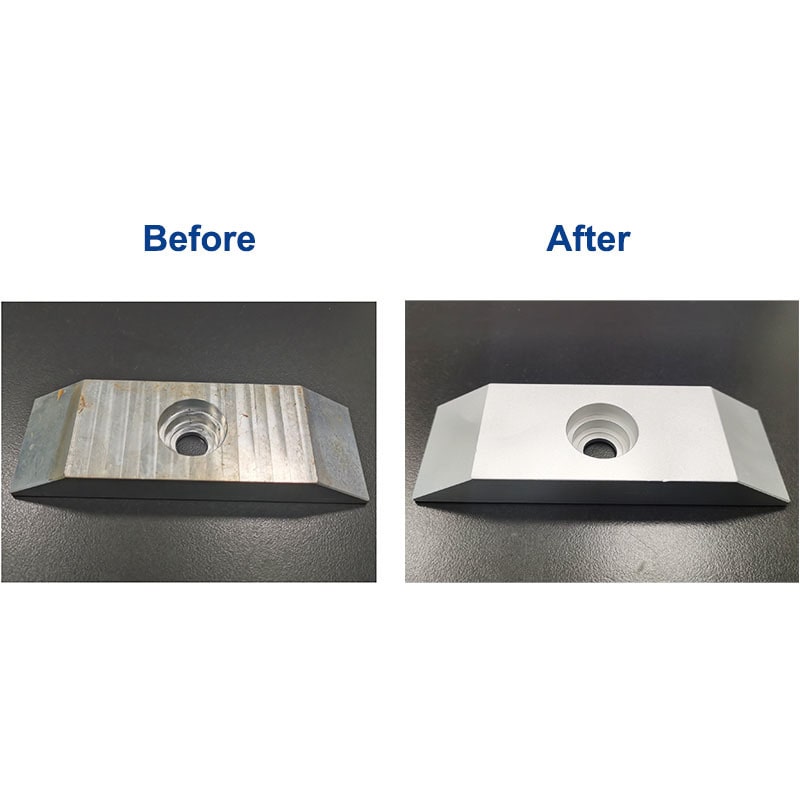
#Product Trends
The Application of Ceramic Blasting in Surface Pre-treatment
Unlocking the Power of Precision and Sustainability
Introduction
In modern industrial production, surface pre-treatment is a crucial step in ensuring product quality and performance. Ceramic blasting, as an efficient and environmentally friendly surface treatment technique, has gradually become a popular choice in the surface pre-treatment industry due to its unique advantages and wide range of applications.
1. The Principle of Ceramic Blasting
Ceramic blasting involves accelerating ceramic particles (such as zirconia ceramic sand) using compressed air or high-pressure gas and projecting them onto the surface of a workpiece. Through the impact and abrasion of the particles, the technique achieves effects such as cleaning, roughening, and strengthening of the workpiece surface. This method can effectively remove oxides, dirt, and burrs from the surface without damaging the base material while also increasing surface roughness and hardness.
2. Applications of Ceramic Blasting
Ceramic blasting technology has been widely applied in various industries due to its efficiency and environmental friendliness:
Metal Processing and Mechanical Manufacturing: Used to remove oxide scales, rust, and old coatings from metal surfaces while increasing surface roughness to provide better adhesion for subsequent coatings or painting.
Automotive Industry: Extensively applied in the surface treatment of automotive components, such as engine blocks, gears, and springs, to enhance the wear resistance and fatigue resistance of parts.
Aerospace: Used for the blasting treatment of high-precision parts made of aluminum alloys and titanium alloys, removing residual surface stresses to improve part stability and service life.
Mold Manufacturing: Used for cleaning and roughening mold surfaces to ensure better demolding performance during the forming process.
Electronics and Plastics Industry: Used to remove burrs and impurities from electronic components and plastic products while achieving a matte surface finish.
3. Advantages of Ceramic Blasting
Compared to traditional surface treatment methods, ceramic blasting offers the following significant advantages:
High-Precision Control: By adjusting parameters such as blasting pressure, angle, and duration, the surface treatment effect can be precisely controlled.
Environmentally Friendly and Energy-Efficient: No chemical solvents are required, reducing environmental pollution. Additionally, ceramic particles can be recycled, lowering production costs.
High Surface Quality: Achieves cleaning and roughening of the surface without damaging the base material, ensuring high surface quality.
Diverse Options: Different particle sizes and shapes of ceramic particles can be selected based on material and process requirements.
4. Future Development Trends of Ceramic Blasting
With continuous advancements in industrial technology, ceramic blasting techniques are also constantly innovating and optimizing. In the future, ceramic blasting will focus more on intelligent and automated control to improve production efficiency and treatment precision. Meanwhile, as environmental requirements become increasingly stringent, ceramic blasting, as a green surface treatment technology, will be applied in more fields.
Conclusion
Ceramic blasting technology, with its efficiency, environmental friendliness, and high precision, has shown great potential in the field of surface pre-treatment. Jiangsu Henglihong Technology Co., Ltd., as a leading company in the industry, is committed to providing high-quality ceramic blasting solutions to help drive the high-quality development of industrial production.
#CeramicBlasting #SurfacePre-treatment #IndustrialApplications #Eco-friendlyTechnology #HighPrecisionTreatment