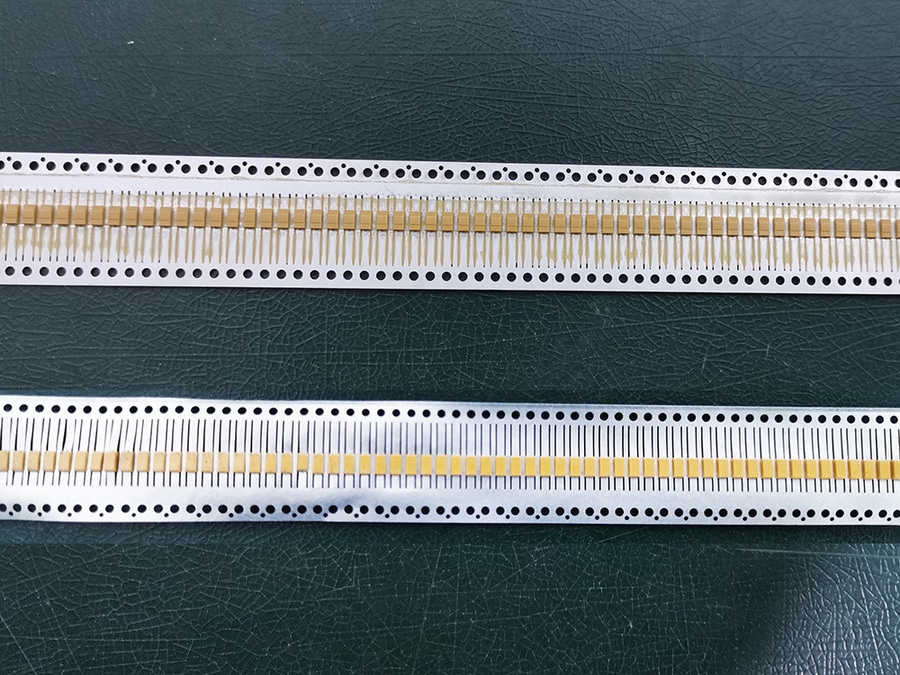
#Product Trends
Can Plastic Blasting Media Revolutionize Tantalum Capacitor Deburring?
The Game-Changing Two-Stage Approach That Delivers 95% Burr Removal Without Component Damage
Tantalum capacitors are valued in aerospace, medical equipment, and communications for their reliability ✓. However, manufacturing burrs cause performance issues and failures ⚠. Plastic media, particularly melamine and urea-formaldehyde, provide precise deburring solutions where traditional methods fail.
1. Technical Challenges
During manufacturing processes, microscopic burrs form on capacitor surfaces and lead interfaces, causing:
Electric field concentration
Short circuit risks
Encapsulation defects
Reliability degradation
Traditional methods damage dielectric layers or fail to reach complex geometries.
2. Material Properties
Melamine Media
Hardness: 3.5-4.0 Mohs
Sharp polyhedral particles
Density: 1.57g/cm³
Chemically stable
Heat resistant to 350°C
Urea-Formaldehyde Media
Hardness: 2.8-3.5 Mohs
Spherical/ellipsoidal particles
Density: 1.45g/cm³
Low moisture absorption
Reduced ESD risk
3. Process Parameters
Pressure: Melamine (1.8-2.5bar), Urea-formaldehyde (1.5-2.2bar)
Distance: 15-25cm ideal
Particle Size: Coarse (80-100 mesh), Fine (120-150 mesh)
Processing Time: 20-60 seconds
Angle: Surface (45°-60°), Lead connections (75°-85°)
Proper control achieves 95%+ burr removal without damage.
4. Application Strategy
Melamine Best For:
Larger capacitors
Severe burrs
Welding areas
Low-voltage products
Urea-Formaldehyde Best For:
Miniature capacitors
High-voltage products
Surface finishing
Precision areas
Optimal Approach: Two-stage process using melamine followed by urea-formaldehyde, improving efficiency by 30% while reducing damage risk.
#ElectronicComponents #ManufacturingTechnology #TantalumCapacitors #SurfaceTreatment #QualityControl #ManufacturingDefects #ElectricalFailure #ProductReliability #MaterialScience #PolymerPropert