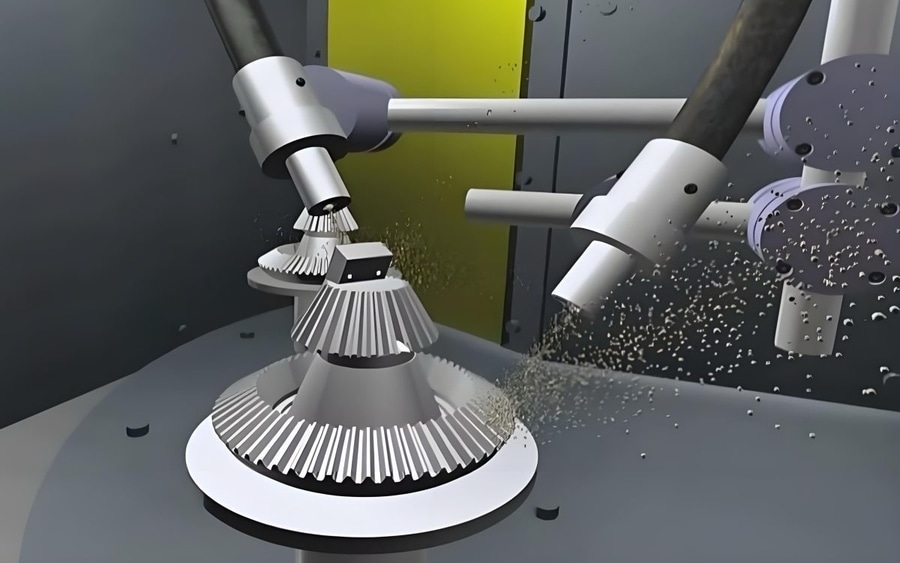
#Industry News
Ceramic Shot Peening: The Microscopic Hammers Extending Component Life by 300%
The Transformative Impact of Ceramic Shot Peening on Industrial Applications
Ceramic shot peening has emerged as an advanced surface treatment process that significantly enhances component fatigue resistance across aerospace, automotive, medical, and power generation industries. While conventional steel shot peening has been an industry standard for decades, ceramic media offers unique advantages that directly translate to superior fatigue life enhancement. This article explores the mechanisms and benefits of ceramic shot peening for extending component service life.
The Fundamentals of Ceramic Shot Peening
Shot peening is a cold working process where small spherical media impact material surfaces at high velocity, inducing compressive residual stresses. Ceramic shot peening utilizes beads typically composed of zirconia, alumina, or silicon nitride.
Key Advantages of Ceramic Media
Superior hardness-to-density ratio: Lighter than steel while maintaining excellent hardness
Chemical inertness: Resists corrosion with no metallic residue
Exceptional durability: Maintains spherical shape longer for consistent results
Clean process: Produces less dust and contamination
The Science Behind Fatigue Life Enhancement
Compressive Residual Stress Induction
Ceramic beads create a layer of compressive residual stress that extends deeper beneath the surface compared to steel media. These compressive stresses act as barriers to crack initiation and propagation—the primary mechanisms of fatigue failure.
Microstructural Refinement
The process induces plastic deformation resulting in:
Grain refinement
Increased dislocation density
More uniform microstructures
These changes disrupt crack initiation mechanisms and create more tortuous paths for potential crack propagation.
Surface Texture Optimization
Ceramic media creates an optimal surface finish that balances:
Sufficient roughness for lubricant retention
Smooth valleys to avoid stress concentration points
Uniform coverage without excessive cold working
Process Parameters Influencing Fatigue Life
Media Selection
Zirconia: Exceptional durability for high-value components
Alumina: Excellent hardness for treating harder materials
Silicon nitride: Superior performance in extreme temperature applications
Peening Intensity
Proper control of Almen intensity is crucial:
Optimal ranges typically between 0.08-0.24 mmA
Coverage levels of 98-200% provide the best results
Multiple-pass techniques can create tailored stress profiles
Process Control
Achieving consistent results requires:
Real-time velocity monitoring
Automated coverage verification
Computer-controlled nozzle movement
Statistical process control
Material-Specific Benefits and Case Studies
Aerospace Titanium Alloys
Ti-6Al-4V compressor blades: 270% fatigue life extension
Landing gear components: 180% improvement in crack resistance
One manufacturer reported $3.2 million in annual savings through extended component life
Automotive Steel Applications
Transmission gears: 200-250% fatigue life extension
Connecting rods: 150% improvement in fatigue resistance
Valve springs: 300% increase in service life
75% reduction in warranty claims reported by one premium manufacturer
Medical Implant Materials
Stainless steel implants: 200% improvement in fatigue life
Cobalt-chrome components: 170% enhancement in fretting resistance
Avoids metallic contamination issues critical in biomedical applications
Advanced Implementation Strategies
Hybrid Processing
Combining ceramic shot peening with other treatments creates synergistic effects:
Ceramic peening + laser shock peening
Pre-nitriding + ceramic peening
Ceramic peening + isotropic finishing
Targeted Peening
Advanced strategies focus treatment on specific high-stress regions:
FEA-guided intensity mapping
Masked peening techniques
Gradient peening approaches
Computational Optimization
Digital tools have revolutionized implementation:
Predictive modeling
Machine learning algorithms
Digital twins for fatigue behavior prediction
Economic Impact
Ceramic shot peening delivers compelling economic benefits:
Extended component service life reduces replacement costs
Enhanced properties enable lighter designs
Fewer in-service failures reduce warranty costs
ROI periods typically range from 6-18 months
Future Directions
Promising developments include:
Nano-ceramic media for precision applications
Cryogenic ceramic peening
Smart ceramic media providing real-time feedback
Multifunctional ceramics inducing beneficial surface chemistry changes
Conclusion
Ceramic shot peening represents a significant advancement in surface treatment technology for enhancing component fatigue life. Through optimized compressive residual stresses, microstructural refinement, and ideal surface texturing, this process delivers substantial improvements in component durability. For engineers facing fatigue-related challenges, ceramic shot peening offers a proven, cost-effective solution that extends service life and enhances overall product performance.