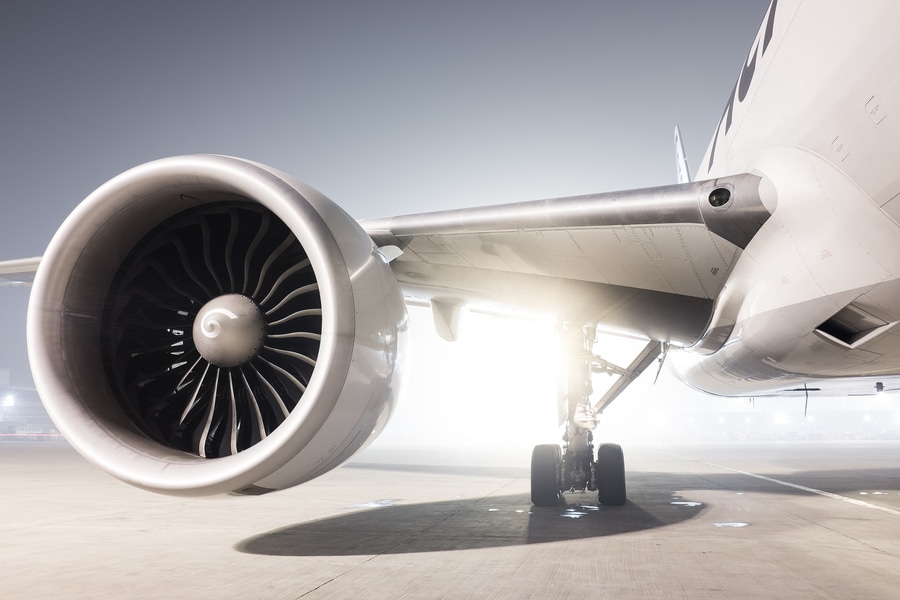
#Industry News
Optimizing Aerospace Performance: The Critical Role of Blasting Media Selection
How the Right Abrasive Can Extend Lifespan, Enhance Safety, and Improve Efficiency in Aerospace Components
1. Introduction
The aerospace industry demands the highest precision and reliability in every component, from turbine blades to structural frames. One critical aspect of manufacturing and maintenance is surface treatment, where blasting techniques are used to clean, strengthen, and prepare surfaces for coatings or bonding. However, the selection of blasting media is not a one-size-fits-all decision. The wrong choice can compromise the integrity, durability, and performance of aerospace components. This article explores the key considerations and best practices in selecting the right blasting media for aerospace applications.
2. The Role of Blasting in Aerospace Manufacturing and Maintenance
Blasting processes serve multiple functions in aerospace engineering, including:
Surface Cleaning: Removing oxidation, coatings, and contaminants to ensure optimal adhesion for coatings or bonding.
Deburring and Smoothing: Refining surfaces of machined or cast parts to meet strict aerodynamic and structural requirements.
Shot Peening for Stress Relief: Enhancing fatigue resistance by inducing compressive stress to prevent crack formation in critical components like turbine blades and landing gear.
Non-Destructive Surface Preparation: Creating a uniform texture without damaging delicate materials such as titanium or composites.
Given these varied functions, the choice of blasting media significantly impacts component longevity, efficiency, and safety.
3. Key Considerations in Choosing Blasting Media
3.1 Material Compatibility
Aerospace components are often made from specialized materials such as aluminum, titanium, stainless steel, and composite polymers. Selecting the wrong media can cause surface damage, excessive wear, or even structural weakening.
Aluminum & Titanium: Require softer media like plastic beads or glass beads to prevent over-aggressive material removal.
Hardened Steel & Nickel Alloys: Can withstand more aggressive abrasives like steel grit or ceramic beads.
Composites & Carbon Fiber: Demand delicate treatment with walnut shells or plastic media to avoid fiber damage.
3.2 Desired Surface Finish
The finish requirements vary depending on the application:
High-polish finishes for aerodynamic surfaces: Achieved using fine glass beads or ceramic beads.
Roughened surfaces for coatings and adhesives: Typically created with aluminum oxide or garnet.
Precision texturing for non-reflective coatings: Best achieved using controlled micro-abrasive blasting with silica-free media.
3.3 Media Hardness and Size
Harder media (e.g., aluminum oxide, steel grit) are effective for tough coatings but may cause surface microfractures.
Softer media (e.g., plastic beads, walnut shells) offer gentle cleaning with minimal substrate damage.
Finer media particles create smoother surfaces, while coarser particles increase surface roughness for better coating adhesion.
3.4 Environmental and Safety Considerations
Dust and Contaminants: Aerospace standards prohibit media that generate excessive dust or embed residues into the surface (e.g., traditional silica sand, which poses health risks).
Recyclability and Cost Efficiency: High-quality media like ceramic beads and steel shot can be reused multiple times, reducing operational costs.
Compliance with Industry Standards: Aerospace applications require adherence to strict regulations (e.g., AMS2431 for peening, MIL-A-22262 for abrasives).
4. Commonly Used Blasting Media in Aerospace Applications
4.1 Glass Beads
Ideal for cleaning and finishing aluminum and titanium parts.
Provides a smooth, satin finish without damaging critical dimensions.
Used for turbine blades, engine components, and fuselage panels.
4.2 Ceramic Beads
Harder and more durable than glass beads.
Offers uniform, precise surface texturing for high-performance components.
Commonly applied in jet engine parts and landing gear maintenance.
4.3 Aluminum Oxide
Highly abrasive, used for removing tough coatings and corrosion.
Suitable for steel and nickel-based alloys but too aggressive for soft metals.
Frequently used in preparing surfaces for thermal spray coatings.
4.4 Plastic Media
Provides a non-destructive cleaning process, ideal for composites and delicate components.
Used in aircraft paint stripping without affecting underlying materials.
4.5 Steel Shot & Grit
Commonly used in shot peening to enhance fatigue resistance.
Ideal for reinforcing load-bearing components such as wing spars and landing gear.
5. Case Studies: Real-World Applications of Blasting Media in Aerospace
Case Study 1: Shot Peening of Jet Engine Turbine Blades
Jet engine turbine blades experience extreme temperatures and stress during operation. By using ceramic beads for shot peening, engineers enhance fatigue resistance and extend the operational life of these critical components.
Case Study 2: Paint Stripping of Aircraft Exteriors
Aircraft undergo periodic repainting for maintenance and regulatory compliance. Plastic media blasting removes old coatings without damaging the aluminum fuselage, ensuring a smooth surface for the next layer of paint.
Case Study 3: Surface Preparation for Composite Bonding
Modern aircraft rely on composite materials for lightweight strength. Walnut shell blasting is employed to clean and texture carbon fiber panels without fraying or delamination, optimizing adhesion for structural bonding.
6. Conclusion
Selecting the right blasting media is a critical factor in ensuring the performance, durability, and safety of aerospace components. The aerospace industry’s strict requirements necessitate careful consideration of material compatibility, surface finish, media properties, and environmental impact. By making informed choices, manufacturers and maintenance teams can enhance efficiency, reduce costs, and improve the longevity of aircraft components. Whether it’s precision shot peening for jet engines or delicate cleaning of composite airframes, the right media choice can make all the difference in aerospace excellence.