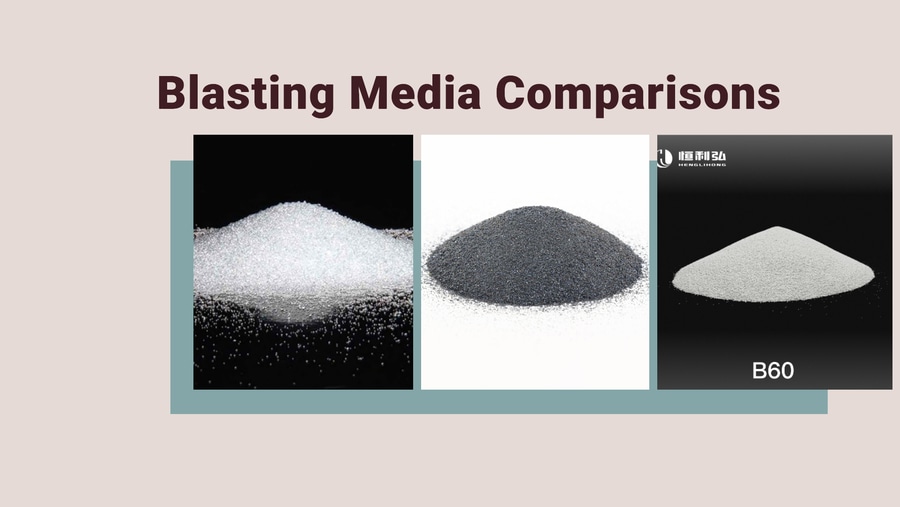
#Industry News
Which is the Best Choice for Surface Treatment: Ceramic Bead Blasting Media, Glass Beads, or Steel Shots? A Comprehensive Comparison
In the world of surface treatment, there are various media options available, each with its own advantages and disadvantages. Ceramic bead blasting media, glass beads, and steel shots are three commonly used media. But which one is the best choice?
I. Comparison of Different Media
Ceramic Bead Blasting Media
1. Applications
Automotive Industry : Used for surface treatment of car bodies, wheels, and components, providing wear - resistant and corrosion - resistant surface protection.
Glass Manufacturing : Used for sandblasting treatment of glass surfaces, increasing the texture and aesthetic appeal of glass, as well as its anti - slip performance.
Metal Processing : Used for removing oxide layers, cleaning, and increasing the roughness of metal surfaces, providing a better base for subsequent coatings or painting.
Mold Manufacturing : Used for surface treatment of molds, increasing the roughness of mold surfaces, and facilitating the formation of plastic or metal materials.
2. Effects
Precision Control : The surface treatment effect can be precisely controlled by adjusting parameters such as blasting pressure, blasting time, and blasting angle.
High - quality Surface : It can remove dirt, oxide layers without damaging the base material, ensuring the surface quality.
3. Advantages
High Hardness and Long Life : Ceramic beads have a high Mohs hardness, usually ranging from 9 to 9.5, which provides excellent wear resistance and a long service life.
Low Dust Generation : Ceramic beads are less prone to breakage during the blasting process, resulting in less dust and contributing to a cleaner working environment.
Good Material Compatibility : They are suitable for use with a variety of materials, including stainless steel, titanium alloy, and hardened alloy.
4. Disadvantages
High Initial Cost : Compared to glass beads and steel shots, ceramic beads have a higher initial cost due to the high - quality materials and complex production process used to make them.
Risk of Media Breakage : Although ceramic beads are highly durable, they may still break after long - term use, requiring regular inspection and replacement.
Glass Beads
1. Applications
Metal Surface Treatment : Used for matte surface treatment of stainless steel products, cleaning of various molds, and relieving residual stress in various machine parts to increase their fatigue resistance and service life.
Electronics Industry : Used for cleaning and deburring of circuit boards before soldering, as well as for improving the surface properties of plastic products as an additive.
2. Effects
Smooth Surface Finish : Glass bead blasting can ensure that metal and other materials obtain a smooth, satin - like surface effect without causing any surface damage.
Material Removal : It removes a thinner layer of material than other media beads, achieving a more precise and less damaging surface treatment effect.
3. Advantages
Low Hardness for Delicate Surface Treatment : With a Mohs hardness of 5 - 6, glass beads are suitable for medium - to low - intensity cleaning tasks, such as cleaning plastic molds or aluminum parts.
Low Cost : Glass beads are relatively inexpensive, making them a cost - effective option for applications where cost is a major concern.
Good Chemical Stability : They have good chemical stability and are suitable for surface treatment of a variety of materials.
4. Disadvantages
Low Hardness : The low hardness of glass beads results in lower cleaning efficiency for hard materials and a higher rate of particle breakage.
High Wear Rate : Glass beads have a high wear rate, requiring more frequent replacement of the media.
Potential for Micro - cracking : When used on high - hardness materials, glass beads may cause micro - cracks or surface damage to the workpiece.
Steel Shots
1. Applications
Automotive Manufacturing : Used to improve the strength and durability of car bodies by increasing the surface hardness of materials through shot peening, as well as enhancing the corrosion resistance of car bodies and reducing the risk of rust.
Shipbuilding, Bridge Construction, and Heavy - duty Machinery Manufacturing : Used in the pre - treatment stage of large - scale steel structures to strongly impact and remove rust, oxide scales, and impurities from the surface of steel materials, laying a solid foundation for subsequent coating operations.
2. Effects
High Impact Force : Steel shots have a high density and can apply a large impact force during the blasting process, effectively removing heavy - duty coatings and rust from the workpiece surface.
Surface Strengthening : Shot peening with steel shots can create a compressive stress layer on the surface of metal parts, effectively resisting collisions and scratches in daily use and extending the service life of products.
3. Advantages
High Impact Force and Efficiency : Steel shots, with their high density and hardness, can quickly remove rust, oxide scales, and coatings from the surface of workpieces.
Surface Strengthening Effect : Shot peening can improve the fatigue resistance of metal parts and extend their service life.
Low Cost : Steel shots are relatively inexpensive and suitable for large - scale industrial applications.
4. Disadvantages
Potential Damage to Soft Materials : The high impact force of steel shots may cause damage to soft materials or thin - walled parts.
High Equipment Cost : Shot peening requires specialized equipment, which can be expensive.
Dust Generation : Steel shots can produce metal dust during the blasting process, requiring an effective dust recovery system.
II. How to Choose the Right Media
1. Consider the Material of the Workpiece
For soft materials such as plastics, glass beads may be a good choice as they can produce a smooth surface finish without causing deep scratches. For hard materials such as metals, ceramic bead blasting media or steel shots may be more suitable.
2. Consider the Desired Surface Finish
If a smooth surface finish is required, low - hardness glass beads or ceramic beads may be the best choice. If a high - roughness surface is needed, high - hardness ceramic beads or steel shots may be more appropriate.
3. Consider the Cost
If cost is a major concern, glass beads or steel shots may be more suitable. However, it is important to consider the long - term cost, including the cost of replacement and the cost of any potential contamination.
III. Conclusion
There is no one - size - fits - all answer to the question of which is the best choice for surface treatment. The choice of media depends on a variety of factors, including the material of the workpiece, the desired surface finish, and the cost. By understanding the advantages and disadvantages of different media, you can make an informed decision and choose the right media for your specific application.