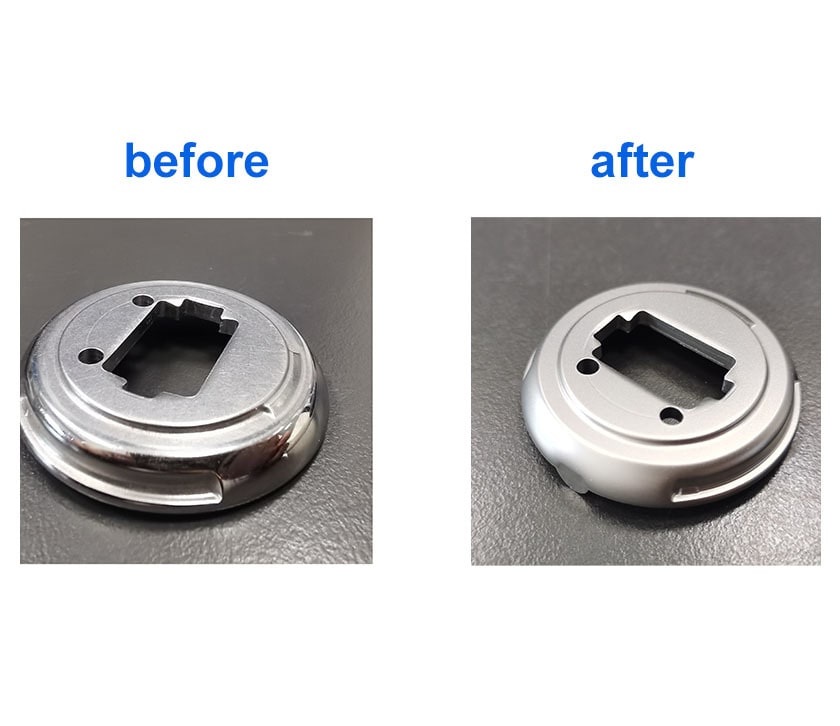
#Product Trends
Abrasive Media Basics: Essential Knowledge for Optimal Surface Finishing
Mastering the Art of Surface Perfection: A Comprehensive Guide to Selecting and Utilizing Abrasive Media
Surface finishing is a critical step in manufacturing, directly impacting product durability, aesthetics, and functionality. At the heart of this process lies abrasive media – the material responsible for cleaning, polishing, or texturing surfaces. Choosing the right abrasive media can significantly enhance efficiency and reduce costs. In this article, we break down the fundamentals of abrasive media and how to optimize your surface finishing processes.
1. What is Abrasive Media?
Abrasive media are granular materials used in blasting, grinding, or polishing to modify a workpiece’s surface. They vary in composition, hardness, and shape, each designed for specific applications.
Key Functions
Remove contaminants: Rust, oxide layers, or old coatings.
Improve adhesion: Prepare surfaces for painting or bonding.
Enhance aesthetics: Create uniform textures or mirror finishes.
2. Types of Abrasive Media
2.1 Ceramic Beads
Material: Aluminum oxide (Al₂O₃) or zirconium oxide (ZrO₂).
Advantages:
High hardness (Mohs 8-9) for tough alloys.
Reusable up to 15 cycles, reducing waste.
Ideal for precision polishing (Ra ≤0.2 μm).
Applications: Medical devices, aerospace components.
2.2 Steel Grit
Material: Carbon steel or stainless steel.
Advantages:
Fast material removal for heavy rust or scale.
Durable but limited reuse cycles (3-5 times).
Applications: Shipbuilding, automotive parts.
2.3 Glass Beads
Material: Recycled soda-lime glass.
Advantages:
Gentle finishing without embedding in soft metals.
Cost-effective for light deburring.
Applications: Electronics, jewelry.
2.4 Organic Media
Material: Walnut shells, corn cob grit.
Advantages:
Eco-friendly, biodegradable.
Safe for delicate surfaces.
Applications: Food processing equipment, historical artifacts.
3. How to Choose the Right Abrasive Media
3.1 Key Selection Criteria
Workpiece material: Hard metals require high-hardness media (e.g., ceramic beads).
Desired surface finish: Mirror polish vs. coarse texture.
Environmental factors: Dust control, recyclability.
3.2 Technical Parameters
Factor Considerations
Particle Size Fine: (0.1-0.3 mm) for polishing; coarse (0.5-1.5 mm) for heavy cleaning.
Hardness (Mohs): Match media hardness to workpiece material.
Shape: Spherical beads for uniform finishes; angular grit for aggressive cutting.
4. Common Challenges & Solutions
4.1 Media Contamination
Issue: Oil or moisture causing clogged equipment.
Solution: Pre-clean workpieces and store media in dry conditions.
4.2 Uneven Surface Finishing
Issue: Inconsistent pressure or media flow.
Solution: Use automated systems with real-time parameter monitoring.
4.3 High Operating Costs
Issue: Frequent media replacement.
Solution: Opt for long-life media like ceramic beads.
5. Innovations in Abrasive Media Technology
5.1 Smart Media Blasting
AI-driven systems adjust blasting pressure and media flow based on surface scans.
5.2 Sustainable Practices
Recyclable media: Ceramic beads regenerated via thermal sintering.
Low-dust formulations: Reduce workplace hazards and disposal costs.
6. Why Choose Henglihong Technology?
As a leader in surface finishing solutions, we offer:
Custom abrasive media: Tailored particle sizes and compositions.
Free process optimization: Test our media with your workpiece – no upfront cost.
End-to-end support: From equipment setup to operator training.
Conclusion
Understanding abrasive media is the first step toward achieving flawless surface finishes. At Jiangsu Henglihong Technology, we combine decades of expertise with cutting-edge innovations to deliver solutions that boost your productivity and sustainability.
Ready to Optimize Your Surface Finishing?