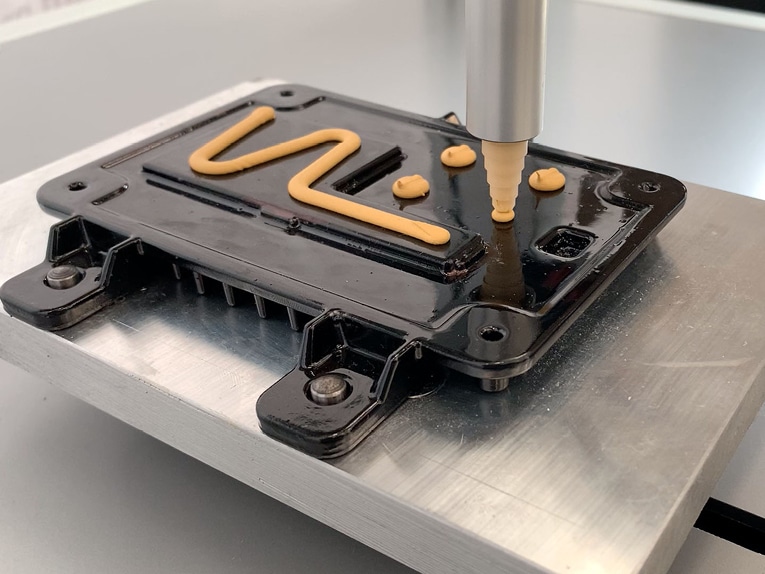
#Product Trends
GAP FILLERS and Thermo-conductive pastes
Thermal Management process: one of the most discussed and developed topics!
The continuous evolution of technology and its "electrification" has resulted in the need in recent years to lend some tunings that guarantee the long life of the components; among these, the Thermal Management process is certainly among the most discussed and developed.
In this regard, the dispensing of thermo-conductive pastes, also known as gap fillers, has acquired more and more importance in the assembly processes of electrical and electronic components. In fact, we know that electric current, whether it is a power supply or generated by data transfer, generates heat; it is clear that the miniaturization of electronic components and the high speeds of today's processors have led to the need to disperse the heat generated to avoid local heating of the electronic components involved, thus safeguarding their integrity. Just think of the development of electric vehicles, where it is necessary to be able to control the high temperature generated by the charging performance and the high working voltage.
The thermo-conductive materials are then dispensed in contact with the components to allow the dissipation of the heat generated, and secondly to compensate for any play, tolerances / air gaps that are created in the assembly process of these components; thanks to their soft and flexible consistency, they allow to protect the components even from shocks or vibrations.
Generally speaking, the gap fillers are made of polymeric, silicone or epoxy material, combined with solid particles that are thermo-conductive and do not conduct electricity; here then we can find metal-based, ceramic-based or carbon-based pastes with diamond powder or carbon fibers, which often make these fluids quite expensive.
This inevitably leads to critical issues in the dispensing of these materials, given the highly abrasive nature of these pastes which come in both mono-component and bi-component form.
This is why the Dav tech solution represents a turning point for their correct dosage. The volumetric pumps for single-component PCP and those for two-component PDP are in fact the perfect solution in terms of performance and durability. The principle of the progressive cavity progressing cavity pump, the possibility of dispensing curbs rather than points, and the possibility of choosing rotors in tungsten carbide or ceramic to resist abrasiveness, instead of stainless steel, identify a solid, reliable and without even.
Beware, however, that even in choosing the power supply unit, one must be careful and not underestimate the criticalities that arise both in the dispensing phase and in the product feeding phase; that's why where the quantities require it (where a pressurized cartridge - such as Semco - was not enough), the solution that Dav tech accompanies the PCP / PDP pumps is represented by the PPE / PPE2K electric feed pumps (in the case of bi-components), which always work through the principle of the progressive cavity pump, managed by a closed-loop, servo-controlled electric motor, which allows a precisely controlled electric feedback. The result is a pumping of the product without pressure peaks, which would tend to cause stress to the product itself, favoring the separation of the gap filler precisely by virtue of the presence of thermo-conductive solid particles.
The possibility of being able to control the speed of its electric motor, allows the PPE / PPE2K pump to manage a constant pumping without peaks, which if associated with the peculiar characteristics of the PCP / PDP volumetric dosing pumps, guarantees perfect control of the Thermal Management in Assembly Applications.