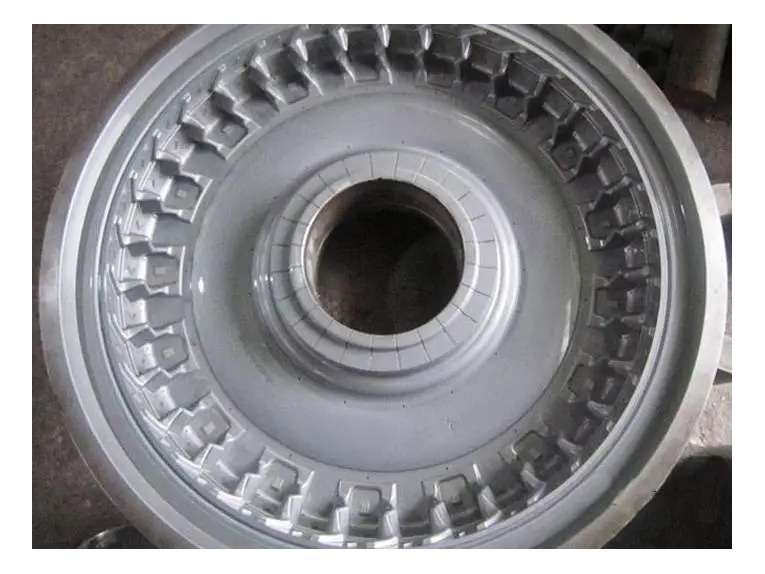
#Industry News
Extending the Lifespan of Injection Molds with Advanced SurfaceTreatment
By adopting advanced surface treatment technologies, the lifespan of injection molds can be significantly extended, maintenance costs can be reduced, and production quality can be improved.
1. The Impact of Surface Treatment on Mold Lifespan
1.1 Physical Vapor Deposition (PVD) Coating
Physical Vapor Deposition (PVD) coating is an advanced surface treatment technology that deposits a high-hardness film on the mold surface, significantly enhancing wear resistance and corrosion resistance. This technology can extend mold life by up to 30% and reduce downtime caused by wear.
1.2 Carburizing and Nitriding
Carburizing and nitriding are common heat treatment processes that significantly increase the hardness and wear resistance of the mold surface. For example, carburizing can increase mold surface hardness by 60%, effectively reducing wear.
1.3 Ceramic Bead Blasting
Ceramic bead blasting is an efficient surface cleaning and treatment method. By using high-purity ceramic beads to blast the mold surface, it effectively removes surface impurities and improves surface roughness. The ceramic beads provided by Jiangsu Henglihong Technology Co., Ltd. have precise grain size distribution, ensuring uniform surface treatment and reducing the risk of micro-cracks.
2. Practical Application Case
2.1 High-Volume Automotive Parts Production
In a practical application with an automotive parts manufacturer, the lifespan of molds was significantly extended by using advanced surface treatment technologies provided by Jiangsu Henglihong Technology Co., Ltd.. Specific measures included:
Rigorous Maintenance Plan: Regular cleaning, inspection, and preventive maintenance to ensure molds operate in optimal condition.
Surface Coating Treatment: Applying TiN (titanium nitride) or DLC (diamond-like carbon) coatings to high-wear areas of the mold to significantly enhance wear resistance.
Optimized Production Parameters: Precisely controlling the temperature and pressure parameters of injection molding machines to reduce unnecessary wear on molds.
These measures extended mold life by 20%, reducing downtime and maintenance costs.
3. Surface Treatment Standards
3.1 SPI Surface Finish Standards
The SPI (Society of the Plastics Industry) standard is a commonly used surface finish standard in the plastics industry, widely applied in mold manufacturing and injection molding. Here are several common SPI surface finish grades and their applications:
Class A (High Gloss): Suitable for products with extremely high appearance requirements, such as high-end electronic product casings. Surface roughness ranges from Ra 0.012 - 0.100 µm.
Class B (Semi-Gloss): Suitable for appliance casings, automotive interior parts, etc., with surface roughness ranging from Ra 0.05 - 0.32 µm.
Class C (Matte): Suitable for industrial components or parts, with surface roughness ranging from Ra 0.4 - 6.3 µm.
3.2 VDI Surface Finish Standards
The VDI standard is a surface finish standard widely used in Europe, with different levels of surface finish indicated by numbers. For example:
VDI 12: Surface roughness Ra 0.4 µm, close to a mirror finish.
VDI 18: Surface roughness Ra 0.8 µm, suitable for high-precision molds.
VDI 30: Surface roughness Ra 3.15 µm, suitable for general industrial applications.
4. Solutions from Jiangsu Henglihong Technology Co., Ltd.
4.1 High-Quality Ceramic Beads
The high-quality ceramic beads provided by Jiangsu Henglihong Technology Co., Ltd. have the following features:
High-Purity Materials: Ensuring excellent wear resistance and chemical stability.
Precise Grain Size Distribution: Ranging from 0.1 mm to 3 mm to meet the needs of various applications.
Uniform Surface Treatment: Reducing micro-cracks and improving mold surface quality.
4.2 Customized Services
The company offers comprehensive customized services, providing integrated solutions from material selection to surface treatment based on specific customer needs. Whether it's Class A high-gloss surfaces or Class C matte surfaces, customized treatment can be achieved.
5. Conclusion
Extending the lifespan of injection molds is key to improving production efficiency and reducing costs. By adopting advanced surface treatment technologies such as PVD coating, carburizing, and ceramic bead blasting, combined with optimized mold design and rigorous maintenance plans, mold life can be significantly extended. Jiangsu Henglihong Technology Co., Ltd., with its high-quality ceramic beads and customized services, offers one-stop solutions to help customers stand out in fierce market competition. Choose Jiangsu Henglihong Technology Co., Ltd. for longer mold life and higher production efficiency!