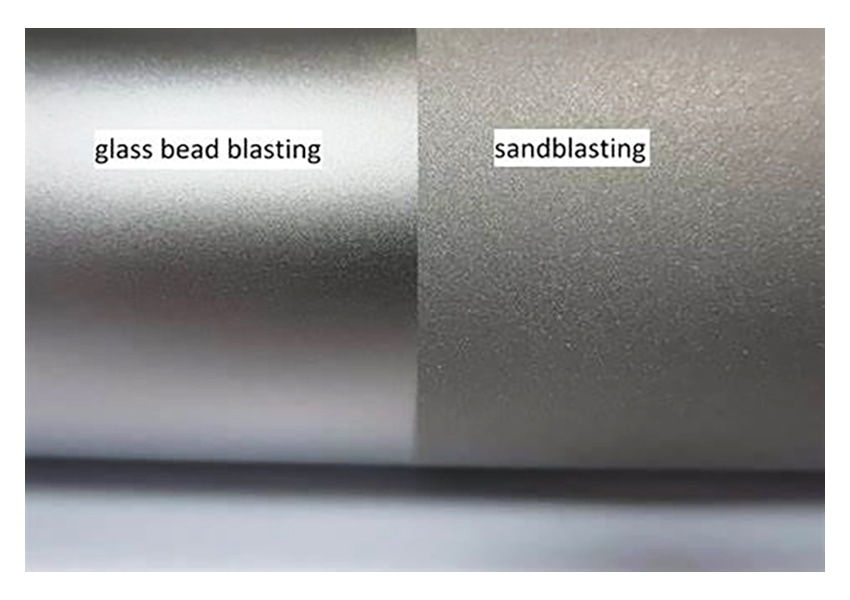
#Industry News
Comparing Sandblasting and Bead Blasting: Which is Right for Your Application?
Choosing the Optimal Blasting Method for Surface Preparation and Finishing
1. Introduction
Surface treatment is a crucial step in manufacturing, restoration, and maintenance across various industries. Among the most commonly used abrasive techniques are sandblasting and bead blasting. While both methods involve using high-speed media to clean, prepare, or finish surfaces, they differ significantly in terms of application, media type, impact on materials, and final results. Understanding these differences is essential in selecting the appropriate method for your specific requirements.
This article delves into the principles, advantages, limitations, and ideal applications of sandblasting and bead blasting, offering insights into which method best suits your needs.
2. Understanding Sandblasting
2.1 What is Sandblasting?
Sandblasting, also known as abrasive blasting, is a surface treatment process that involves propelling abrasive particles at high velocities onto a surface. The process removes rust, paint, scale, and contaminants while also preparing surfaces for coatings or refinishing.
2.2 Types of Sandblasting Media
Traditionally, silica sand was used as the primary blasting medium. However, due to health risks associated with silica dust inhalation, alternative media such as aluminum oxide, steel grit, garnet, and crushed glass are now preferred. The choice of media affects the aggressiveness of the blasting process.
2.3 Advantages of Sandblasting
Effective Material Removal: Ideal for stripping tough coatings, corrosion, and contaminants.
Wide Range of Applications: Suitable for metals, concrete, wood, and some plastics.
High Efficiency: Quickly cleans large surfaces with strong abrasion.
Surface Profiling: Creates anchor patterns that enhance adhesion for coatings.
2.4 Limitations of Sandblasting
Aggressiveness: Can damage softer materials and create surface roughness.
Dust and Health Hazards: Requires proper ventilation and protective equipment.
Potential Warping: High-pressure blasting on thin metals can cause deformation.
3. Understanding Bead Blasting
3.1 What is Bead Blasting?
Bead blasting is a gentler abrasive process that uses spherical media, such as glass beads or ceramic beads, to achieve a smooth, polished, and uniform surface finish. Unlike sandblasting, which aggressively removes material, bead blasting primarily cleans and enhances the appearance of a surface without excessive wear.
3.2 Types of Bead Blasting Media
Glass Beads: Provide a satin or matte finish, ideal for delicate surfaces.
Ceramic Beads: Harder and more durable, used for precision applications.
Plastic Beads: Used for softer materials like aluminum and composites.
3.3 Advantages of Bead Blasting
Non-Damaging to Surfaces: Suitable for fragile and intricate components.
Enhances Aesthetic Appearance: Produces a clean, uniform, and refined finish.
Improves Fatigue Resistance: Introduces compressive stress, reducing the risk of cracks.
Environmentally Friendly: Less dust production compared to sandblasting.
3.4 Limitations of Bead Blasting
Limited Material Removal: Not effective for heavy rust or thick coatings.
Slower Process: Requires more time for cleaning compared to sandblasting.
Higher Cost: Bead blasting media can be more expensive than traditional abrasives.
4. Choosing the Right Method for Your Application
4.1 Key Considerations
Material: Sandblasting is suitable for hard metals, concrete, and wood, while bead blasting is ideal for soft metals, plastics, and delicate parts.
Surface Impact: Sandblasting creates a rough texture with high abrasion, whereas bead blasting results in a smooth finish with minimal material removal.
Coating Preparation: Sandblasting effectively creates anchor patterns for coatings, while bead blasting is better suited for final polishing.
Efficiency: Sandblasting is fast and aggressive in material removal, whereas bead blasting is slower but offers more controlled finishing.
Cost: Sandblasting has lower media costs but requires more cleanup, while bead blasting has higher media costs but produces less dust and waste.
Application: Sandblasting is best for rust removal, paint stripping, and surface texturing, while bead blasting is preferred for aesthetic finishing and delicate part cleaning.
4.2 Best Applications for Each Method
Use Sandblasting When:
Removing heavy rust, old paint, or thick coatings.
Preparing surfaces for industrial coatings and adhesives.
Cleaning structural steel, concrete, or machinery parts.
Surface texturing for enhanced grip.
Use Bead Blasting When:
Finishing precision components with minimal material loss.
Cleaning delicate parts in aerospace, medical, or electronics industries.
Achieving a polished or satin finish on metals like stainless steel or aluminum.
Reducing surface stress in fatigue-sensitive applications.
5. Conclusion
Both sandblasting and bead blasting are highly effective surface treatment methods, each with distinct advantages and ideal applications. Sandblasting excels in aggressive material removal and surface preparation, making it suitable for tough industrial tasks. On the other hand, bead blasting is the preferred choice for applications requiring smooth finishes, minimal material impact, and enhanced aesthetic appeal.
By understanding the strengths and limitations of each technique, manufacturers and professionals can make informed decisions to optimize surface treatment processes, improve product quality, and enhance operational efficiency. The right blasting method depends on the specific needs of your application, material properties, and desired finish quality.