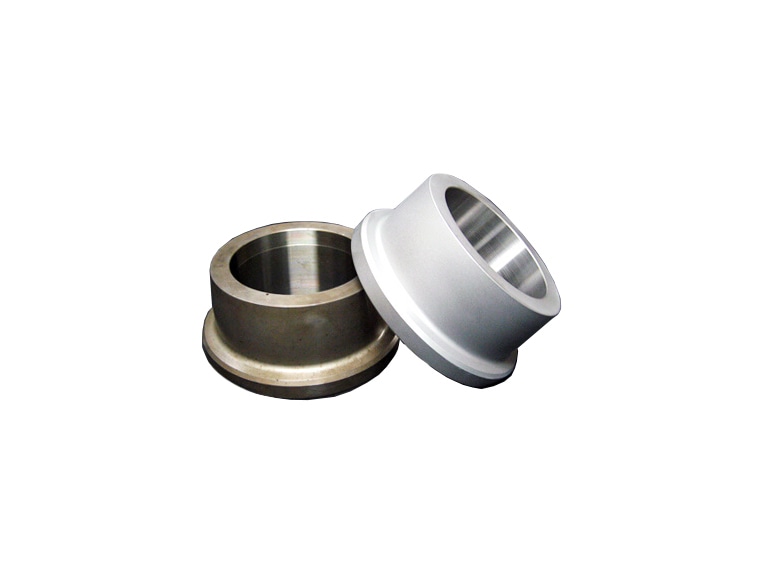
#Industry News
How Different Types of Ceramic Beads Determine Industrial Surface Roughness Parameters
Understanding the Impact of Ceramic Bead Types on Surface Quality and Precision in Industrial Applications
Preface
In modern industrial surface treatment technology, ceramic bead blasting has become a key process for achieving precise surface characteristics. Surface roughness, as a core parameter, directly affects a product's friction coefficient, coating adhesion, optical properties, and service life. This article will explore in depth the influence mechanisms of different types of ceramic beads on workpiece surface roughness and their application selection strategies in precision manufacturing.
1. Ceramic Bead Material Properties and Their Relationship with Surface Roughness
1.1 Main Ceramic Bead Types and Their Physical Properties
Alumina Ceramic Beads (Al₂O₃)
Hardness: Mohs hardness 8.5-9.0
Density: 3.6-3.9 g/cm³
Particle Size Range: Typically 0.1-3.0mm
Characteristics: High hardness, medium density, with relatively sharp fracture properties
Zirconia Ceramic Beads (ZrO₂)
Hardness: Mohs hardness 8.0-8.5
Density: 5.4-6.0 g/cm³
Particle Size Range: Typically 0.1-2.5mm
Characteristics: High density, excellent wear resistance, high sphericity after surface treatment
Yttria-Stabilized Zirconia Beads (YZ)
Hardness: Mohs hardness 8.5-9.0
Density: 6.0-6.1 g/cm³
Particle Size Range: Typically 0.05-2.0mm
Characteristics: Ultra-high density, excellent toughness and wear resistance, highest sphericity
Zircon Ceramic Beads (ZrSiO₄)
Hardness: Mohs hardness 7.5-8.0
Density: 4.1-4.7 g/cm³
Particle Size Range: Typically 0.1-2.5mm
Characteristics: Medium hardness and density, lower price
1.2 Surface Roughness Parameter System
Precise measurement of surface roughness relies on multi-parameter analysis:
Ra value: Arithmetic average roughness, the most commonly used roughness parameter
Rz value: Maximum profile height, an indicator for evaluating surface peak-valley height
Rq value: Root mean square roughness, more sensitive to extreme values
RSm value: Mean spacing of profile irregularities, characterizes the periodicity of surface texture
Rt value: Maximum height of the profile, characterizes extreme surface features
2. Influence Mechanisms of Different Ceramic Beads on Surface Roughness
2.1 Material Hardness Factor
The hardness ratio between ceramic beads and workpiece material determines the surface micro-deformation mechanism:
Hardness ratio >1.5: Dominated by cutting and scraping, producing higher Ra values and smaller RSm values
Hardness ratio 1.0-1.5: Dominated by plastic deformation, forming lower Ra values and larger RSm values
Hardness ratio <1.0: Dominated by surface compaction, mainly changing Rq values rather than Ra values
Experimental data shows that when alumina beads treat aluminum alloys, Ra values can reach 1.8-2.5μm; while using yttria-stabilized zirconia beads with the same process parameters to treat the same material, Ra values are typically 1.2-1.8μm.
2.2 Density and Impact Energy Transfer
Ceramic bead density directly affects impact energy transfer efficiency:
High-density ceramic beads (such as yttria-stabilized zirconia beads) can transfer higher kinetic energy at the same speed
Differences in kinetic energy lead to different micro-deformation depths, thus affecting Rz values
Research shows that for each 1 g/cm³ increase in density, under the same pressure and speed conditions, Rz values increase by an average of 15-20%.
2.3 Bead Size Distribution and Uniformity
Bead size distribution directly affects the uniformity of surface microtopography:
Narrow distribution bead sizes produce more uniform surface textures, with small RSm fluctuations
Wide distribution bead sizes result in larger RSm fluctuations after treatment, but help increase the density of surface micro-pits
Single-size beads are more suitable for precision optical surface treatment, with Ra value fluctuations controllable within ±0.05μm range
2.4 Bead Morphology and Surface Topography
Bead sphericity has a decisive influence on surface microtopography:
High sphericity (such as yttria-stabilized zirconia beads, sphericity >0.95) produces uniform dot-like pit textures
Low sphericity (such as some alumina beads, sphericity <0.90) tends to produce irregular scratches and directional textures
Differences in sphericity cause changes in Ra/Rz ratios, affecting subsequent coating adhesion performance
3. Ceramic Bead Selection Strategies in Different Industry Applications
3.1 Aerospace Precision Components
Aerospace requires strict control of surface roughness to ensure fatigue strength and coating performance:
Preferred Material: Yttria-stabilized zirconia beads
Particle Size Requirement: 0.1-0.3mm, narrow distribution
Target Ra Value: 0.8-1.5μm
Treatment Strategy: Multi-stage processing, large particles first, then small particles for fine finishing
Case Study: A certain engine turbine blade treated with 0.2mm yttria-stabilized zirconia beads showed 28% increase in fatigue strength and 35% extension in coating life
3.2 Medical Implants
Medical implants require specific surface roughness to promote bone integration or inhibit bacterial growth:
Preferred Material: High-purity alumina or zirconia beads
Particle Size Requirement: 0.05-0.15mm
Target Ra Value: Typically 1.2-2.0μm for titanium implants
Special Requirements: Treatment media must meet USP Class VI or ISO 10993 biocompatibility standards
Case Study: Hip implants treated with 0.1mm alumina beads showed 42% faster bone integration compared to mechanically machined surfaces
3.3 Precision Optical Components
Optical components require precisely controlled scattering properties and surface roughness:
Preferred Material: Ultra-high sphericity yttria-stabilized zirconia beads
Particle Size Requirement: 0.03-0.1mm, extremely narrow distribution
Target Ra Value: 0.05-0.5μm
Processing Strategy: Low pressure, high-precision control, usually conducted in dust-free environments
Application Example: Laser reflection mirrors treated with 0.05mm yttria-stabilized zirconia beads showed 65% reduction in scattering loss while maintaining surface shape accuracy
3.4 Automotive Engine Components
Automotive parts require balanced oil retention and wear resistance:
Preferred Material: Alumina beads or zircon beads
Particle Size Requirement: 0.3-0.7mm
Target Ra/Rz Ratio: 0.12-0.15 (this ratio optimizes oil film retention)
Application Case: Automobile cylinder blocks treated with 0.5mm alumina beads showed 2.8% reduction in oil consumption and 40% shorter break-in period
4. Process Parameter Optimization for Precise Surface Roughness Control
4.1 Key Process Parameters
The following parameters directly affect surface roughness:
Blasting Pressure: Typically in the range of 0.2-0.8MPa, each 0.1MPa increase in pressure results in an average 8-12% increase in Ra value
Blasting Distance: Typically in the range of 50-200mm, each 10mm increase in distance results in an average 3-5% decrease in Ra value
Blasting Angle: Affects the directionality of surface topography, 90° angle achieves the most uniform surface, 45° angle achieves directional texture
Treatment Time: Surface roughness grows non-linearly with treatment time, usually there is a critical saturation point
Bead Flow Density: Number of impacts per square centimeter per second, directly affects surface coverage and uniformity
4.2 Process Window Comparison for Different Ceramic Beads
Ceramic bead types include alumina beads, zirconia beads, yttria-stabilized zirconia beads, and zirconia-silica beads.
For alumina beads, the optimal pressure range is 0.3 to 0.7 MPa, with a Ra value range of 1.5 to 3.0 μm. They have moderate surface uniformity and are typically used in general industrial applications and automotive parts.
Zirconia beads have an optimal pressure range of 0.2 to 0.6 MPa and a Ra value range of 0.8 to 2.0 μm. They offer good surface uniformity and are commonly applied in precision machinery and aerospace components.
Yttria-stabilized zirconia beads feature an optimal pressure range of 0.1 to 0.5 MPa and a Ra value range of 0.3 to 1.5 μm. They provide excellent surface uniformity and are used in medical implants and optical components.
Zirconia-silica beads have an optimal pressure range of 0.3 to 0.7 MPa and a Ra value range of 1.2 to 2.5 μm. They also have moderate surface uniformity and are suitable for cost-sensitive applications.
5. Precise Measurement and Characterization of Surface Roughness
5.1 Advanced Measurement Techniques
Precise characterization of surfaces after ceramic bead treatment requires multiple complementary techniques:
Contact Profilometers: Measure one-dimensional parameters such as Ra, Rz
White Light Interferometers: Obtain three-dimensional surface topography and Sa parameters
Atomic Force Microscopy (AFM): Nanometer-level resolution surface topography analysis
Scanning Electron Microscopy (SEM): Evaluate surface microtopography and defects
5.2 Surface Functionality Assessment
Functional differences of surfaces treated with different ceramic beads can be evaluated through the following tests:
Contact Angle Measurement: Surface wettability assessment, related to surface free energy
Coating Adhesion Test: Evaluate coating adhesion strength through cross-cut or pull-off methods
Coefficient of Friction Determination: Evaluate surface tribological properties
Fatigue Strength Test: Evaluate the impact of surface treatment on component fatigue performance
6. Practical Application Case Studies
6.1 Precision Aerospace Component Surface Optimization
A certain aircraft engine compressor blade requires strict control of surface roughness to improve fatigue resistance:
Challenge: Achieve a uniform surface with Ra=1.0±0.2μm while improving fatigue strength
Solution:
Use 0.2mm yttria-stabilized zirconia beads
Processing pressure 0.3MPa
Processing distance 120mm
90° perpendicular blasting angle
Processing time 30 seconds
Results:
Obtained uniform surface with Ra=1.05μm
Surface hardness increased by 22%
Fatigue strength improved by 31%
Component service life extended by 45%
6.2 Medical Titanium Alloy Implant Surface Treatment
Orthopedic implants require specific roughness to promote bone integration:
Challenge: Create a uniform surface with Ra=1.8±0.3μm while avoiding contamination
Solution:
Use high-purity 0.15mm alumina beads
Processing pressure 0.4MPa
Processing distance 100mm
Segmented processing time: 3 times at 10 seconds each, with cooling in between
Ultrasonic cleaning after treatment
Results:
Achieved uniform surface with Ra=1.75μm
In vitro cell experiments showed 62% increase in bone cell attachment rate
Bone integration time reduced by 3 weeks in clinical applications
Implant success rate improved by 5.8%
Conclusion and Outlook
The influence of different types of ceramic beads on surface roughness is a complex and precise scientific field. Through in-depth understanding of the material properties, physical mechanisms, and process parameters of various ceramic beads, precise design and control of surface roughness can be achieved. This not only improves product performance and service life but also opens new possibilities for personalized surface treatment technologies.
With the development of materials science and surface engineering, more specialized ceramic bead materials will emerge to meet the precise requirements of various industries for surface microtopography. Especially in the medical, aerospace, and microelectronics fields, precise control of surface roughness will continue to be a key technological barrier and research focus.
#CeramicBeadBlasting #SurfaceRoughness #SurfaceTreatment #YttriaStabilizedZirconia #AluminaBeads #PrecisionManufacturing #MedicalImplants #AerospaceMaterials