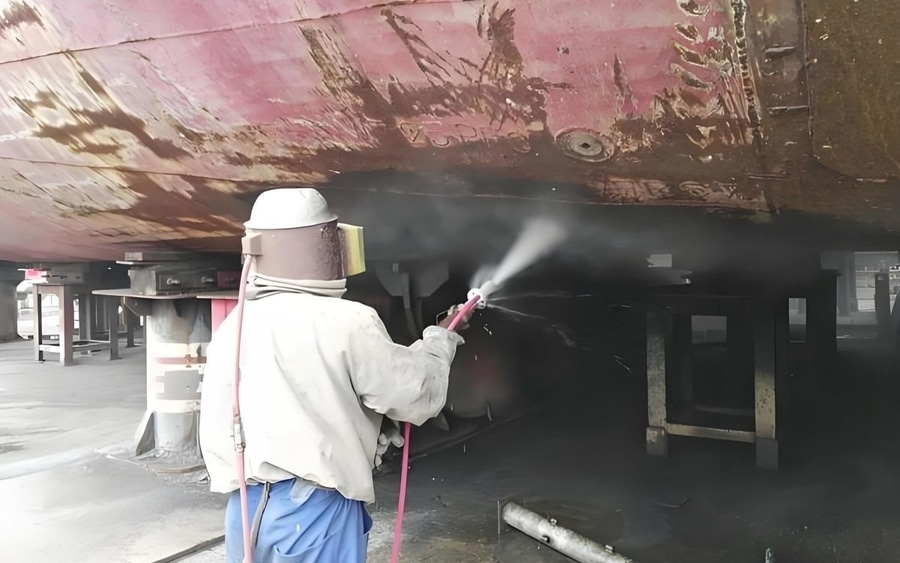
#Industry News
40% Boost in Sandblasting Efficiency? You Might Be Overlooking These Critical Parameters!
Discover how precision parameter tuning can dramatically enhance productivity, cut costs, and improve finish quality.
In the manufacturing industry, sandblasting is a widely adopted surface treatment method used for cleaning, rust removal, surface roughening, and strengthening. Despite the use of high-performance equipment, many companies still fall short of achieving expected output and quality levels. The root cause often lies not in the equipment itself—but in poor parameter configuration.
This article explores the core parameters that influence sandblasting efficiency, provides in-depth analysis of their impact on performance, and offers practical optimization strategies. These insights can help manufacturers significantly improve productivity and consistency while ensuring equipment stability.
1. Core Parameters Affecting Sandblasting Efficiency
The efficiency of sandblasting operations is primarily determined by the following parameters:
1.1 Working Pressure
This directly affects the velocity and kinetic energy of abrasives. It is a key factor in both cleaning performance and surface roughness.
1.2 Abrasive Type and Size
Different abrasive materials and particle sizes are suited for different tasks. Larger particles offer stronger impact force but lower surface refinement.
1.3 Nozzle Type and Wear Condition
Nozzle design and wear level influence the shape and consistency of the abrasive jet. Worn nozzles significantly reduce operational efficiency.
1.4 Standoff Distance and Blast Angle
Too short a distance may damage the workpiece surface; too long lowers impact efficiency. The blast angle should be adapted based on the workpiece shape and desired outcome.
1.5 Abrasive Flow Rate
Accurate control of abrasive feed rate ensures a balance between quality and operational cost.
2. Optimization Strategies for Key Parameters
2.1 Adjusting the Working Pressure
For heavy-duty cleaning (e.g., oxide removal), set pressure to 0.5–0.8 MPa.
For precision surface prep (e.g., pre-coating), maintain 0.3–0.5 MPa.
A pressure stabilizer can reduce energy waste and abrasive dispersion.
2.2 Selecting the Right Abrasive
Steel shot offers strong peening effects for metal workpieces.
Glass beads or aluminum oxide produce smoother finishes.
Avoid overly coarse abrasives that accelerate nozzle wear. Replace ultrafine dust particles in recycled media regularly.
2.3 Nozzle Maintenance
Use boron carbide or silicon carbide nozzles for extended service life.
Inspect nozzle diameter daily. Replace if wear exceeds 10%.
Venturi-type nozzles can improve blasting efficiency by over 40%.
2.4 Optimizing Distance and Angle
Recommended blast angle: 45°–75° for optimal cleaning and stripping.
Ideal standoff distance: 100–300 mm for balance between impact and coverage.
Robotic or automated blasting systems ensure uniformity and repeatability for batch processing.
2.5 Automation and Smart Control
PLC systems or HMI screens allow real-time monitoring and adjustment.
Install smart sensors to monitor abrasive flow, nozzle wear, and ambient conditions.
Closed-loop control systems help maintain stable blasting performance with minimal manual intervention.
3. Case Study: Real-World Improvements Through Optimization
A Tier-1 automotive parts supplier optimized its sandblasting equipment settings and saw remarkable improvements in production efficiency and equipment reliability:
Average processing time per part dropped from 12 minutes to 7 minutes, a 42% improvement.
Energy consumption fell from 9.2 kWh to 6.5 kWh per hour.
Surface defect rate declined from 3.1% to 0.7%, greatly enhancing product consistency.
Nozzle replacement cycle increased from 10 days to 18 days, reducing downtime and maintenance costs.
Through targeted optimization of working pressure, abrasive selection, and nozzle performance, the company achieved over 40% improvement in sandblasting efficiency, while significantly lowering operational costs.
4. Conclusion
Sandblasting performance is determined not only by the physical design of the equipment but also by how well its parameters are tuned and integrated. A systematic approach to parameter optimization enables manufacturers to enhance throughput, reduce energy consumption, and ensure high product quality.
As industrial automation advances, sandblasting is evolving toward digitized, eco-friendly, and precision-driven operations. Continuous parameter tuning, proactive maintenance, and smart system integration are key drivers for staying ahead in the competitive manufacturing landscape.
If you're looking to enhance your sandblasting system's performance or need customized optimization solutions, our technical experts are here to help. Contact us today for personalized consultation and engineering support.