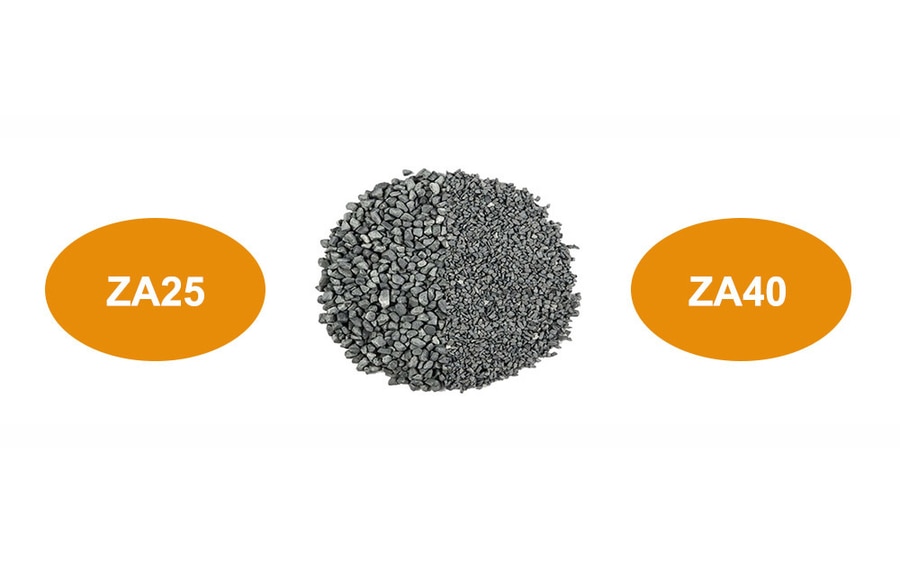
#Industry News
Which Abrasive is Right for You: ZA25 or ZA40?
Discover the Key Differences and Benefits of ZA25 and ZA40 Abrasives for Optimal Industrial Performance
In modern industrial manufacturing, the choice of abrasives plays a crucial role in ensuring both product quality and production efficiency. ZA25 and ZA40 abrasives, as two widely used high-performance abrasives, exhibit distinct advantages in various working environments and processing requirements. This article will provide a detailed overview of the applications, advantages, and selection methods for ZA25 and ZA40 abrasives, helping you choose the right abrasive based on specific industrial processing needs.
1. Applications and Advantages of ZA25 Abrasives
ZA25 abrasives are characterized by their high hardness and wear resistance, making them ideal for precision grinding and polishing processes.
1.1 Main Applications:
Precision Grinding: Due to the high hardness of ZA25 abrasives, they are widely used for precision grinding of hard materials such as metals, ceramics, and glass. They provide high-quality processed surfaces and are used in the production of precision machinery, electronic devices, and optical components.
Ultra-Precision Polishing: ZA25 abrasives are commonly used in ultra-precision polishing applications in fields such as optical lenses, hard disk manufacturing, and semiconductors, achieving micron-level precision on surfaces.
Surface Treatment: In industries such as aerospace and automotive manufacturing, ZA25 abrasives improve surface hardness and extend the product’s lifespan.
1.2 Advantages:
Strong Wear Resistance: ZA25 abrasives, with their high hardness, maintain excellent cutting performance over extended grinding periods, reducing the frequency of abrasive replacements and improving production efficiency.
High Precision: ZA25 abrasives ensure superior surface smoothness and are ideal for precision grinding that requires fine surface quality.
High Temperature Stability: ZA25 abrasives maintain stable performance under high-temperature environments, making them suitable for high-temperature grinding applications.
2. Applications and Advantages of ZA40 Abrasives
ZA40 abrasives are known for their high toughness and good thermal stability, making them ideal for various grinding and cutting applications, especially in high-speed processing and environments where heat stability is crucial.
2.1 Main Applications:
Metal Grinding: ZA40 abrasives are widely used for grinding metals such as steel and aluminum alloys. They are suitable for processing materials that are hard or prone to deformation, especially in large-scale production environments.
High-Speed Cutting: In high-speed grinding operations, ZA40 abrasives' thermal stability helps prevent abrasive wear and deformation of workpieces caused by high temperatures.
Belt Sanding: ZA40 abrasives perform excellently in sanding soft materials such as wood, plastic, and rubber, efficiently removing uneven surfaces and finding application in furniture manufacturing and automotive repair.
2.2 Advantages:
High Toughness: ZA40 abrasives have higher toughness, allowing them to withstand greater grinding pressures and are ideal for softer or more easily deformed materials.
Strong Heat Resistance: ZA40 abrasives maintain their performance in high-speed grinding and high-temperature environments, extending the life of the abrasives.
Versatility: ZA40 abrasives are not only suitable for metal grinding but also perform well in processing other materials such as wood and plastic, offering broader application scope.
3. How to Choose Between ZA25 and ZA40 Abrasives
Choosing the right abrasive is essential to ensuring both processing quality and production efficiency. ZA25 and ZA40 abrasives each have their own characteristics, and the choice of abrasive should be made based on factors such as the material being processed, precision requirements, and the specific processing method.
3.1 Based on Workpiece Material Hardness and Properties:
For processing hard materials (e.g., high-hardness alloy steel, ceramics), ZA25 abrasives are the ideal choice. Their high hardness and wear resistance ensure effective grinding over extended periods.
For softer materials (e.g., aluminum alloys, copper), ZA40 abrasives are more suitable due to their higher toughness, which reduces the risk of abrasive cracking and is suitable for processing materials prone to deformation.
3.2 Based on Precision Requirements:
For high-precision workpieces (e.g., optical lenses, precision instruments), ZA25 abrasives ensure fine surface quality and meet the strictest precision grinding requirements.
For medium-precision processing (e.g., general metal cutting or grinding with less demanding surface roughness requirements), ZA40 abrasives offer a good balance between performance and cost efficiency.
3.3 Based on Processing Method:
In high-speed grinding or high-temperature operations, ZA40 abrasives are more advantageous due to their superior thermal stability, ensuring stable performance during fast-paced and continuous grinding.
For fine grinding and ultra-precision polishing, ZA25 abrasives are optimal due to their high hardness and wear resistance, ensuring high-quality processing results.
3.4 Based on Grinding Efficiency and Economic Factors:
In large-scale production where high efficiency is required, ZA40 abrasives are ideal as they offer faster cutting speeds and better toughness, increasing overall production efficiency and reducing abrasive replacement frequency.
For processes requiring high precision and longer production cycles, ZA25 abrasives are better suited for providing consistent quality and stability, even though their grinding speed may be slower compared to ZA40.
Conclusion
ZA25 and ZA40 abrasives each offer unique advantages and are suitable for different processing needs. ZA25 abrasives are best suited for hard, high-precision grinding and ultra-precision polishing applications, while ZA40 abrasives excel in high-speed grinding and processing softer materials. By considering factors such as workpiece material, precision requirements, processing method, and efficiency, one can select the most suitable abrasive for their specific needs. A well-chosen abrasive will not only improve production efficiency but also ensure the highest quality of the final product.
Tags:
#ZA25 #ZA40 #Abrasives #PrecisionGrinding #MetalProcessing #Polishing #IndustrialManufacturing #GrindingEfficiency #AbrasiveSelection