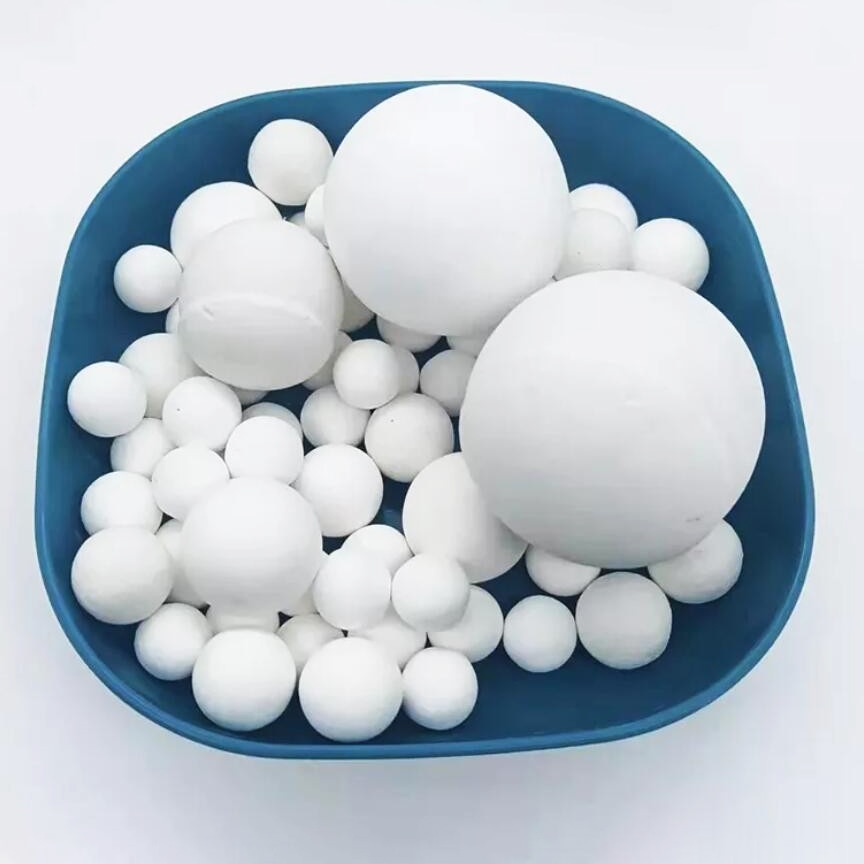
#Product Trends
How Can Polishing Alumina Grinding Balls Revolutionize Your Surface Treatment Process?
Polishing alumina grinding balls are emerging as a transformative solution in surface treatment, offering significant advantages over traditional materials.
Why Choose Polishing Alumina Grinding Balls?
1. Exceptional Hardness and Durability
Polishing alumina grinding balls, particularly those made from high-purity α-Al₂O₃, exhibit a Mohs hardness of up to 9—second only to diamond and silicon carbide. This remarkable hardness ensures efficient grinding and polishing, even on the hardest materials like ceramics and metals.
2. Low Wear Rates and Long Lifespan
Compared to traditional grinding media like glass beads, alumina balls have significantly lower wear rates. This not only reduces the frequency of media replacement but also minimizes contamination from worn particles, leading to longer-lasting performance.
3. High Purity and Chemical Inertness
High-purity alumina balls (up to 99.99% purity) are chemically inert and do not react with the materials being processed. This ensures that the final product remains uncontaminated, making them ideal for industries where purity is paramount, such as electronics, pharmaceuticals, and food processing.
4. Uniform Particle Size Distribution
Polishing alumina balls are available in a wide range of sizes, from sub-millimeter to several millimeters, with precise control over particle size distribution. This uniformity ensures consistent grinding performance and high-quality surface finishes.
Manufacturing Process
1. Raw Material Selection
The production of high-performance alumina grinding balls begins with the selection of high-purity α-Al₂O₃ powder. The purity and particle size of the raw material directly impact the final product's performance.
2. Forming and Sintering
The alumina powder is typically formed into balls through processes like rolling or drop forming. The formed balls are then sintered at high temperatures to achieve high density and strength. Advanced techniques such as hot pressing, microwave sintering, and spark plasma sintering are used to enhance the balls' mechanical properties.
3. Surface Treatment
To further enhance performance, the balls often undergo surface polishing to achieve a smooth, mirror-like finish. This reduces friction during grinding and minimizes wear.
Applications Across Industries
1. Electronics and Semiconductors
In the electronics and semiconductor industries, alumina balls are widely used for polishing silicon wafers, gallium arsenide, and other semiconductor materials. Their high purity and hardness make them ideal for achieving the ultra-smooth surfaces required in microelectronics.
2. Optics and Glass
In the optical industry, alumina balls are used for polishing lenses, mirrors, and other precision glass components. Their ability to produce high-gloss finishes without causing scratches is particularly valuable.
3. Ceramics and Advanced Materials
For the production of technical ceramics, alumina balls provide an efficient and durable grinding solution. Their high hardness and low wear rates ensure consistent particle size reduction and minimal contamination.
4. Pharmaceuticals and Food Processing
In industries where contamination is a critical concern, high-purity alumina balls are used for grinding and mixing active pharmaceutical ingredients (APIs) and food additives.
Future Trends and Challenges
1. Advancements in Manufacturing Techniques
The development of new sintering techniques and the integration of advanced materials science are expected to further enhance the performance of alumina grinding balls. For example, the use of nanotechnology could lead to balls with even higher strength and lower wear rates.
2. Environmental and Cost Considerations
As industries move towards more sustainable practices, the development of energy-efficient manufacturing processes and recyclable grinding media will become increasingly important.
3. Customization and Specialization
The demand for customized grinding balls tailored to specific applications is growing. This includes balls with specialized surface coatings, unique shapes, and tailored particle size distributions.
Conclusion
Polishing alumina grinding balls offer a versatile, high-performance solution for a wide range of surface treatment applications. Their exceptional hardness, low wear rates, and high purity make them an ideal choice for industries where precision and quality are paramount. As advancements in manufacturing techniques continue to push the boundaries of performance, the future of alumina grinding balls looks promising.