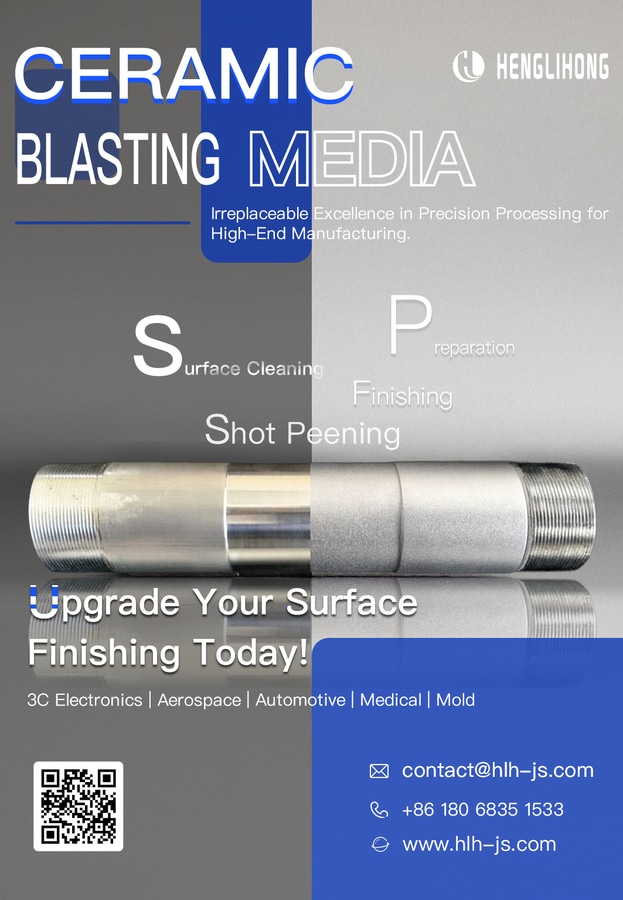
#Industry News
Industrial Applications and Prospects of Micron-Level Ceramic Bead Blasting Technology
Exploring the Future of Precision Surface Treatment in Manufacturing with Micron-Level Ceramic Bead Blasting Technology
In the field of modern precision manufacturing, surface treatment technology plays a crucial role. With the increasing demands for surface quality in high-tech industries such as electronics, aerospace, and medical devices, traditional blasting technologies can no longer meet the processing requirements at the micron level. Micron-level ceramic bead blasting technology, as an emerging high-precision surface treatment method, is gradually becoming an indispensable process in precision parts manufacturing. This article will thoroughly analyze the principles, applications, and development trends of this technology.
1. Technical Principles
1.1 Material Characteristics of Micron-Level Ceramic Beads
Micron-level ceramic beads are primarily made from high-hardness ceramic materials such as zirconium oxide (ZrO₂), aluminum oxide (Al₂O₃), or silicon carbide (SiC), with diameters typically ranging from 5 to 100 microns. These materials possess the following characteristics:
Ultra-high hardness: Mohs hardness of 8-9.5, approaching that of diamond
Excellent sphericity: Sphericity exceeding 98%, ensuring uniform contact surfaces
Chemical stability: Acid and alkali resistant, non-reactive with most metals
Dimensional precision: Uniform particle size distribution with standard deviation controlled within ±1μm
1.2 Working Mechanism
Micron-level ceramic bead blasting technology uses high-pressure air or liquid flow as a carrier to project micron-level ceramic beads onto the workpiece surface at precisely controlled speeds (20-120m/s) and angles (15°-90°). The microscopic impact effects produced by the collision of ceramic beads with the surface achieve precise modification of the surface:
Micro-cutting: The edges of ceramic beads perform micro-cutting on the surface, removing nanometer-level surface layers
Plastic deformation: Impact forces create microscopic plastic deformation on the material surface, increasing surface hardness
Nano-compressive stress: Forms a compressive stress field in the surface layer, improving fatigue strength
Surface activation: Increases surface active sites, enhancing subsequent coating adhesion
2. Equipment and Process Parameters
2.1 Core Equipment Components
Modern micron-level ceramic bead blasting systems typically include the following components:
High-precision pressure control system: Pressure fluctuation controlled within ±0.01MPa
Micron-level powder classification device: Ensures particle size consistency
Digital nozzle control system: Precisely controls projection angle and distance
Optical real-time monitoring system: Monitors processing effects and adjusts parameters in real-time
Environmental control unit: Temperature controlled at 20±2℃, humidity at 45±5%
2.2 Key Process Parameters and Control
Parameter, Control Range, Influencing Factors
Blasting Pressure: 0.1-0.8MPa, Surface roughness, processing efficiency
Bead Diameter: 5-100μm, Surface morphology, microstructure
Projection Angle: 15°-90°, Impact force direction, material removal rate
Projection Distance: 10-100mm, Energy distribution, treatment uniformity
Processing Time: 5-300s, Surface integrity, processing depth
Bead Flow Density: 2-20g/min·cm², Processing efficiency, surface quality
Precise control of these parameters is crucial for achieving ideal surface effects. Modern systems typically employ AI algorithms to assist parameter optimization, automatically generating optimal parameter combinations based on material characteristics and processing requirements.
3. Application Fields
3.1 Semiconductor and Microelectronics Industry
Precision lead frame processing: Increases bonding strength by 30-50%
Microelectromechanical systems (MEMS) cleaning: Removes microscopic contaminants, improving yield by up to 15%
Integrated circuit packaging substrate treatment: Enhances surface wettability, improving soldering reliability
3.2 Aerospace Field
Gas turbine blade strengthening: Increases blade fatigue life by up to 40%
Precision hydraulic component treatment: Reduces friction coefficient, extending service life
Aerospace fastener surface treatment: Improves hydrogen embrittlement resistance and corrosion resistance
3.3 Medical Devices
Implant surface modification: Enhances osseointegration, improves biocompatibility
Dental implant treatment: Creates microstructures that promote tissue growth
Precision medical device components: Removes micro-burrs, improving safety
4. Technical Advantages and Limitations
4.1 Advantages Over Traditional Blasting Technologies
Improved processing precision: Can achieve nanometer-level surface modification, with Ra values controllable within 0.05-1.2μm
Surface integrity: Produces virtually no microcracks or stress concentrations
Repeatability: Batch-to-batch consistency exceeding 95%
Environmental friendliness: Ceramic materials can be recycled, reducing waste generation
Precise area control: Can achieve micron-level selective area treatment
4.2 Technical Limitations and Challenges
Equipment investment cost: Professional equipment typically requires an investment of 500,000-2,000,000 yuan
Narrow process window: High parameter control requirements, difficult operation
Adaptability issues for specific materials: Such as ultra-soft materials or certain composites
Production efficiency: Smaller area treated per unit time compared to traditional methods
5. Latest Technology Development Trends
5.1 Intelligence and Digital Twins
AI-assisted parameter optimization: Reduces trial and error time by up to 85%
Digital twin technology: Real-time simulation of the blasting process, predicting surface quality
Adaptive control systems: Automatically adjusting process parameters based on real-time feedback
5.2 New Ceramic Materials
Core-shell structured ceramic microbeads: Combining high hardness and toughness
Nano-composite ceramics: Improving wear resistance and chemical stability
Functionalized ceramic beads: Surface modification with specific functional groups, achieving chemical activation
5.3 Composite Process Integration
Electrochemical-assisted micro-blasting: Combining electrochemical effects to improve material removal efficiency
Laser-enhanced ceramic blasting: Using laser pre-treatment to improve processing precision
Ultrasonic-assisted technology: Enhancing microbead impact effects while reducing projection pressure
6. Case Study: Aero-Engine Blade Treatment
An aero-engine manufacturer adopted micron-level ceramic beads (ZrO₂, 20±2μm) to treat high-temperature alloy turbine blades, achieving the following significant results:
Surface roughness optimized from Ra 1.8μm to Ra 0.4μm
Surface hardness increased by 42%, from HV320 to HV455
Surface compressive stress layer depth reached 25μm, improving fatigue life by 35%
Thermal barrier coating adhesion improved by 50%, extending service life by 2,000 hours
Production efficiency increased by 20%, with a 75% reduction in processing rework rate
This case fully validates the superior performance of micron-level ceramic bead blasting technology in high-end precision parts surface treatment.
7. Process Implementation Guide and Quality Control
7.1 Process Implementation Workflow< strong>
Pre-treatment: Ultrasonic cleaning to remove oil and particulate matter
Parameter design: Setting initial parameters based on material characteristics and requirements
Sample validation: Small batch testing and surface analysis
Formal processing: Controlling environmental conditions, executing blasting operations
Quality inspection: Surface roughness, morphology, and performance testing
Post-treatment: Neutralizing the surface, removing residual ceramic particles
7.2 Quality Control and Testing Methods
Test Item, Testing Equipment, Control Standard
Surface Roughness: Laser Confocal / Microscope, Ra ±0.05μm
Surface Morphology: Field Emission SEM, No microcracks, uniform particle distribution
Compressive Stress Layer: X-ray Stress Analyzer, Stress value -300±30MPa
Surface Hardness: Nano-indentation Tester, Hardness deviation <5%
Surface Activity: Contact Angle Meter, Contact angle reduction >40%
Conclusion
As a cutting-edge process for precision parts surface treatment, micron-level ceramic bead blasting technology continues to break the limitations of traditional processing, providing powerful technical support for high-tech manufacturing industries. Its applications in aerospace, medical devices, semiconductors, and other fields have strongly promoted technological progress in these industries. With the development of intelligent manufacturing and new material technologies, micron-level ceramic bead blasting technology will further integrate advanced concepts such as artificial intelligence and digital twins to achieve higher precision and more efficient surface treatment, bringing new development opportunities for precision manufacturing.
When introducing this technology, enterprises need to comprehensively consider investment costs, technical requirements, and application scenarios to formulate reasonable implementation strategies to fully leverage its potential in product quality improvement and cost optimization.
Keywords: #MicronCeramicBeads #BlastingTechnology #SurfaceTreatment #PrecisionManufacturing #Aerospace #MedicalDevices