG) used to sense the Sagnac phase difference between two counter-propagating light waves caused by the input angular velocity. Its performance is one of the key factors affecting the overall performance of the fiber optic gyroscope.
Our mainstream fiber optic coil products are wound using polarization-maintaining (PM) fibers in a standard symmetric winding pattern. During the winding process, UV-curable adhesive is applied synchronously, and the coil is formed after UV curing. A cross-sectional schematic of the fiber optic coil is shown in Figure 1.1 below.
UV curing for fiber optic coils is a photochemical reaction that uses a UV light source to trigger a chemical reaction between the photoinitiator in the adhesive, resulting in adhesive curing.
Currently, the commonly used UV curing equipment in the fiber optic coil industry is the UV mercury lamp curing system. This system consists of four main components: a UV mercury lamp light source, a reflective device, a cooling system, and auxiliary control devices.
During the curing process of fiber optic coils, the gaps between fibers are filled with cured adhesive, introducing new stresses to the fibers. These stresses primarily include shrinkage stress caused by the curing process, thermal stress resulting from environmental temperature changes, and bonding stress due to adhesion forces. As polarization-maintaining (PM) fibers are stress-sensitive materials, external stresses can alter the internal stress distribution within the fibers, thereby affecting the extinction ratio of the fiber coils and the overall system performance.
Traditional UV mercury lamp curing equipment, characterized by its technological maturity and low cost, is currently widely used in the curing process of PM fiber coils. However, this equipment has certain drawbacks and issues that remain unresolved:
1.Low UV Conversion Efficiency:
The UV mercury lamp light source provides the energy required for UV curing and is the core component of UV curing equipment. However, the UV efficiency of traditional mercury lamps is approximately 30%, with the remaining 60%–70% being infrared and thermal radiation energy, resulting in low UV conversion efficiency. Improper use can also lead to elevated lamp temperatures, negatively affecting the fiber coils.
2.Decline in Light Intensity Over Time:
Traditional mercury lamps require significant energy to operate, and their light intensity (irradiance) decreases over time. Frequent monitoring of UV light intensity with an irradiance meter is necessary, adding complexity to process control and quality management.
Light intensity refers to the UV energy received per unit area of the coating, measured in units of . It is calculated using the following formula:
3.Short Lifespan:
Traditional mercury lamps have a relatively short lifespan, with an average usage life of ≤1,000 hours.
4.Long Startup Time:
Mercury lamps require a cold startup and a prolonged induction period, typically taking around 10 minutes to reach full spectral output. Once turned off, they cannot be restarted immediately and need a cooling period of 15–20 minutes before reactivation, which affects operational convenience.
5.High Protective Requirements:
During operation, traditional mercury lamps generate ozone, which is harmful to humans. Moreover, the wide irradiation range of mercury lamps can pose risks to the eyes and skin if used improperly. This necessitates the inclusion of protective systems.